Учебное пособие
для студентов специальностей 17.07.00 «Машины и аппараты текстильной и легкой промышленности», 28.08.00 «Технология швейных изделий» и
28.08.09 «Конструирование швейных изделий»
Утверждено в качестве учебного пособия
Редакционно-издательским советом МГУДТ
Авторский знак
Куратор РИС Зайцев А.С.
Работа рассмотрена на заседании кафедры машины и аппараты легкой промышленности
Зав. кафедрой Сторожев В.В. д.т.н. проф.
Авторы: П.М. Петров, к.т.н.,
В.И.Фомичев, к.т.н.
Рецензент: доцент Лопухина И.В., к.т.н.
Петров П.М. Регулировки механизмов швейных машин. Петров П.М., Фомичев В.И. – М.: ИИЦ МГУДТ, 2007 – стр.
Рассмотрены основные принципы выполнения регулировок в швейных машинах.
Дано конструктивное оформление, описание устройства и работы отдельных механизмов и узлов. Даны практические рекомендации по выполнению наладочных и технологических регулировок.
Предназначена в качестве учебного пособия для студентов специальностей 17.07.00 «Машины и аппараты текстильной и легкой промышленности», 28.08.00 «Технология швейных изделий» и 28.09.00 «Конструирование швейных изделий»
Московский государственный университет
дизайна и технологии, 2007
ВВЕДЕНИЕ
Успешное осуществление технологического процесса изготовления швейных изделий во многом зависит от исправности используемого оборудования. Основным оборудованием швейного производства являются швейные машины, как общего, так и специального назначения. В процессе эксплуатации, даже при надлежащем обслуживании, нередко возникает необходимость произвести частичную или полную разборку отдельных механизмов или всей машины. При сборке требуется обеспечить правильное положение деталей и рабочих элементов машины, т.е. осуществить наладочные регулировки. Кроме того, даже при эксплуатации исправной машины при смене технологической операции, материала и т.п. возникает необходимость изменения параметров работы машины, таких, как длина стежка, закрепки, петли; ширины зигзага; давления или высоты прижимной лапки и т.п., что требует соответствующих регулировок. При достаточно высокой квалификации данные регулировки выполняет сам оператор машины. Роль инженера-механика или технолога заключается в обеспечении соответствующего уровня знаний у оператора. В современном производстве используются разнообразные машины как отечественных, так и многочисленных зарубежных фирм. Принципы регулировок, используемых во всех машинах, одинаковы и весьма немногочисленны, хотя и отличаются конструктивным исполнением. Понимание принципов регулировок и их осуществления позволит разобраться в конструктивных особенностях механизмов любой машины и обеспечить ее наладку на выполнение требуемой операции по заданным параметрам.
Данное пособие предполагает дать необходимые знания студентам для последующей практической деятельности, а также при выполнении лабораторных работ, курсового и дипломного проектирования.
РЕГУЛИРОВКИ МЕХАНИЗМОВ ШВЕЙНЫХ МАШИН
Регулировки подразделяются на наладочные и технологические.
Н а л а д о ч н ы е регулировки осуществляются механиком с помощью инструмента при ремонте или техобслуживании машины, вышедшей из строя или не обеспечивающей требуемого качества выполнения швейной операции. Также они необходимы при замене отдельных деталей или рабочих органов машины, что требуется, например, при смене технологической операции, выполняемой на машине.
Т е х н о л о г и ч е с к и е регулировки выполняются, как правило, оператором машины без использования слесарного инструмента. Они заключаются в изменении параметров осуществляемой на машине операции. Это, как упоминалось выше, в первую очередь: изменение длины стежка, ширины зигзага, размеров закрепки или петли, глубины захвата ткани на машинах потайного стежка, степени посадки, растяжения или присборивания ткани и т.п. в зависимости от назначения машины.
Т р е б о в а н и я к регулировкам. Они по своему устройству (если оно позволяет) должны:
Обеспечивать изменение перемещения рабочих органов машины в пределах, определяемых ее технической характеристикой;
Сохранять (если позволяет конструкция) необходимое взаимное расположение рабочих инструментов при регулировке величины их перемещения;
Быть независимыми, т.е. такими, чтобы при регулировке одного параметра работы механизма, не менялся другой параметр, который не требует изменения;
Производиться, по возможности, вручную (без применения инструмента) оператором машины при изменении технологических параметров работы машины;
Быть доступными для их осуществления.
Р а з л и ч а ю т 4 вида регулировок:
I – в е л и ч и н ы перемещения исполнительных элементов машины;
II – п о л о ж е н и я рабочих органов или деталей;
III –с в о е в р е м е н н о с т и (синфазности) перемещения рабочих орга-
нов машины относительно друг друга;
IV – с и л ы давления, прижатия, торможения и т.д.
2. Швейные машины для выполнения операций групп Iа и II
4. Швейные машины для выполнения операций группы Iб
5. Оборудование для выполнения операций типа I и II в автоматическом режиме
6. Оборудование для выполнения операций, относящихся к III группе
7. Оборудование для выполнения операций IV группы
9. Столы для швейных машин
Библиографический список
1. Типовые элементы швейной сборочной операции
Любой вид одежды – изделие сложное. И, как каждый сложный объект, состоит из отдельных деталей, соединённых тем или иным способом: с помощью ниток, сварки, клея, ультразвуковым воздействием. Наиболее распространённым типом соединения (95 % от всех) является ниточное, которое реализуется на практике с помощью швейной машины или вручную, но последнее при промышленном производстве одежды применяется крайне редко.
Соединение нескольких слоёв материала, сложенных определённым образом, называется швом, а ниточная составляющая шва – строчкой.
Строчка состоит из повторяющихся элементов, расположенных между двумя соседними проколами иглы и представляющих собою законченное переплетение ниток, которые называют стежками.
При этом наиболее употребляемые типы стежков: цепной однониточный, цепной двухниточный, двухниточный челночный, краеобмёточный и стачивающе-обмёточный (стежки классов 100, 300, 400).
Для того чтобы осуществить соединение деталей одежды, в общем случае нужно: установить (положить) заготовки на рабочую позицию, провести непосредственно рабочий процесс соединения и снять полуфабрикат, над которым совершены необходимые действия. Нужно заметить, что очень часто одновременно с процессом соединения проводятся другие воздействия на заготовки: формование (подгибка), резание, смещение слоёв в пакете и другие, в связи с этим устройство, обеспечивающее в целом рабочий процесс, должно содержать соответствующие органы: челнок (петлитель), двигатель ткани, нитепритягиватель, ножи и др.
Все эти органы и механизмы и узлы, приводящие их в движение, собранные в одном агрегате, и составляют устройство, называемое швейной машиной. Различных видов швейных машин довольно много, и, естественно, это многообразие нужно упорядочить. Известны различные варианты классификации швейного оборудования: по типу выполняемых стежков, по виду обрабатываемых материалов, по специалазации, по скоростным характеристикам, по виду отдельных элементов конструкции и др. (см. раздел 5.1).
Учитывая, что в последнее время много внимания уделяется автоматизации швейного производства, представляется целесообразным в основу классификации положить технологический принцип, выделив характерные элементы процесса сборки швейного изделия. Основы такого подхода разработаны в Центральном Научно-Исследовательском Институте Швейной Промышленности (ЦНИИШП) в 1970–80 гг.
Рассматривая всю совокупность швейных сборочных операций, принято выделять несколько основных их типов, базируясь на видах используемых строчек. В таблице 1 приведены 6 из них, наиболее часто встречающихся в процессе изготовления одежды, при условии, что полуфабрикат может быть разложен на плоскость.
Таблица 1
Типовые сборочные операции
Груп-па | Под-груп-па | Эскиз | Час-тость | Характеристика операции |
операций |
I | ![]() ![]() |
Соединение деталей прямолинейной строчкой челночного или цепного стежка, начало и конец строчки выходят за край полуфабриката Соединение деталей прямолинейной строчкой с закрепками |
Стачивание подбортов или нижних воротников из частей; выполнение вытачек Обработка входа в карман; застрачивание шлицы |
||
![]() ![]() |
Соединение деталей криволинейной строчкой Соединение деталей криволинейной строчкой при строгой взаимной ориентации шьющей головки и полуфабриката |
Стачивание боковых срезов брюк; стачивание внутренних срезов рукавов; обмётывание срезов Стачивание срезов деталей с одновременным обмётыванием или обрезкой |
|||
III | ![]() |
0,12 | Соединение деталей строчкой сложной конфигурации | Выполнение закрепок, отделочных строчек; обмётывание петель | |
IV | ![]() |
0,06 | Обтачивание деталей, прокладывание отделочных строчек | Обтачивание воротников, манжет, клапанов, бортов |
Самые распространённые (47 %) – строчки по прямолинейным контурам челночным стежком, цепным двухниточным, краеобмёточным (I группа).
Здесь возможны два варианта: строчка в своих концах не закрепляется, просто выходит за край пакета полуфабриката (Iа) или строчка требует закрепления (Iб), предохраняя выполненный шов от распускания как во время последующей сборки изделия, так и при эксплуатации.
Закрепление шва осуществляется либо обратной строчкой на длину 7÷10 мм, либо учащением стежков в концах строчки, либо закрепляющей строчкой III группы (табл. 1). Характерным примером таких операций служит выполнение строчек при изготовлении прорезных карманов.
Операции, где вид строчки характеризуется небольшим отклонением от прямой (II группа), выполняются челночным или цепным стежком. Закрепки, как правило, не выполняются. Таких строчек в общем объёме до 15 %. В этой же группе есть операции (тип II б), при выполнении которых нужно обеспечить одно очень важное условие – стабильную ориентацию рабочих инструментов, взаимодействующих с полуфабрикатом, относительно контура строчки в каждый момент времени от начала и до конца операции. Примерами таких операций являются стачивание боковых срезов брюк на машине для одновременного стачивания и обмётывания, соединение на такой же машине срезов рукавов платья, обмётывание половинок брюк на краеобмёточной машине.
Если в рабочей головке имеется нож для подрезания припуска эквидистантно линии строчки, то для правильной и стабильной работы требуется выполнить условие по жёсткой его ориентации относительно контура строчки, и подобные операции (стачивание с обрезкой) также относятся к группе II б.
При ручном сопровождении полуфабриката под рабочими органами шьющей головки требование по ориентации выполняется как бы «само по себе» и сложностей не вызывает, но при создании оборудования полуавтоматического действия, где оператор не влияет на проведение рабочего процесса, приходится такое положение учитывать, создавая для этой цели специальные технические средства. Поэтому сборочные операции со строгой взаимной ориентацией рабочих инструментов и обрабатываемых деталей вынесены в отдельную подгруппу.
Тип операции III. В контуре встречаются резкие переломы; стежок, как правило, челночный, но возможен и цепной. На долю таких операций приходится до 12 % всех работ, выполняемых с помощью ниточного соединения. Примерами операций такого типа является выполнение закрепок, прикрепление пуговиц, эмблем и других мелких деталей, обмётывание петель, выполнение отделочных строчек на карманах джинс.
И, наконец, последний тип операций связан с выполнением строчки по контурам произвольной конфигурации, встречающейся, как правило, при обтачивании деталей – клапанов, воротников, манжет, бортов. В процессе работы требуется обеспечить постоянство направления подачи относительно рабочих органов, осуществляющих переплетение ниток и подрезку припуска. Это специфическое требование связано с технологическими особенностями образования стежков и принципами резания материалов устройствами типа ножниц.
Все рассмотренные строчки могут выполняться на различных материалах. Их ассортимент чрезвычайно велик. От очень тонких и мягких до достаточно толстых и жёстких. Используются материалы сухие и эластичные, устойчивые и тягучие, ворсистые и гладкие. И на всех материалах или пакетах из них должна быть проложена качественная строчка, то есть без пропуска стежков, со стабильной их длиной, без посадки и стягивания или с заданной посадкой и с необходимой затяжкой ниток в стежке.
Понятием «Типовые сборочные операции» охватывается порядка 80 % всего объёма ниточных работ. На остальные приходятся либо комбинации выделенных строчек, либо строчки на объектах, не раскладывающихся на плоскость.
Нужно ещё иметь в виду, что и в каждом «типовом» случае могут быть технологические разновидности, и их, как и в основном варианте, нужно уметь осуществить, желательно с помощью производительных и надёжных технических средств.
Машиностроительные фирмы предлагают потребителю весьма значительную номенклатуру, из которой всегда возможно выбрать то, что наиболее подходит по технологическим и экономическим показателям.
2. Швейные машины для выполнения операций групп I а и II
Сборочные операции, по приведенной классификации относящиеся к группам Iа и II, самые распространённые. Выполняются они челночным, цепным и краеобмёточным стежками и их комбинациями. Закрепление от распускания строчки в её начале и конце при этом не производится.
Очень многие фирмы выпускают оборудование для подобной цели, и крупные с мировой известностью, и более мелкие. Как правило, такая техника выпускается в виде группы машин на одной конструктивной основе.
Одноигольные машины челночного стежка – базовый ряд «Juki» – 9000 DDL; базовый ряд «Pfaff» – 1160, 1180 и 2235; базовый ряд «Durkopp/Adler» – 271.
Двухигольные машины челночного стежка – базовый ряд «Juki» – LH и LU, базовый ряд «Pfaff» – 1120; базовый ряд «Global» – DN9200; «Mitsubishi» – LU-2.
Машины, выполняющие зигзагообразную строчку – базовый ряд «Juki» LZ, базовый ряд «Brother» – ZE.
Машины краеобмёточные и стачивающе-обмёточные – базовый ряд «Juki» – МО; «Pegasus» – EX 3200 и ЕХ-5200; «Siruba» – 700 F, 700 FX, 700 FS.
Цифры и буквы здесь никакой дополнительной информации не несут, это только условное обозначение.
В связи с тем, что сегодня конструктивные новинки очень быстро становятся достоянием всех машиностроительных фирм, то можно прямо сказать, что в основе машины разных производителей примерно одинаковы и отличаются не очень существенными деталями. Поэтому для понимания вопроса достаточно рассмотреть одну из типовых машин. Что мы и будем делать в дальнейшем, беря за прототип одну из моделей известных фирм.
Рассмотрим в качестве примера одну из последних разработок фирмы «Garudan» (Чехия) машину серии GF-115.
Машина предназначена для соединения деталей швейных изделий однолинейной строчкой двухниточного челночного стежка (рис. 1).
швейный машина стол сборочный операция
Рис. 1. Общий вид промышленной швейной машины
Она состоит из шьющей головки, которая установлена на крышке промышленного стола. На столе смонтированы катушечная стойка, электродвигатель в одном блоке с фрикционной муфтой, выключатель электропитания, педаль управления и коленоподъёмник нажимной лапки. Машина вобрала в себя все достоинства предыдущих конструкций и при этом достигнут низкий уровень шума и вибраций, что создаёт оператору комфортные условия работы.
Основными рабочими органами шьющей головки являются: прямая игла, совершающая возвратно-поступательные движения в вертикальной плоскости, вращающийся челнок с горизонтальной осью вращения, нитепритягиватель шарнирно-стержневого типа, нижняя зубчатая рейка в качестве двигателя ткани и шарнирная нажимная лапка.
В машине предусмотрено регулирование длины стежка, натяжения игольной и челночной ниток, усилия прижима обрабатываемого материала лапкой, натяжения приводного ремня, связывающего привод машины с главным валом шьющей головки, хода педали управления, высоты стола.
Зубчатая рейка механизма двигателя ткани может подавать заготовки в прямом и обратном (на работающего) направлениях. Для перехода на обратное транспортирование необходимо нажать до упора вниз рычаг, расположенный на колонке рукава шьющей головки. Применяется обратная подача, как правило, для закрепления строчки путём прохода несколько раз по одному месту. Но, как мы указывали выше, при прокладывании строчек, относящихся к группам I и II, закрепки не требуются. Рассмотренная функция остаётся в резерве и будет использована при выполнении других видов строчек, в частности, типа I б. Этот момент будет отмечен в соответствующем разделе.
Прижим материала к игольной пластине и зубчатой рейке производится нажимной лапкой, которая поднимается для закладывания под неё заготовок ручным рычагом или коленоподъёмником.
Устройство для намотки ниток на шпулю расположено справа от шьющей головки на столе машины и приводится в действие от контакта с клиновым ремнём привода. При полном заполнении шпули ниткой моталка автоматически отключается.
Машина имеет масляный картер и насос для автоматической подачи масла на все трущиеся поверхности деталей, включая зону челночного устройства.
В машине регулируются также:
Подача масла к узлам трения;
Усилие и ход компенсационной пружины, воздействующей на игольную нитку;
Положение стержня нажимной лапки по высоте;
Положение транспортирующей зубчатой рейки по высоте и углам наклона;
Момент начала продвижения материала;
Длина нитки, вытягиваемая нитепритягивателем.
Для работы швейное машинное масло заливается в масляный поддон до уровня верхней отметки. Во время работы за подачей масла можно вести визуальное наблюдение через прозрачный колпачок на верхней крышке рукава.
Подача масла к нитепритягивателю регулируется поворотом винта, который находится за фронтовой крышкой.
К челноку масло поступает через дозирующий винт, ввёрнутый во втулку вала челнока. Такая тонкая регулировка минимизирует поступление масла к упомянутым узлам и уменьшает вероятность загрязнения сшиваемых заготовок.
Установка по времени взаимодействия иглы и челнока осуществляется по рискам, нанесённым на игловодитель.
Наклон транспортирующей рейки по отношению к верхней плоскости игольной пластинки влияет на качество соединения заготовок. Изменение положения рейки осуществляется поворотом эксцентрика её подъёма. Другим эксцентриком, установленным на главном валу головки, регулируется начало взаимодействия рейки с материалом, то есть начальный момент продвижения.
Область применения подобных машин (различных фирм) охватывает весь основной диапазон обрабатываемых текстильных материалов: ткани лёгкого, среднего и тяжёлого веса.
Краткая техническая характеристика машин базового ряда GF-15 приведена в таблице 2.
Таблица 2
Некоторые модификации машины GF -115
Технологические требования к швейной операции ассортиментом тканей и типом стежка не ограничивается. Важными характеристиками также являются:
Вид строчки: беспосадочная, с посадкой верхней или нижней детали;
С посадкой верхней и нижней детали;
Наличие поперечных швов и утолщённых участков;
Допускаемые отклонения в ширине шва.
Эти требования определяют наличие технических средств, которые должны присутствовать в машине, отвечающей конкретным условиям пользования. В связи с этим номенклатура вариантов машины существенно расширяется. В таблице 3 приведены самые распространённые.
Таблица 3
Некоторые конструктивные варианты
на базе одноигольной челночной машины
Могут быть и другие особенности. У ряда фирм этот перечень расширяется за счёт моделей с увеличенным челноком, с нижней дифференциальной подачей, с устройством для управления сборкой ткани.
Известны также модели, где могут быть собраны упомянутые возможности в других комбинациях, например, увеличенный челнок плюс дифференциальная подача.
При изготовлении одежды часто приходится прокладывать одновременно две параллельные строчки. Многие из таких операций также могут быть отнесены к подгруппам Iа и IIа. Выполняются эти операции с помощью двухигольных машин (рис. 2).
Рис. 2. Двухигольная швейная машина
Основных вариантов здесь два: с нижней реечной подачей и с реечной вместе с игольной. Краткая техническая характеристика машин дана в таблице 4.
Таблица 4
Варианты исполнения двухигольных машин
В машине используются челноки с вертикальной осью вращения, которые работают при неподвижной шпульке. Ход левого и правого нитепритягивателя регулируется отдельно.
Смазочная система полностью автоматизирована.
Конструктивное развитие машина получила при выпуске модели LH-3168, где применён механизм раздельного отключения игл, что позволяет при одном размещении полуфабриката выполнять либо правую, либо левую строчки. Особенно это важно при прокладывании отделочных строчек на деталях с резким переломом профиля, например, на карманах.
В работу механизм включается лёгким нажатием рычага, удобно размещённым близ зоны шитья.
Вариант LH-3178 снабжён увеличенными челноками.
Строчки могут находиться на различном расстоянии друг от друга, в связи с чем к машинам прилагаются сменные комплекты иглодержателей, лапок, реек, игольных пластин. Стандартные расстояния между иглами: 2,4 мм; 3,2 мм; 4,0 мм; 4,8 мм и т.д. до 38,1 мм.
На этой же базе может быть выполнен одноигольный вариант. Версия DU-1181 с верхней и нижней подачей и увеличенным вдвое челноком предназначена для шитья тяжёлых тканей. Вылет рукава 260 мм.
У этой машины величина стежка до 9 мм и может регулироваться в обоих направлениях подачи. Величина чередования вертикального перемещения шагающей и прижимной лапок регулируется в диапазоне от 2 до 5 мм, в зависимости от толщины материала и числа слоёв.
Применяемые нитки достаточно толстые от № 40 до № 8.
Высокий подъём лапки позволяет выполнять операции на многослойных пакетах.
Максимальная частота вращения главного вала – 2000 об/мин.
К операциям типа Iа и II относятся и ситуации, реализуемые зигзагообразными строчками. Характерным примером операции является настрачивание нижней части воротника на верхнюю при его заготовке в технологических процессах сборки пиджака.
Зигзагообразные строчки могут быть образованы как стежками челночного переплетения, так и цепными стежками.
Получают зигзаг двумя способами: либо перемещая обрабатываемый материал в необходимом направлении после каждого прокола его иглой, либо поперечным перемещением иглы относительно направления прокладываемой строчки. Первый применяется, когда длина строчки невелика, например, при вымётывании петли и пришивании пуговиц (об этом ниже). Второй вариант используется при выполнении швов, длина которых существенно превышает величину поперечного смещения иглы, то есть ширину зигзага, и рисунок строчки образуется за счёт воздействия на материал иглы и реечного транспортирующего органа.
Многие фирмы выпускают машины, выполненные по второй схеме, при этом на одной конструктивной базе выпускается несколько модификаций.
Проследим эту тему на группе машин фирмы «Shanggong» (Китай). Первый и наиболее простой тип машин для строчки «двухукольный зигзаг» кл SG2023 (рис. 3а).
Рис. 3. Машины, выполняющие зигзагообразную строчку
Машина предназначена для шитья лёгких и средних тканей. Шаг строчки – до 5 мм, ширина зигзага – до 9 мм. Скоростной режим – 2000 об/мин. Здесь зигзаг образуется путём поперечного перемещения рамки, в которой двигается возвратно-поступательно игловодитель, с помощью трёхцентрового кулачка, охватываемого вилкой, связанной с упомянутой рамкой. Смазка машины – фитильная (капельная), по точкам.
Вылет рукава около 200 мм. Существует модификация этой машины, обеспечивающая ширину зигзага до 12 мм, однако рабочая скорость здесь поменьше – 1800 об/мин. Высота подъёма лапки – 10 мм.
Вариант этой машины под маркой SG2073 имеет устройство для фиксации иглы при шитье прямой строчкой: крайнее левое, крайнее правое и среднее положение (рис. 3б).
Ещё одна разновидность – машина, выполняющая четырёхукольный (трёхшаговый) зигзаг (рис. 3в).
Но это всё машины для дома или для ателье, где нагрузки всё же не так велики, как в промышленном производстве. В качестве оборудования, выдерживающего более скоростную работу за счёт иного конструктивного решения и автоматической смазки, можно назвать машину 457А (рис. 3г). Опять здесь довольно много модификаций. В связи с чем ширина зигзага может доходить до 5 или 8 мм, длина стежка от 1,3 до 5,1 мм. Вылет рукава 260 мм. Максимальная скорость – до 5000 об/мин. Возможны варианты по тканям: лёгкий, средний и тяжёлый. При использовании машины на средних и тяжёлых материалах скорость работы снижается.
На этой же базе фирма выпускает модель для четырёхугольного зигзага и для декоративной строчки. Программа здесь задаётся копирным диском.
Замена механического управления на электронное расширяет возможности машин: возрастает число выполняемых строчек, а переход с одной на другую упрощается.
Используя стандартный рукав как базовый, группа фирм расширяет ряд за счёт соединения его с другими типами платформ: рукавной, колонковой, П-образной. Применение П-образной платформы позволяет изготавливать детали цилиндрической формы (рукава) сколь угодно большой длины.
Машины, выполняющие зигзагообразную строчку, могут комплектоваться различными дополнительными устройствами и приспособлениями – двойной иглой, тянущими роликами, окантовывателями или устройствами для пришивания резинки, ленты, кружев. В последнем случае в конструкцию машины вводится механизм для подрезки неровностей края ткани, на которую настрачиваются кружева или лента. Нож, служащий для этой цели, представляет собою планку, смонтированную над игольной пластиной, и располагается справа от иглы. Острая кромка ножа взаимодействует с краем прорези игольной пластинки, и совместно они работают как режущие кромки ножниц.
Практика часто требует не просто зигзагообразной строчки, но и выполнения некоторых особых условий. Например, для изготовления сидений автомобилей, парусов яхт, различных тентов, накидок, штор, палаток и других крупногабаритных вещей потребовалась машина с очень большим вылетом рукава, и фирмы создали такую технику (рис. 4).
Рис. 4. Швейная машина с большим вылетом рукава
Мы уже указывали, что строчки в операциях типа Iа и II могут выполняться не только челночными стежками, но и цепными, в частности, цепными двухниточными.
Эти строчки используются для соединения передних и локтевых срезов рукавов в верхней одежде, для выполнения швов спинки (в одноигольном варианте), для стачивания частей кокетки и боковых швов на джинсах, если применяется машина с двумя иглами.
Подобное оборудование выпускают фирмы «Juki» (серия МН), «Durkopp/Adler» (кл 273 и модификации), «Pfaff» (база 3811) и др. Общий вид такой машины приведён на рисунке 5.
Цепные стежки образуются у этих машин при взаимодействии иглы, движущейся возвратно-поступательно в вертикальной плоскости, и петлителя, участвующего в двух движениях – колебательном поперёк направления строчки и возвратно-поступательном вдоль неё.
Сложение этих двух движений определяет довольно непростую эллиптическую кривую фактического перемещения петлителя.
Петлитель, заправленный ниткой, снимает с иглы петлю, образующуюся после прокола ткани, обеспечивает условия для того, чтобы игла при повторном проколе прошла в области между своею предыдущей петлёй и ниткой петлителя. Эта зона в горизонтальной проекции выглядит как треугольник. На рисунке 1.3 приведён именно такой момент из процесса петлеобрезания.
Мы останавливаемся на этом специально, так как процесс закола (проход иглы в площадь нитяного треугольника) – самый ответственный при образовании стежка. Непопадание иглы в необходимую зону ведёт к пропуску стежков, что весьма нежелательно, ибо цепная строчка в таких случаях легко распускается.
Рис. 5. Швейная машина двухниточного цепного стежка
На рисунке хорошо видно, что одна из вершин треугольника из ниток уходит в строчку. Двигатель ткани (рейка), перемещая полуфабрикат, оттягивает нитки, и треугольник при этом имеет чёткие очертания, игле легче попасть в него.
Таким образом, если говорить строго, то в образовании двухниточного цепного стежка участвуют 3 рабочих органа: игла, петлитель и двигатель ткани.
При малых длинах стежка вершина треугольника, связанная со строчкой, приближается к его основанию, и площадь для закола уменьшается, а вероятность пропуска стежков увеличивается. Поэтому шаг строчки у подобных машин не может быть меньше 1÷1,5 мм.
С другой стороны, уменьшение длины стежка или выполнение их (стежков) нескольких подряд в конце шитья обеспечивает определённое закрепление строчки, вероятность распускания становится весьма малой. Необходимо только в машину ввести устройство, обеспечивающее уплотнение стежков, что ряд фирм и делает.
В связи с изложенным конструктивные особенности механизмов, приводящих в движение петлитель, и его геометрия играют решающую роль в надёжности работы машины.
Машины имеют плоскую платформу; выпускаются в двух- и одноигольных вариантах.
В двухигольных моделях иглы могут располагаться следующим образом: две иглы поперёк линии шва и две иглы вдоль линии шва (одна за другой). Правда, в последнем случае иглы в поперечном направлении всё-таки раздвинуты, но это смещение невелико, всего 0,5 мм, что позволяет прокладывать две строчки вплотную друг к другу. Шов с такими строчками более прочный, чем одинарный. Кроме того, он имеет способность при растяжении сохранять целостность ниточного соединения. Поэтому машины, обеспечивающие подобные строчки, применяют для выполнения сильно нагруженных швов. Классический пример – шов сиденья в брюках.
Машины указанных серий выпускаются с различными механизмами транспортирования: обычный вариант – нижняя рейка. Более сложные: дифференциал снизу и устройство, обеспечивающее нижнюю и верхнюю дифференциальную подачу. Такие конструктивные особенности позволяют выполнить высококачественные швы на различных материалах и в различных сочетаниях.
Скоростной режим машин от 4500 об/мин до 6000 об/мин (в зависимости от сшиваемых пакетов).
При изготовлении предметов одежды иногда используются строчки, образованные плоскими цепными стежками, относящиеся к классам 400 и 600 по ГОСТу 12807–88. Чаще такие строчки используют в изделиях из трикотажа.
Известная техника для выполнения указанных строчек – машины серии MF(«Juki»), FB («Global»), 1500 («Pegasus»).
Это двухигольные (при сменных деталях трёхигольные) машины с плоской платформой (рис. 6).
Расстояние между иглами может быть 4,8 мм; 5,6 мм; 6,4 мм (опять-таки при сменных комплектах). Подобные машины принято называть плоскошовными.
Рис. 6 Двухигольная трёхниточная швейная машина (плоскошовная)
Застил снизу строчки выполняется с помощью петлителя, колеблющегося поперёк линии строчки. Схема образования стежка приведена на рисунке 7.
Длина стежка регулируется в диапазоне 1,2÷3,6 мм. Конструктивная скорость – 6500 об/мин.
На этой базе спроектировано большое число вариантов: с разными видами платформ (плоские и цилиндрические); с разным количеством игл, с различными вариантами транспортирующих органов (обычная нижняя рейка, дифференциал, дополнительные тянущее ролики), с применением узлов для подрезки краёв полуфабриката.
Рис. 7. Один из моментов образования трёхниточного цепного стежка
Интересен вариант FS-311L41 («Juki») или FD-4 («Brother»). Это двухигольная пятиниточная машина, выполняющая строчку из плоских цепных стежков, переплетённых сверху покровной ниткой. Такую строчку принято использовать при настрачивании отрезного бочка на подкладку кармана мужских (детских) брюк. Она образуется при взаимодействии двух игл, двух петлителей и раскладчика. Строчка прямая, начало её и окончание совпадает с краем пакета заготовок. Закрепка не требуется, так как в последующих операциях эти зоны попадут под другие строчки, идущие поперёк к выполняемой.
На этой же базе выпускается многими фирмами специализированная машина (рис. 8) для изготовления шлёвок к брюкам, джинсам – MFB-2600 «Juki», SS 1112 BLF «Sunshine».
Шлёвки изготавливаются из отдельных заготовок или из ленты, полученной из предварительно соединённых друг с другом полосок ткани. Такой подход позволяет использовать небольшие выпады кроя тех же изделий, для которых изготавливаются шлёвки, что исключает необходимость подбора их по цветам и оттенкам к изготовляемой одежде.
Рис. 8. Машина для изготовления шлёвок
В машине имеется направитель, который формует заготовку, подгибая её срезы вниз перед подачей под шьющий механизм так, чтобы края находили друг на друга внахлёст. При шитье срезы снизу закрываются плоской цепной строчкой.
Для того чтобы получить одинаковость подгибки, заготовки перед формованием подрезаются с двух сторон, обеспечивая достаточно точную по ширине ленту. С этой целью машина снабжается устройством в виде двух пар ножей, механизм привода в работу которых кинематически связан с главным валом машины. Точность ленты после подрезки краёв ±1 мм, что позволяет весьма качественно сформировать шлёвку и аккуратно закрыть срезы.
После выхода из-под лапки готовая шлёвочная полоска может свободно спадать в бункер или принудительно наматываться на кассету.
Скорость шитья 5500 об/мин – это максимум. Нормальной считается скорость работы при числе оборотов главного вала 4500÷5000 об/мин.
Шаг стежка 1,2÷3,2 мм (регулируется). Расстояние между иглами 4,8 мм; 5,6 мм; 6,4 мм. Обеспечивается, естественно, за счёт смены деталей шьющего комплекта.
Ширина шлёвки в готовом виде может быть 8÷20 мм.
Смазка машины автоматическая.
Рассматриваемая база лежит в основе группы многоигольных машин, находящих широкое применение в швейной отрасли (серия МН-1410 «Juki», серия SS3400 «Sunshine» (рис. 9)).
Эти машины отличаются от описанных выше прежде всего по способу образования стежков. Рабочими органами для этого являются прямые иглы, совершающие возвратно-поступательные движения по вертикали; петлители в количестве, равном числу игл, колеблющиеся вдоль линии строчки; ширители, движущиеся поперёк строчки. Количество последних опять-таки равно количеству игл.
Рис. 9. Многоигольные швейные машины
Каждая тройка инструментов (игла, петлитель, ширитель), взаимодействуя друг с другом, обеспечивают образование двухниточного цепного стежка (рис. 10).
Рис. 10. Образование цепного стежка иглой, петлителем и ширителем
При работе транспортирующего механизма, состоящего из зубчатых реек, нажимной лапки и дополнительного узла из тянущих роликов, стежки складываются в строчку. И этих строчек машина образует столько, каково количество игл, установленных в иглодержателе. Заменяя группу деталей, можно обеспечить различное расстояние между параллельно идущими строчками. Количество игл может доходить до 12. В этом случае ширина полосы обработки составляет 70 мм.
Длина стежка плавно регулируется в диапазоне 2,1÷6,4 мм.
Максимальная скорость работы 5000 об/мин, однако её необходимо корректировать, сообразуясь с обрабатываемыми материалами, поскольку они очень разнообразны: ткани хлопчатобумажные, смешанные, плащёвые, льнолавсановые, шёлковые и полушёлковые, из синтетических нитей и мн. др.
В зависимости от технологического оснащения (приспособления для направления ткани к иглам, которые монтируются на платформе) машина может использоваться, например, при изготовлении поясов, как съёмных, так и соединённых с изделием – джинсы, спортивные брюки; при изготовлении планок на полочках сорочек; при изготовлении нескольких идущих параллельно складок. Во всех случаях строчки прямые, начало и конец их совпадает с краем пакета полуфабриката, обрезка ниток осуществляется ножницами оператором.
При изготовлении спортивных брюк или трусов одновременно с формированием пояса и шитьём в него (пояс) вставляется эластичная тесьма. Для её расправления и необходимого натяжения к платформе машины спереди крепится узел, состоящий из принудительно вращающихся роликов и подпружиненного прижима. Тесьма, проходя через это устройство, приобретает необходимое (опытным путём подобранное) натяжение, что позволяет отрезать её в точный размер.
Операции в рассматриваемых группах (Iа и II) можно проводить стачивающе-обмёточным или краеобмёточным стёжками. «Juki», «Pegasus», «UnionSpecial» и другие выпускают очень большое количество машин, реализующих эти стежки. Все фирмы создают оборудование, руководствуясь принципом образования конструктивно-унифицированных рядов, при котором на единой базе за счёт смены отдельных узлов получаются различные технические модификации.
Последнее поколение краеобмёточных и стачивающе-обмёточных машин – серия МО 6000 «Juki» (рис. 11).
Рис. 11. Базовая машина ряда краеобмёточных
и стачивающе-обмёточных машин
К настоящему времени этой фирмой разработано семь рядов машин, отличающихся скоростным режимом, видом платформы, комбинациями транспортирующих устройств, применимостью для различных типов материалов, типом стежка, расстоянием между иглами и др.
Общая классификация рядов приведена в таблице 5.
Таблица 5
Классификация рядов машин МО-6
3. Основные принципы совершенствования швейных машин
За последние несколько десятилетий специалисты, работающие в химической промышленности, металлургии, предложили практическому машиностроению большое количество новых полимерных и композитных материалов, новых покрытий, что позволило существенно усовершенствовать конструкции швейных машин, а это, в свою очередь, – расширить их возможности и области применения. Общий скачок технического уровня произошел в 80-х гг. ХХ в. Особенно это коснулось систем смазки. Если раньше применялись системы, где имелась специальная ёмкость для запаса масла и из неё с помощью насоса по трубопроводам масло подавалось в места трения, а оттуда самотёком или с помощью другого насоса (отсасывающего) сливалось обратно в эту же ёмкость, то сегодня конструкторы отказываются от применения подобных схем в пользу несмазываемых сухих головок (Dryhead).
Причина в том, что весьма затруднительно создать систему смазки, которая была бы абсолютно герметична и не допускала попаданий капелек масла, пусть даже в незначительном количестве, на обрабатываемое изделие. Есть в машине такие узлы (челнок, игловодитель), где предотвратить утечку масла практически невозможно.
Если масло свежее, оно жёлтого цвета, но если машина проработает какой-то промежуток времени, оно – чёрное, так как загрязнено продуктами износа. При попадании такой капельки на тёмное изделие большой беды не будет. Но если шьётся что-либо из светлых тканей, да ещё дорогих, тогда изделие безнадёжно испорчено. Попытки убрать следы масла химическим путём могут оставить пятна. Вот в таких случаях решение Dryhead незаменимо.
Всё это стало возможным с появлением новых композитных материалов для машиностроения. Свойства ряда этих материалов таковы, что смазывающих компонентов просто не требуется. Коэффициент трения в трущейся паре из таких материалов низкий и постоянный.
Решение Dryhead быстро завоевало популярность. Все фирмы, особенно ведущие, массово стали его использовать. Однако к настоящему времени общее восхищение улеглось. Конечно, очень хорошо, если во время эксплуатации капли отработанного масла не загрязняют обрабатываемое изделие. Но цена сухой головки оказалась довольно высокой. Фирмы более сдержанно используют этот вариант; только там, где абсолютно необходимо: изготовление изделий из светлых тканей.
Например, при шитье одежды джинсовой группы попадание мелких масляных капелек не испортит изделие, тем более что в конце технологического цикла оно (изделие) подвергается «варке» – обработке горячей водой с применением специальных химических веществ и камней. Так что все загрязнения неминуемо исчезнут. В сухом варианте головки особой надобности нет. Но это не значит, что всё остаётся по-старому. Наоборот, производители машин создают конструкции, обеспечивающие достаточную смазку трущихся деталей плюс надёжную герметизацию масляных зон в машине.
Вообще говоря, основная тенденция здесь – смешанная система: сверху сухой рукав, снизу, в платформе – масляный картер.
Исходя из этого, машина может быть с дозированной системой смазки (обозначается S, обеспечивает скорость работы 5000 об/мин), вероятность появления масляных пятен, хотя и малая, но имеется; вариант с системой М (полусухая головка) практически не оставляет масляных следов, даже при высокой скорости работы; и вариант D (сухая головка) полностью исключает масляные загрязнения, но скорость работы здесь поменьше, до 4000 об/мин.
Это первое направление.
Второе направление, на котором сосредоточено внимание конструкторов, – разработка нового привода.
Приведение в работу швейной машины осуществляется с помощью индивидуального фрикционного электрического привода, и управление им оператор осуществляет с помощью ножной педали. Электропривод состоит из однофазного или трёхфазного асинхронного электродвигателя с короткозамкнутым ротором и смонтированной с ним в одном блоке муфты сухого трения. Фрикционный диск муфты установлен на одном выходном валу со шкивом, который соединяется с маховиком швейной машины клиновым ремнём. Общий вид привода приведён на рисунке 12а.
Электропривод монтируется на крышке рабочего стола на резиновых амортизаторах. Такое крепление не передаёт вибрацию и удобно в том плане, что когда необходимо по каким-либо соображениям изменить высоту стола, например, по физиологическим данным оператора, то относительное положение привода и шьющей головки не меняется.
Отрегулированное один раз натяжение клинового ремня, связывающего привод и шьющую головку, остаётся при таких манипуляциях постоянным.
Мощность электропривода в различных модификациях от 200 до 400 Вт. Напряжение электрической сети 110, 220, 380 В.
Регулирование частоты вращения главного вала машины оператор осуществляет путём нажима на педаль. Ясно, что в этом случае нагрузка на работающего немаленькая; его внимание всё время напряжено: где снизить скорость, где остановиться и т.д.
Развитие электроники, микропроцессорной техники дало возможность создать технические средства для автоматизации процесса управления шитьём.
Были сконструированы приводы (рис. 12б), которые способны обеспечить:
Плавный пуск машины;
Останов машины при заданном положении иглы (вверху или внизу);
Обрезку ниток;
Подъём нажимной лапки;
Автоматизированную закрепку с возможностью запрограммировать выполнение закрепки в начале или конце строчки, или в том и другом случае, а также число стежков в закрепке;
Программирование числа стежков в строчке на отдельных её участках.
Рис. 12. Виды приводов:
а) фрикционный; б) автоматизированный; в) двигатели прямого привода
Автоматический останов иглы в верхнем положении необходим для чёткого срабатывания вводимого в машину механизма обрезки ниток, так как в противном случае обрезающий подвижный нож может задеть иглу, находящуюся в материале, а это приведёт к её поломке и повреждению лезвия. При остановке машины с иглой в нижнем положении и поднятой нажимной лапке сокращается время на поворот обрабатываемых деталей, когда строчка резко меняет своё направление.
Особенностью автоматизированного привода является наличие у него нескольких фиксированных частот вращения: 150–200 об/мин – для доводки главного вала головки до положения останова; 200 об/мин – для автоматического выполнения закрепки; и ещё несколько фиксируемых дополнительных режимов (до 11) для регулирования скорости основной работы.
Электропривод, обеспечивающий автоматизированное выполнение вспомогательных функций, состоит из электродвигателя, на валу которого закреплена электромагнитная муфта вращения; электромагнитной муфты торможения; подвижного фрикционного диска контрпривода; тахогенератора; клиноременной передачи; синхронизатора вращения; блока управления и педали управления. Крепится автоматизированный привод точно так же, как обычный фрикционный, болтами через резиновые прокладки.
Дальнейшее совершенствование привода коснулось прежде всего самих электродвигателей. Тиристорное управление позволило уменьшить (и весьма значительно) габариты двигателей, повысить приемистость привода, снизить вибрацию, обеспечить необходимую точность останова агрегата на заданном участке шва, исключить потери мощности, экономить электроэнергию.
Новые двигатели (рис. 12в) компактны и мощны. Выпускают такие двигатели фирмы «Efka» и «Quik-Rotan» (обе Германия) и «MitsubishiElectrik» (Япония). Каждая фирма предлагает двигатели двух типоразмеров: с мощностью 375 и 550 Вт.
Двигатели можно встраивать непосредственно в шьющие головки и использовать в качестве прямого привода (Directdrive) главного вала, но можно применять и в традиционной навесной системе, размещая двигатель под крышкой стола. При этом и в том и в другом случае двигатель может работать в ручном режиме шитья и при шитье с использованием программы. При разумной цене такой привод, наверняка, вытеснит привычный асинхронный двигатель с фрикционной муфтой включения.
Описанный привод хорошо комбинируется с микропроцессорными системами управления и теперь практически все функции швейной машины находятся под контролем, что даёт возможность программировать весь ход технологической операции: количество стежков на заданном участке строчки, скоростной режим на каждом из них, необходимое расстояние от края полуфабриката, нужный момент останова шитья при фиксации иглы в верхнем или нижнем положении, обрезку ниток.
В последнее время разработчикам машин пришлось решать (жизнь потребовала) весьма серьёзную задачу: обеспечение качества строчек и швов вне зависимости от свойств соединяемых материалов.
С этой целью рабочие органы и приводящие их в движение механизмы были подвергнуты тщательному компьютерному анализу на основе кинематических и динамических положений теории механизмов машин. В результате чего найдены оптимальные условия петлеобразования для различных типов швейных машин, удалось снизить натяжение ниток в процессах образования и затягивания стежков, решить вопросы стабильного транспортирования сложных в этом отношении синтетических материалов.
Одним из очень нагруженных элементов швейной машины является игла. Коснулся прогресс и этого элемента.
С увеличением скорости шитья игла существенно нагревается. Повышение температуры иглы приводит к плавлению синтетических волокон перерабатываемых материалов и прикипанию продуктов этого процесса к игле. Игла с прилипшими частицами материала с затруднением прокалывает пакет, нитка не скользит по желобкам иглы и в отверстии острия. Отсюда пропуски стежков и обрывы.
Новые иглы с титановым и керамическим покрытиями, а также с более совершенной микрогеометрией отвечают всем сегодняшним запросам швейников. Высококачественные иглы выпускают фирмы «Triumph» (Тайвань), «Schmetz» (Германия), «Organ» (Япония).
Челноки. Установка в корпус челнока вкладышей из полимерного материала позволяет обойтись без смазки челнока, что исключает возможность загрязнения любых обрабатываемых материалов. Не требуется в дальнейшем дополнительных усилий для удаления следов масла на одежде. То же решение ведёт к снижению трения в челночном комплекте, а это позволяет уменьшить натяжение ниток и улучшить условия петлеобразования, что в свою очередь уменьшает стягивание и посадку строчки.
Челноки с элементами из полимерных материалов меньше нагреваются даже при длительной работе на высоких скоростях, что положительно сказывается опять-таки на натяжении ниток и качестве строчки.
Подбор материалов, оптимальное соотношение конструктивных элементов дали возможность при высоких скоростных режимах использовать челноки увеличенных размеров, куда можно установить шпулю большей ёмкости. А отсюда – больше нитки на шпуле и реже перезаправка.
Важный вопрос – стабильное транспортирование полуфабриката под иглой.
Сегодня швейникам для переработки предлагается огромная номенклатура текстильных материалов. У них различные показатели жёсткости, растяжимости, поверхностного сцепления. Различные толщины.
Стандартный узел перемещения материала: нижняя рейка – лапка часто не удовлетворяет потребителя, так как не обеспечивает нужного качества строчки, даёт увеличенную посадку и стягивание.
Созданы более десятка различных конструкций устройств для продвижения ткани: с иглой, отклоняющейся вдоль линии строчки; дифференциальный двигатель; с верхней подающей рейкой и др. Все они улучшают и стабилизируют процесс подачи, так как компьютерное исследование и рекомендации на его основе привели к выбору оптимальных из применяемых механизмов.
Некоторые фирмы в своих машинах применяют механизм транспортирования, в котором производится изменение угла наклона транспортирующей рейки относительно направления перемещения полуфабриката.
В систему транспортирования вводится тянущий ролик (пуллер), который устанавливается непосредственно за нажимной лапкой. Пуллер имеет два шаговых привода – вращения и вертикального перемещения. Вращение ролика программируется согласно с установленной на машине длиной стежка и обязательно строго синхронизируется с работой зубчатой рейки двигателя ткани. Вертикальные перемещения ролика обеспечивают управляемое давление его на транспортируемый материал. Ролик можно поднимать и фиксировать без контакта с материалом для перехода через поперечные швы, для поворота материала вокруг иглы.
Стабильность транспортировки полуфабриката обеспечивается и с помощью системы, управляющей давлением нажимной лапки на материал в зависимости от скорости работы машины. Исключается эффект зависания лапки над материалом на больших скоростях, а качественная строчка может быть получена при любой скорости работы машины (система «SRP» фирмы «Pfaff»).
Решая задачу качественной транспортировки полуфабриката под иглой, фирма «Juki» в некоторых из своих машин (LU-1508NH, LU-1509NH) применила новый механизм, обеспечивающий движение рейки двигателя ткани не по традиционной эллипсовидной кривой, а по почти идеальной для рабочего процесса траектории в виде прямоугольника (см. рис. 4.8а). Рейка механизма двигателя ткани поднимается вертикально вверх из своего нижнего нерабочего положения и выходит на контакт с полуфабрикатом над игольной пластиной. Затем она движется вперёд по направлению подачи, причём плоскость вершин зубьев остаётся параллельной плоскости игольной пластины. Закончив перемещение, рейка опускается вертикально вниз, а затем под игольной пластиной возвращается в своё первоначальное положение. Конечно, механизм более сложен, но даёт чёткое продвижение.
Особенностью многих машин стал дифференциальный двигатель ткани, что позволяет на труднотранспортируемых тканях получать ровные швы без искривления и волн или соединять «в стык» различные по плотности материалы, также обеспечивая ровноту строчки. Конструкторы добились, что подобные механизмы стали вписываться даже в машины, которые имеют узкую рукавную платформу (машины серии 35800 совместной разработки «Juki» и «UnionSpecial»).
Другие механизмы также подверглись совершенствованию, например, механизмы обрезки ниток. Современные механизмы обеспечивают длину обрезанных концов ниток до толщины игольной пластины. Это стало возможным в связи с тем, что механизм выдвигается в рабочую зону только в момент обрезки. Игольная нитка хорошо удерживается в игле и не выскакивает при последующем цикле работы.
Все машины стали снабжаться панелью управления с большим дисплеем, где даётся информация, легко понимаемая и программируемая по символам, отображающая процесс шитья в режиме реального времени. Технологические инструкции всё время высвечены, и проблемы при шитье определяются в момент их возникновения.
Можно привести ещё несколько примеров технического совершенствования оборудования:
У плоскошовных машин часто используется верхний двигатель ткани и специальная плавающая нажимная лапка;
У плоскошовных машин – учащённая строчка в конце её выполнения (используется как закрепка);
При соединении трикотажных полотен применяется устройство для расправления скрученных срезов;
Система активного контроля натяжения ниток в процессе петлеобразования;
При окантовке срезов обрезка краёв тканей производится непосредственно перед окантовкой;
При краеобмётке в конце строчки производится заделка цепочки ниток в шов;
В конструкцию машины вводятся пневматические устройства для заправки ниток;
В пуговичных машинах цепного стежка в конце цикла завязывается узелок, что делает строчку нераспускаемой;
Во многих машинах выдаётся информация для работающего об оставшейся на шпульке нитке;
Производится регулирование усилия прорубания материала в петельных полуавтоматах;
Петли различной длины делаются без смены прорубающего ножа (нож срабатывает несколько раз по длине участка).
Всё перечисленное серьёзно способствует улучшению качества выполняемых швейных операций.
4. Швейные машины для выполнения операций группы I б
На базе описанных выше технических решений проектировщики разработали и фирмы серийно выпускают оборудование с широкими технологическими возможностями, в частности для выполнения строчек с закрепками. Комбинация автоматизированного привода и машин, конструкция которых описана в разделе 2, позволяет осуществлять в нужный момент останов, подъём лапки и обрезку ниток. Область применения в этом случае существенно больше, практически полностью охватываются операции, составляющие I и II группы по нашей классификации.
На рисунке 13 приведён для сравнения вид нескольких типов автоматизированных машин: одноигольной и двухигольной челночной, челночной зигзаг-машины, одноигольной машины с цилиндрической платформой, двухигольной машины с колонковой платформой, машины с большим вылетом рукава, краеобмёточной, плоскошовной.
Рис. 13. Швейные машины с автоматическим приводом
Создаются и новые конструкции, вбирающие в себя весь комплекс последних исследовательских достижений. В качестве примера приведём последнюю серию машин фирмы «Juki» DDL-9000. Общий вид показан на рисунке 14.
Прежде всего это новый дизайн, отличный от всех прошлых. Удлинённый рукав: от колонки до оси иглы 300 мм, вместо 260 у более ранних конструкций.
Трубчатая часть рукава имеет скос спереди вниз, открывая широкий обзор на рабочую зону платформы.
Самая низкая часть рукава (район нижней втулки игловодителя) на 10 мм выше, чем у машин аналогичного назначения прежних серий и чем у машин аналогов других фирм. Оператору гораздо удобнее перемещать полуфабрикат в такой длиннорукавной швейной головке. Размеры платформы 517 178 мм.
Рис. 14. Последняя разработка фирмы «Juki» (2008 г.)
Несмотря на увеличенные размеры рукава, вибрация корпуса и шум работы механизмов сохранились на прежнем низком уровне. Произошло это в связи с хорошей балансировкой всех подвижных элементов машины. А потому рабочий режим машины 3500÷5000 оборотов в минуту в зависимости от характеристик обрабатываемого материала.
Этот режим работы обеспечивает прямой привод на базе компактного сервомотора типа АС, смонтированного непосредственно в головке. Система обеспечивает отличную приемистость при жёстком старт-стопном режиме: плавный и быстрый набор скорости, чёткий останов при малом выбеге.
В приводе не используется ни клиновый ремень, ни какой бы то ни было другой ремень, и потому продукты износа передачи не могут попасть в механизмы машины.
Далее. Шьющая головка сконструирована в двух вариантах. D-тип – сухой вариант, S-тип – с минимальной смазкой. В сухом варианте нет необходимости следить за уровнем масла в картере машины, доливать масло при расходе и заменять его после достижения определённого срока службы, следить за возможностью подтекания и устранять выявившиеся недостатки. А главное это то, что при отсутствии масла в системе никогда не будет загрязнено изделие, которое шьётся, продуктами износа.
В варианте S (полусухом) имеется небольшая ёмкость для масла, откуда оно дозированно, в необходимых количествах, подаётся для смазки игловодителя и челночного устройства. Это полностью герметичная система, не допускающая утечек масла. Качество, необходимое при высокой скорости работы машины.
В условном обозначении машин серии DDL-9000 буквы D и S, следующие за цифрами, указывают на использованную систему смазки.
Машины новой серии могут применяться для шитья лёгких и средних материалов (условное обозначение S), для шитья тяжёлых материалов (H) и для шитья очень лёгких материалов (F).
Натяжение ниток в машине невелико и легко регулируется. Давление лапки на материал осуществляется пружиной с усилием всего в 500 г, но лёгкая лапка не прыгает, предотвращая проскальзывание материала, образование складок и неравномерную подачу.
Длина стежка – до 5 мм, в очень лёгком варианте до 4 мм. Подъём нажимной лапки – 5,5 мм рукой, коленом 15 мм. Применяемые иглы от № 65 до № 160. Общий вес машины 84,5 кг.
Система управления машиной включает в себя: управляющий блок и контрольную панель для визуального наблюдения. Система обеспечивает выполнение в автоматическом режиме таких функций, как останов шитья с иглой вверху или внизу, обрезку ниток, выполнение закрепок, выполнение строчки по заданному числу стежков и др.
Обязательным элементом машины является «выключатель безопасности». Контакты этого выключателя последовательно включены в цепь электроснабжения машины. При замкнутых контактах машина готова к работе, а такое положение возможно только в том случае, если шьющая головка чётко установлена в вырезе крышки стола. Когда головка откинута, например, чистка, осмотр или для профилактических и ремонтных работ, контакты выключателя разомкнутся, и любой, даже случайный, пуск машины невозможен.
Устройство для намотки ниток на шпулю встроено в рукав. Удобно.
По отдельному заказу машина может быть снабжена ещё рядом дополнительных устройств, например, указателем остатка нитки на шпуле, датчиком, реагирующим на край сшиваемого материала, кнопкой включения обратной подачи (а не рычагом) и др.
Основной вариант исполнения машины – одноигольная с нижней подающей рейкой. Однако на этой базе появились и другие модификации, например, беспосадочная машина, осуществляющая продвижение заготовки нижней зубчатой рейкой и отклоняющейся вдоль строчки иглой (вариант DDL-9010).
«Juki» позиционирует машину DDL-9000 как «лидера XXI века». На наш взгляд, другие фирмы («Pfaff», «Durkopp») совсем не уступают.
5. Оборудование для выполнения операций типа I и II в автоматическом режиме
В системе машин, которые применяются в процессах ниточной сборки предметов одежды из деталей кроя, особое место занимают швейные полуавтоматы. Этот вид оборудования характеризуется тем, что рабочий процесс (выполнение стежка) и рабочие перемещения (выполнение строчки) осуществляется автоматически, а установка заготовок и их съём – вручную или с осуществлением отдельных средств механизации.
Использование полуавтоматов позволяет получать строчку высокого качества независимо от её кривизны, переломов, возвратов и квалификации работающего, то есть без всяких отклонений от заданного модельером контура (точность). При этом, что первая строчка, что сотая будут одинаковыми (стабильность). Влияние рабочего на выполнение операции сводится к минимуму, практически нужна только аккуратная установка заготовок на рабочую позицию. Производительность труда возрастает в несколько раз по сравнению с трудом на машине неавтоматического действия.
Однако все эти технические преимущества перекрываются одним недостатком – высокой ценой этого оборудования. Правда, использование полуавтоматов в массовом производстве позволяет влияние указанного фактора существенно уменьшить.
Сегодня, когда рынок, мода диктует быструю смену моделей, большие партии швейных изделий редки, а потому практическое применение машин полуавтоматического действия невелико. Казалось, вопрос решён. И решён не в пользу полуавтоматов. Однако ряд фирм продолжают конструкторский поиск, и что он не безуспешен, показала очередная выставка IMB. Пути, по которому идут эти фирмы, следующие.
Во-первых , выделение типовых узлов в одежде, где может быть экономически выгодно использована такая техника. Это позволяет применить полуавтомат при выпуске однородных изделий, а общую их партию увеличить.
Во-вторых , решается проблема быстрой переналадки полуавтомата на иной контур, на иную форму, на другой пакет, иную схему распределения слоев в пакете. Расширяются возможности, увеличивается количество обрабатываемых моделей, появляется гибкость.
В-третьих , переход на новую элементную базу в системах управления позволяет упростить всю конструкцию и несколько снизить стоимость машины.
В-четвёртых , ясно просматривается подход решать вопрос комплексно, то есть создавать группу полуавтоматов для автоматизации выполнения сборочных операций для какого-либо конкретного изделия.
В-пятых , уделяется большое внимание надёжности функционирования техники, например, введение элементов, следящих за окончанием нитки на шпуле или отключающих прорезные ножи, в случае какого-либо сбоя, чтобы не испортить заготовки.
Напомним, что операции, отнесённые нами к I и II группам, это процессы, связанные с прямыми и слабоискривлёнными строчками. Посмотрим, что предлагается для их автоматизации.
Представителем такой техники является полуавтомат для выполнения вытачек. Вытачки как элементы одежды необходимы для создания необходимого объёма формы одежды в области груди, по линии талии, по спине. По конструкции эти вытачки бывают неразрезные и разрезные. В числовом выражении вытачка определяется двумя параметрами: длиной и глубиной. Но, главное, характеризуется строчкой: прямая или слабоискривлённая, выходящая в начале и конце на край полуфабриката. Строчка может быть как челночной, так и цепной, естественно, двухниточной.
Для первого случая это может быть класс 3586-2/02 «Pfaff» (рис. 15а), для второго – 743-221 «Durkopр/Adler» (рис. 15б).
Заготовки (полочки пиджака или половинки брюк) размещаются в зоне загрузки на шаблоне с огибанием его края. Точное позиционирование осуществляется по лазерным световым отметкам. После такого базирования полуфабрикат с помощью подающего стола направляется в рабочую зону шьющей головки, где вытачка стачивается с одновременным его разрезанием. Последний элемент операции может и не выполняться (неразрезная вытачка на брюках).
Подача заготовок и само стачивание происходят с перекрытием во времени, благодаря чему вырастает производительность.
Строчка в начале и конце закрепляется путём учащения стежков, после окончания цикла нитки обрезаются, а заготовка укладывается в пачку.
Длина стежка варьируется от 0,5 до 3,0 мм.
На этом же полуавтомате можно выполнять и другие операции подобного типа: стачивание частей подворотников, стачивание подбортов, застрачивание складок. Но опять повторим: экономика применения должна быть тщательно продумана и просчитана.
В одежде (любой – мужской, женской, детской) всегда имеются карманы. Они имеют утилитарное и декоративное назначение, а потому качество их исполнения – на виду.
Аккуратный прорезной в рамку, с клапаном, с листочкой, накладной – могут украсить одежду, а искривлённые, небрежно обработанные – свести на нет все предыдущие усилия в изготовлении.
Рис. 15. Полуавтоматы для изготовления вытачек
Ясно, что конструкторская мысль давно была направлена на создание техники, обеспечивающей качественную обработку карманов независимо от квалификации работающего, тем более, что обработка карманов, как накладных, так и прорезных весьма трудоёмка.
При изготовлении прорезных карманов в рамку необходимо проложить две параллельные строчки с закреплением их в начале и в конце и разрезать полуфабрикат между строчками. При этом нужно иметь в виду, что обе строчки находятся в середине детали, где будет находиться карман. На край заготовки они не выходят, а это предъявляет особые требования к механизмам, их выполняющим.
Многие фирмы преодолели эти трудности и создали производительные и надёжные полуавтоматы: «Juki» – серия APW 194 N; «Durkopp/Adler» – 745 кл в нескольких модификациях; «Global» – серия PW 2045; «New-tech» – серия 2000; «AMF-Reece» – модель LW – 6000 (в различных вариантах); «A-S-S» – серия BASS 3500 и др.
Технология изготовления прорезных карманов в рамку, заложенная в основу действия полуавтомата, отличается от таковой же, но при ручной работе.
Проиллюстрируем её схемой (рис. 16).
Рис. 16 Технологическая схема изготовления прорезного кармана
На сборку (изготовление рамки кармана) поступают три детали: основная (это может быть полочка пиджака, половинка брюк и т.д.), долевик и обтачка. Последняя по ширине выглядит как две обтачки при ручном исполнении. На платформу 1 полуавтомата (рис. 16а) укладывается долевик, а поверх его основная деталь лицом вверх. Укладка производится по упорам, которые установлены на платформе, и световым отметкам, оставляемым лазерными излучателями. Отметки эти выглядят как прямые линии и перекрестья. Зажимами 2 долевик и основная деталь фиксируются на платформе. Если укладка произведена с отклонениями (на взгляд оператора), то её можно повторить, исправив неудачное размещение. Для лучшей ориентации в процессе укладки на основную деталь (полочку, половинку брюк) наносятся меловые линии, отмечающие место расположения кармана. На шаблоны 3 укладывается обтачка лицом вниз. Пуансон 4 опускается сверху на обтачку, проминает её между шаблонами 3 и прижимает к уложенным на платформе основной детали и долевику (рис. 16б). Шаблоны 3 сдвигаются и окончательно формируют обтачку, которая теперь выглядит в виде перевёрнутой буквы «Т» (рис. 16в). В таком виде весь пакет поступает в зону шитья, где прокладываются одновременно две параллельные строчки, состоящие из двухниточных челночных стежков. Одновременно со стачиванием происходит разрезание входа в карман, для чего предусмотрен нож, располагающийся между иглами. Для выполнения этого рабочего процесса в платформе 1, шаблоне 3 и пуансоне 4 имеются пазы.
На схеме для упрощения они не показаны. Нож разрезает обтачку, основную ткань и долевик, причём он включается в работу, когда будет образовано 8 ÷ 10 мм строчек от начала шитья, а отключается, не доходя те же 8 ÷ 10 мм до окончания строчек. В начале и конце строчек производится закрепка. Сшитый пакет выглядит, как показано на рисунке 16г. После окончания шитья разрезание пакета завершается надсечкой уголков в концах разреза для удобства вывёртывания. Ножи, высекающие уголки, совмещены с узлом, обеспечивающим вывёртывание. При обратном холостом ходе ножей этот механизм проводит обтачку через разрез входа в карман вниз на изнаночную сторону основной детали, и рамка кармана теперь выглядит так, как показано на рисунке 16д.
Рабочий цикл изготовления рамки прорезного кармана заканчивается удалением из рабочей зоны основной детали с помощью укладчика. Остаётся только окончательно расправить рамку, приутюжить и закрепить её в концах. Но это уже другое оборудование. Общий вид одной из моделей полуавтомата для изготовления прорезных карманов приведён на рисун- ке 17.
В дальнейшем технологическим процессом предусматривается прикрепление подкладки кармана к краям обтачки и соединение её боковых срезов. Таким образом, изготовление кармана завершается.
Подобным образом изготавливаются и карманы с клапаном. Готовый клапан укладывается поверх сформированной обтачки лицевой частью вниз. Присоединяется клапан к карману одной из тех же строчек одновременно с изготовлением рамки.
Производительность труда увеличивается более чем в три раза по сравнению с этим же показателем при ручной технологии и использованием универсальных машин. Это достигается за счёт совмещения во времени вспомогательных приёмов с машинным циклом работы полуавтомата.
На рассматриваемом оборудовании в автоматическом режиме выполняется соединение двумя параллельными строчками цельнокроеной обтачки, долевика, клапана и полочки, разрезается вход в карман, надсекаются уголки, обеспечивается останов с иглами в заданном положении, обрезка ниток, выведение изделия из зоны обработки и укладывание его в пачку.
На полуавтомате можно выполнить: прямую рамку кармана без клапана, прямую рамку кармана с клапаном, наклонную рамку с клапаном и без него, карман с листочкой.
В случае изготовления наклонных карманов строчки соединения сдвинуты относительно друг друга, в связи с чем необходимо обеспечить разновременное включение в работу шьющих механизмов. С этой целью в полуавтомате применяется швейная головка с отключающимися игловодителями.
Рис. 17. Полуавтомат для изготовления прорезного кармана
Стандартные расстояния между иглами 8, 10, 12, 14, 16, 18 и 20 мм. Длина стежка 2,0÷3,4 мм. Скоростной режим 2500 оборотов в минуту.
В полуавтоматах имеется устройство, следящее за наличием нитки в шпульке. Челнок увеличенный.
На этом оборудовании можно изготавливать рамки длиной от 35 до 180 мм. Самые малые длины – это не для карманов, это, скорее, прорезные петли на женской одежде. Но и такие часто встречаются.
Отметим ещё один важный момент. При изготовлении прорезных карманов с клапаном необходимо чёткое соответствие по длине клапана и рамки. Такое положение можно достичь только в случае обтачивания клапанов на машинах полуавтоматического действия, обеспечивающих стабильность размеров при обработке. Об этом мы ещё раз напомним в разделе
Создатели швейного оборудования успешно автоматизировали ещё ряд операций. В настоящее время полуавтоматами оснащаются целые потоки.
Для примера рассмотрим технологический процесс изготовления мужских брюк. Из 51 операции по сборке 18 выполняется не на швейных машинах (утюжильные места, пресса). Ясно, что оставшиеся 33 операции все сразу невозможно автоматизировать сегодня. Однако добрую половину удалось перевести на полуавтоматы, что убедительно показали фирмы «Beisler» и «Durkopp/Adler» (Германия).
Здесь можно выделить типовые операции, например, обмётывание срезов заготовок, обтачивание клапана кармана, изготовление самих карманов, обработка гульфика и откоска, подшив низа брюк. Для перечисленных операций предлагается большая группа швейных полуавтоматов (табл. 6).
Как видим, процент автоматизации рассмотренного технологического процесса весьма высок. Многие из этих полуавтоматов были показаны ещё на выставке IMB-200 Все они воплотили в себе последние достижения технической мысли. Сегодня они уже широко в производстве.
Точная транспортировка полуфабриката, без сбоев и заминов, даже таких, какие называют «труднотранспортируемыми». В нужных местах – необходимая посадка, любого слоя в пакете как верхнего, так и нижнего. Фотослежение: обрезка подаваемой тесьмы в точный размер и без отходов. Механизм обрезки ниток обеспечивает короткие концы. С помощью простых регулировок осуществляется переход с размера на размер и изменение параметров операции. Контролируется остаток нити в шпуле (в случае использования системы челночного переплетения).
Все полуавтоматы снабжены цветным графическим дисплеем. В случае любого сбоя отключаются устройства, способные испортить материал.
Таблица 6
Полуавтоматы, применяемые при изготовлении брюк
Похожий комплекс предлагает фирма «A-S-S» («AutomatedSewingSystems») также из Германии. Специализирующаяся на оборудовании для изготовления джинс итальянская фирма «VI.BE.MAC» в комплект включает 8 полуавтоматов: для подгибки и закрепления верхнего среза карманов, для настрачивания этикетки, для прокладывания декоративной строчки по карманам, для настрачивания шлёвок, для выполнения отделочной строчки по гульфику, для изготовления петли и для закрепок.
Предлагаются комплекты полуавтоматов и для других изделий массового производства – пиджаков, сорочек. Вот в сорочке на полуавтоматах заготавливают все узлы: манжеты, воротник, клапаны, карманы, планки на переде, настрачивают карманы и клапаны, пробивают и обмётывают петли на планке, пришивают пуговицы, изготавливают рукавную планку. Что же остаётся? Остаётся соединить плечевые, рукавные и боковые срезы, втачать воротник, присоединить манжеты и подшить низ изделия. Пока эти операции идут с ручным сопровождением полуфабриката. Таких операций очень немного.
Необходимо заметить, что не все перечисленные выше полуавтоматы обеспечивают выполнение операций I и II групп. Есть и другие, для III и IV. О них будет рассказано в соответствующих главах.
6. Оборудование для выполнения операций, относящихся к III группе
Операции, относящиеся к этой группе, выполняются строчками сложной формы, контур имеет множество точек излома, подача относительно рабочих органов шьющей головки осуществляется в произвольном направлении. По размерам эти строчки весьма различны, но всё-таки их можно подразделить на малые, размещающиеся в поле, примерно, 2060 мм; средней величины, укладывающиеся в прямоугольник 60100 мм, и большие. В последнем случае необходимо вести обработку площади в габарите 400 мм по ширине и до 250 мм по второй координате.
Всё оборудование для этой группы операций относится к машинам полуавтоматического действия: рабочий процесс осуществляется автоматически, а установка заготовок и их съём – вручную.
В связи с приведённой выше градацией строчек по размерам рассматриваемая техника программируется на различное число стежков. Большинство полуавтоматов, предназначенных для выполнения закрепок, пришивания пуговиц, крючков, этикеток, талонов, вымётывания коротких петель, производят небольшое число стежков, от 8 до 100. Петли увеличенной длины, сложные закрепки, некоторые рисунки требуют большого числа стежков, и ряд моделей полуавтоматов их выполняют до 400. Рисунки, сложные строчки большой протяжённости с повторами, возвратами задаются более ёмкой программой с памятью на 20 000 стежков.
Представителями короткошовных полуавтоматов первой группы являются машины серии МВ-372 и 373 «Juki», В 916 «Brother», серии BS 470 «Global» (рис. 18).
Машина работает на скорости 1500 оборотов в минуту. С её помощью можно пришивать пуговицы диаметром от 10 до 28 мм (есть модификации от 8 до 30) с двумя и четырьмя отверстиями. Это основной вариант. Но возможности машины шире. Так, при сравнительно простой переналадке машины применяются для прикрепления пуговиц с ушком, пуговиц с обвитой ножкой, пуговиц с подпуговицами, кнопок, этикеток.
Число стежков в цикле определяется классом и подклассом машины и может быть 8, 16, 32 или 6, 12, 24. Управление циклом осуществляется с помощью копиров. Размеры стежков регулируются диапазоне 2,5÷6,5 мм как вдоль рукава машины, так и поперёк.
Пуговица для пришивки вставляется в зажим вручную. Зажим поднимается над платформой на 14 мм, что позволяет легко расположить под ним деталь одежды или часть изделия, на которые пришивается пуговица.
Останов машины в конце цикла происходит на пониженной скорости, что исключает удары и вибрации в момент окончания шитья. Зажим поднимается автоматически.
Машины снабжены устройством для обрезки нитки. Конструкции этого узла различны. Так, в группе машин нитка обрезается пластинкой, связанной рычажной системой с механизмом подъёма зажима, и, скорее, обрывается, чем обрезается. В части машин другая система – она состоит из пары ножей (подвижного и неподвижного), которые срабатывают под игольной пластиной. Длина кончика нитки не более 3,5 мм.
Смазка машины по точкам при помощи маслёнки. Вес головки 20 кг, общий вес машины 80 кг. Машина приводится в работу от электродвигателя мощностью 200 Вт; двигатель может быть однофазный и трёхфазный.
Дальнейшее техническое развитие машины получили в нескольких направлениях.
Рис. 18. Полуавтомат для пришивки пуговиц
Поскольку для прикрепления пуговиц здесь используется однониточный цепной стежок, то строчка, состоящая из таких стежков, подвержена распусканию, несмотря на то, что последние стежки в цикле выполняются в одну точку. Для предотвращения этого нежелательного явления был создан механизм для завязывания узелка из нитки в конце цикла. Реализовано это в машине серии МВ-377.
Машина в основном повторяет базовый вариант, но, заканчивая пришивку, выполняет прочный узел, препятствующий распусканию готового шва. Даже если последний стежок не завершён, то вероятность распускания практически невелика и риск потери пуговицы снижен.
Машина может снабжаться ещё и дополнительным бункером, обеспечивающим комплексную подачу пуговиц. Класс машины МВ 377 А/ВR у «Juki» или ВАS-016B у фирмы «Brother» (рис. 19).
На машине можно установить три различных режима работы: работа с ручной подачей пуговиц, когда оператор устанавливает пуговицы непосредственно в зажим; работа с автоматической подачей пуговиц из бункера; и режим загрузки пуговиц на одно изделие – 5÷6 пуговиц заправляются в пуговицеприёмник перед началом работы, а затем этот запас постепенно используется.
Оптимальный скоростной режим – 1300 оборотов в минуту.
Принцип «сухой головки» коснулся и короткошовных полуавтоматов. В них также применён привод на шаговых двигателях и компьютерное управление. Благодаря автоматизированному приводу упростилась механика машин, улучшилась динамика работы, снизились ударные нагрузки, уменьшились шум и вибрация.
Последние достижения фирмы «Juki» в области машин для пришивания пуговиц сконцентрировались в полуавтомате АМВ-289. Машина предназначена для широкой номенклатуры пуговиц: с двумя отверстиями, с четырьмя отверстиями, с ушком.
Рис. 19. Полуавтомат для пришивки пуговиц с подачей их из бункера
Пришить можно пуговицу с подпуговицей, можно на ножке с обвивкой. Качество прикрепления очень высокое: на изнаночную сторону проходит минимальное количество стежков, ножка выглядит в виде буквы «V», что позволяет провести обвивку большой плотности в начале ножки, а это предотвращает раскачивание пуговицы.
Компьютерная система управления позволяет легко вводить необходимые данные по программе пришивки различных пуговиц. Для защиты от распускания строчки, которая выполняется цепным стежком, на заключительном этапе цикла завязывается узелок. Узелок завязывается и при обвивке ножки. Область применения машин очень широкая.
Несколько лет тому назад в промышленности применялись пуговичные машины на базе челночного стежка. Конечно, строчка прочнее, но машина сложнее. С решением вопроса закрепления цепной строчки путём завязывания узелка необходимость в машинах челночных отпала. Сейчас они в номенклатуре заводов отсутствуют.
Двухниточная челночная строчка применяется в сложных коротких швах закрепочного типа. Такие строчки имеют длину 7÷16 мм и ширину 1,8÷2,5 мм. Форма закрепки и число стежков в ней программируются копиром, являющимся в машине сменным элементом (серия LK-1850 «Juki», «Global»). Скоростной режим – 2300 оборотов в минуту, при использовании синтетических ниток снижается до 1800 оборотов в минуту. Челнок колеблющегося типа. Зажим поднимается над платформой максимально до 17 мм. Закрепки делаются за 42 стежка или за 21 стежок и образуются за счёт перемещения под иглой материала в продольном и поперечном направлениях. Машина широко применяется на швейных предприятиях, однако в настоящее время устойчивая тенденция к её замене на оборудование серии ВТ-1900 или LK-1900 (рис. 20), где строчка образуется с помощью шаговых двигателей и компьютерного управления. Это дало существенное многообразие форм закрепки: стандартное число 50, но может быть увеличено до 200.
Машина выпускается для различных видов тканей. Номинальный скоростной режим 3000 оборотов в минуту, но для тяжёлых тканей и толстых пакетов скорость должна быть снижена до 2700 оборотов в минуту.
Поле, в котором располагается строчка, 3040 мм. Важной особенностью является введение в конструкцию электронного устройства, активно следящего за натяжением игольной нитки, что очень важно при выполнении закрепки на пакетах, где толщина по длине закрепки меняется.
Отдельные варианты машины могут иметь увеличенный челнок – больше шпуля, больше нитки на шпуле, реже перезаправка.
Ещё одна группа коротких строчек – всевозможные петли на швейных изделиях. Для петель на белье и одежде из лёгких материалов петельная строчка выполняется челночным или однониточным цепным стежком; петли на верхних изделиях, где используются более плотные ткани, относящиеся к пальтовой и костюмной группам, – двухниточным цепным. Здесь часто для создания рельефной петли внутрь обмётки срезов прокладывается утолщённая нитка, называемая каркасной. Без такой нитки петли получаются рыхлыми, невыразительными.
Исходя из вида изделия, модели, фактуры материала одежды, области эксплуатации, петли выполняют различной формы, различной длины, с разной шириной кромок, с разным типом закрепления.
Но в общем виде процесс вымётывания петли следующий: зигзагообразное расположение обмёточных стежков достигается сочетанием продольного перемещения материала (вдоль петли) и поперечным к нему отклонением иглы. Основные виды петель (наиболее часто применяемые) приведены на рисунке 21.
Для изготовления прямых петель созданы различные конструкции машин: с механическим управлением (LBF-780 «Juki», HM-8180 «Brother», BH-783 «Global», 3117 «Pfaff» и др.) и электронным управлением на базе шаговых приводов в системе Directdrive (3119 «Pfaff», LBH-1790 «Juki», HE-8000 «Brother» и др. (рис. 22).
Машины с механическим управлением работают на скорости 3600 оборотов в минуту, выполняют петли одного вида длиною от 6,4 до 38,1 мм, кромки которых могут быть обмётаны с числом стежков 54÷345. Изменение числа стежков производится за счёт смены блока шестерён в системе подачи. Высота подъёма зажима ткани до 12 мм. Стежок двухниточный челночный. Есть варианты для изготовления петли с каркасной ниткой. Смазка машины автоматическая. Вес машины 80 кг.
Рис. 20. Закрепочный полуавтомат
Вход в петлю прорубается плоским ножом, который при рабочем движении взаимодействует с острыми кромками узкого паза, выполненного в игольной пластине.
Рис. 21. Наиболее часто встречающиеся виды петель
После окончания цикла выметки при подъёме зажима, удерживающего полуфабрикат, приводится в действие устройство для обрезки верхней и нижней нитки около ткани. Одновременно конец верхней нитки защемляется между верхним ножом и плоской пружиной, что позволяет надёжно начинать следующий цикл обмётки – нитка из ушка иглы не выскочит.
Важным элементом машины является узел блокировки работы ножа, прорубающего ткань, в случае каких-либо неполадок с шитьём.
Машины с электронным управлением имеют большие технологические возможности.
Скоростной режим – до 4200 оборотов в минуту. Размеры петель в стандартной комплектации такие же, как у машин предыдущей серии, но по специальному заказу сменных деталей длина петли может быть увеличена до 41, 70 или даже до 120 мм. Но главное – это простой переход на изготовление петли иной формы, а вариантов при этом может быть до 30. В памяти машины может храниться 99 моделей петель.
Электронное слежение за натяжением нити позволяет получить хорошее качество петли, даже если она пробивается на пакетах неравномерной толщины.
Важной особенностью машины является тот момент, что она не требует замены прорезного ножа при изменении размера петли. Механизм ножа здесь таков, что он срабатывает два-три раза при увеличении длины петли, смещаясь вдоль неё при работе.
И повторим, главное – это простой и быстрый переход на изготовление другого вида петель.
Стоит обратить внимание на конструкцию рукава машины. Он (рукав) в основании выполнен со смещением от продольной оси платформы, что открывает свободный проход ткани по всей длине платформы машины. Это важно в тех случаях, когда петли вымётываются вдоль какой-либо детали, например, на планке мужской строчки. Полочка свободно располагается на столе и платформе машины и не затрудняет рабочий процесс.
Петля «с глазком» на верхней одежде служит не только смысловым узлом, удерживающим пуговицу, но и украшающим элементом, существенно влияющим на внешний вид. Хорошая петля сама по себе не испортит качественное изделие, но плохая, безусловно, повлияет на общее впечатление даже от добротной одежды.
У высококачественной петли стежки должны быть равномерными, бисерный стежок (двойной цепной стежок с характерными узелками в переплетении) должен чётко формироваться поверх каркасной нитки, глазок должен быть симметричным относительно оси петли, петля должна иметь пропорциональную и надёжную закрепку.
Сразу скажем, что закрепки здесь бывают трёх видов: поперечная, клиновая и полукруглая. Поперечная закрепка применяется в мужской одежде – пиджаки, пальто, куртки. Клиновая (или сходящаяся), как правило, в женской одежде и на джинсах. Полукруглая используется, в основном, на петлях брюк.
Рис. 22. Петельные полуавтоматы:
а) с механической системой управления; б) с электронной системой управления
Если машина выполняет петлю без закрепки, то поперечную закрепку приходится осуществлять отдельной операцией, применяя одну из закрепочных машин, о которых рассказывалось выше. Но из последних конструкций большим вниманием пользуются варианты, где поперечная закрепка включается в цикл изготовления петли, а вся операция осуществляется за один установ полуфабриката. При этом требуется, чтобы закрепка располагалась симметрично относительно петли, а размер её не превышал суммарной ширины обмётки кромок.
До 2000 г. фирмы в основном выпускали машины для изготовления петли с глазком механического типа. Геометрия и размер петли у них задаётся с помощью сменных жёстких копиров и системы рычагов. В настоящее время их сменили более совершенные, производительные и удобные машины с электронным управлением (рис. 23). Преуспели здесь фирмы «Juki», «AMFReece».
В машинах этого типа используются шаговые двигатели для продольного и поперечного перемещений, а также для привода в действие ножа для прорубки и разворота каретки с игольным механизмом.
Основным преимуществом таких машин перед механическими является простота перехода на другой вид петли. Переналадка осуществляется перепрограммированием основных параметров петли – длина, форма глазка, частота стежков, тип закрепки и её размеры – с помощью управляющей панели и блока памяти.
Рис. 23. Петельный полуавтомат для выполнения петли
двойным цепным стежком
Есть ещё один важный нюанс: при изменении длины петли или формы глазка требуется ещё заменить комплект: прорубающий нож – опорная колодка.
Ведь прорубка отверстия в петле здесь производится не плоским, а фигурным (по форме петли) ножом, взаимодействующим с плоской колодкой, в результате чего выштамповывается в ткани отверстие нужного размера и формы. Чтобы острые кромки стального ножа меньше тупились, колодка изготавливается из более мягкого материала, чем сталь, бронза, латунь. У рассматриваемых машин применяется раздельная прорубка глазков и прямых участков. Это позволяет выполнять петли различной длины без замены колодочек и ножей, просто прямой нож срабатывает несколько раз по длине. Всё обходится без дополнительных регулировок.
Машина оборудована механизмом, обеспечивающим активное следящее натяжение игольной нитки и нитки петлителя. Величина натяжения задаётся на операционной панели в зависимости от условий шитья. Параметры регистрируются на дисплее пошагово для того, чтобы можно было воспроизвести одинаковые условия работы. Натяжение ниток может устанавливаться отдельно для глазковой и прямой части петли.
Контроль за действием ножа осуществляется с помощью шагового привода. Это позволяет легко программировать давление ножа для разных видов ткани. Можно выбрать два режима прорубки: до обмётывания петли или после процесса шитья.
Правый и левые зажимы полуфабриката контролируются отдельно и приводятся в действие независимыми друг от друга воздушными цилиндрами. Этот механизм зажимает надёжно пакет различной толщины, предотвращая провисание.
Максимальная скорость шитья – 2200 оборотов в минуту; длина петли 10÷38 мм (возможно до 50); ширина обмётки кромок 2,0÷3,2 мм; длина закрепки 0 мм; 3÷15 мм; высота подъёма рабочих зажимов до 16 мм. Общий вес машины 185 кг.
На машине удобно выполнять петли, расположенные как поперёк, так и вдоль борта одежды.
Петли могут обмётываться и однониточным цепным стежком. Они применяются чаще всего на белье. Пример машины для реализации этого процесса МВН-180 «Juki».
Машина обладает довольно высокой скоростью работы (3300 оборотов в минуту), не требуя замены шпульной нитки. Петля, выполненная цепной строчкой, получается прочной, выдерживает большое количество застёгиваний и растёгиваний. С нижней стороны кромок петли происходит переплетение нитки в стежках в виде узелков, что придаёт петле красивый вид. С верхней стороны петля имеет гладьевую строчку.
Длина петли от 6,4 до 34,9 мм (при сменных деталях до 38,1 мм); ширина обмётки кромок 1,6÷2,4 мм, максимальная длина стежка – 1,0 мм; подъём прижимных лапок до 7 мм. Смазка ручной маслёнкой по отдельным точкам.
И, наконец, последняя группа машин – для выполнения строчек любой сложности, содержащих 300 000 стежков и более (рис. 24). Выпускают такую технику фирмы «Brother», «Sunstar», «Juki», «Mitsubishielectric».
Все эти полуавтоматы построены по одному принципу. Зажим в виде прямоугольных пялец с помощью шаговых двигателей перемещается по плоскости стола в двух координатах, а программа работы задаётся компьютерной системой. Поле обработки изменяется в очень широких пределах от 60100 мм до 250400 мм; есть модели и для больших размеров.
Рис. 24. Полуавтомат для выполнения строчек сложной конфигурации
Скорость работы этого оборудования 2000÷2500 оборотов в минуту в зависимости от тяжести обрабатываемого полуфабриката. Длина стежка от 0,1 до 12,7 мм. Колеблющийся тип челнока обеспечивает хорошую затяжку стежков при любой их длине; увеличенный объём шпули сокращает количество перезаправкок. Количество программ, которые машина удерживает в памяти, – до 700. По своим возможностям это просто вышивальные машины.
Микрокомпьютер обеспечивает пошаговые программирования участков строчки. Но в случае простых конфигураций можно задавать только базовые характерные точки, а соединение их вести прямыми линиями, дугами окружностей, что позволяет сократить необходимый объём информации, вводимой в память машины.
На одном изделии выполняется, как правило, не одна петля, пришивается не одна пуговица. Ведущие фирмы мира создали оборудование для прикрепления группы пуговиц к одному изделию и для выметки группы петель.
Построено оно по следующему принципу. К хорошо зарекомендовавшим себя пуговичным головкам с бункером и петельным машинам с электронным управлением присоединён стол, имеющий подвижную площадку. На этой площадке размещается деталь швейного изделия, например, полочка сорочки. Делается это по упорам и световым отметкам. Затем полочка фиксируется прижимами. По командам, поступающим от системы управления, полочка перемещается в рабочую зону шьющей головки и останавливается. В автоматическом режиме после этой остановки включается цикл пришивки пуговицы (изготовление петли), после завершения которого происходит останов головки, обрезка ниток. Полочка перемещается (автоматически) к следующему месту обработки. Цикл повторяется до тех пор, пока не будет пришита вся группа пуговиц или обмётаны все петли. После окончания обработки в последней позиции включается укладчик и готовая полочка снимается.
Расстояние между пуговицами (петлями) возможно варьировать в 20 различных комбинациях. Один оператор может обслуживать несколько таких полуавтоматов. Общий вид машин приведён на рисунке 25.
Рис. 25. Полуавтоматы для пришивки комплекта пуговиц
и вымётывания группы петель
Современная тенденция построения швейных полуавтоматов связана с совмещением в один общий процесс нескольких различных операций. Так, например, в полуавтомате «Pfaff» 3588-04/020 (рис. 26) объединены фальцевание краёв накладного кармана, настрачивание кармана на половинку джинс и закрепление краёв кармана.
Традиционная схема – фальцевание кармана на прессе, настрачивание кармана на универсальной машине, например DDL-8 700Н-7, и закрепка (LK-1900 A-НS) – требует трёх рабочих мест и, по крайней мере, трёх операторов.
В новом полуавтомате все операции объединены, причем деятельность оператора, в обязанности которого входит только размещение на позиции укладки заготовок (половинка джинс и карман), совмещена во времени с процессом настрачивания.
Прикрепление кармана осуществляется двумя строчками, проходящими эквидистантно боковым сторонам кармана и его нижней стороне, с закреплением верхних уголков кармана. Закрепка выполняется зигзагообразной строчкой. Рабочая головка выполняет прямую строчку и зигзаг, стежок двухниточный челночный. Челнок увеличенный. Скорость работы 4000 оборотов в минуту.
Рис. 2 Полуавтомат для настрачивания накладных карманов
Область шитья 250240 мм. Фальцевание краёв кармана осуществляется холодным способом.
Для того чтобы перейти на обработку кармана иной формы, нужно сменить фальцующий узел и установить новую программу шитья. На смену шаблонов уходит около 5 минут. Специальных инструментов для этой цели не требуется. Программа шитья набирается на пульте управления или вызывается из памяти.
Иногда такой полуавтомат снабжается дополнительным устройством, которое обеспечивает автоматическую намотку шпули и замену её в челночном узле. Когда действует это устройство, производительность увеличивается на 10 %.
Полуавтомат снабжён устройством для автоматического удаления из зоны шитья обработанных заготовок. Укладчик надёжно удерживает пачку из 64 единиц.
В памяти системы управления хранится более 690 модельных вариантов строчки.
Для работы полуавтомата необходим сжатый воздух; давление в сети должно быть 5 атмосфер.
Полуавтомат занимает площадь 1,81,8 м; вес 600 кг.
Ещё один полуавтомат, о котором бы хотелось упомянуть, предназначен для закрепления шлёвок на поясе джинс (рис. 27) – 2650 EV 7 фирмы «Vi. Be. Mac».
Для этого полуавтомата создана специальная головка, у которой две иглы расположены вдоль оси нижнего рукава. Расстояние между ними можно изменить в диапазоне 40÷70 мм.
Взаимодействуют с иглами два челнока. Строчки двухниточные челночные выполняются одновременно, что позволяет прикреплять шлёвку к поясу с двух сторон.
Полуавтомат снабжён устройством для автоматической подачи заготовки шлёвок из рулона. Шлёвка отрезается в нужный размер, края её подгибаются внутрь, и такая сформированная шлёвка подаётся в зону шитья.
Рис. 27. Полуавтомат для прикрепления шлёвок к поясу
У подающего устройства имеется датчик, реагирующий на изменение толщины шлёвочной ленты. Это бывает на стыках между заготовками, которые образуются при изготовлении упомянутой ленты на машинах типа MFB-2600 «Juki» (см. рис. 8 раздела 2). По сигналу датчика утолщённые участки автоматически вырезаются и удаляются.
Шлёвка прикрепляется к поясу строчкой закрепочного типа с числом стежков в ней 28, 36 или 42 (выбирается с помощью операционной управляющей панели). Длина закрепки 7÷22 мм, ширина 1÷3,2 мм. Скорость работы шьющей головки 2500 оборотов в минуту. Время прикрепления одной шлёвки 1,2 сек при числе стежков в цикле 28. Ширина прикрепляемых шлёвок 9÷20 мм.
Задача оператора – только подставить под шьющую головку нужное место пояса.
Размерные параметры полуавтомата 12008001350 мм, вес 230 кг.
7. Оборудование для выполнения операций IV группы
Примерно 6 % всего объёма технологических сборочных операций приходится на обтачивание деталей.
Принципиальная схема обработки тут следующая. Выкроенные заготовки складывают друг с другом, уравнивают по контуру и на определённом расстоянии от него прокладывают соединяющую строчку. Сшитый пакет выворачивают, выправляют и утюжат. По лицевой стороне часто прокладывают отделочную строчку. В зависимости от вида материалов и модели изделия внутрь обтачной детали могут входить прокладки из клеевого и неклеевого материала. Прокладки располагают в пакете заготовок обтачного узла так, чтобы они попадали под соединяющую строчку, что не позволяет прокладке смещаться внутри пакета при эксплуатации изделия.
Часто обтачивание совмещают с подрезкой края пакета заготовок вдоль линии строчки. Этот приём позволяет обеспечить стабильную ширину шва, что после выворачивания и окончательного прессования положительно сказывается на качестве обтачного узла.
Если в обтачном узле детали верха и подкладки выполняются из разных тканей, то, как правило, требуется, чтобы после обтачивания и выворачивания подкладка не выступала за контур детали верха. Это достигается тем, что при стачивании из детали верха вдоль шва создают некоторый избыток ткани (напуск), который после выворачивания образует кант, скрывающий подкладку.
Таким способом изготавливают воротники, манжеты, паты, клапаны, погончики. Иногда так обрабатывают борта мужских костюмов.
Здесь есть такая особенность: в процессе обработки необходимо обеспечить строгую ориентацию рабочей головки относительно обрабатываемого контура (рис. 28), так как любые отклонения от этого влияют на переплетение ниток в стежках челночной строчки (без узелка или с узелком), на саму возможность образования челночной строчки, на качество работы ножа, на использование многоинструментной обработки, на работу отклонения иглы вдоль строчки.
Всё это необходимо учитывать при создании техники для обтачивания деталей, особенно если подача полуфабриката в рабочей зоне осуществляется без сопровождения руками оператора, то есть в автоматическом режиме.
|
|
|
|
|
|
|
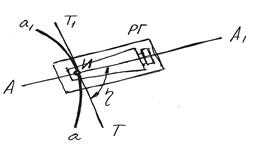
Рис. 28. Схема, поясняющая условие ориентации рабочей головки
по отношению к контуру строчки:
РГ – рабочая головка; И – игла; аа 1 – контур обтачивания;
АА 1 – ось, связанная с рабочей головкой;
ТТ 1 – касательная к контуру обтачивания, проведённая в точке обработки;
– угол, определяющий ориентацию рабочей головки
Для нормальной работы угол должен быть в пределах 90±20°.
Первый шаг на пути к автоматизации прокладывания строчки – устройство на базе универсальной швейной одноигольной с ножом машины, действующее по жёсткому шаблону (рис. 29), «Pfaff» 9083-3/99. Машина оснащена механизмами автоматического останова и обрезки ниток.
Рис. 29. Полуавтомат для обтачивания мелких деталей
В качестве двигателя заготовок здесь используется непрерывно вращающийся зубчатый диск, кинематически связанный с главным валом головки. Диск взаимодействует с зубчатым венцом плоской кассеты. В кассете имеется зона, куда укладываются заготовки: манжеты, клапаны, воротники. Чтобы заготовки не сдвигались, они фиксируются прижимом.
При работе головки вращающийся диск перемещает кассету по плоскости стола, и под иглу и нож всё время попадают новые участки заготовки. Таким образом происходит их стачивание и одновременная подрезка припуска.
Кассета имеет разделительную пластину. При укладке в кассету заготовок одна размещается под разделительной пластиной, а вторая – сверху. Заготовка, огибающая разделительную пластинку, после стачивания будет образовывать некоторый излишек ткани – напуск. Этот напуск пойдёт на образование канта из верхней детали после вывёртывания на лицевую сторону сшитого пакета.
Фирма «Durkopp/Adler» выпускает полуавтомат для той же цели класса 739-23-1. Но он посложнее конструктивно. Выпускает такое же оборудование и «AMFReece».
Стоит отметить, что и в России есть техника подобного назначения – полуавтомат 570 класса, достаточно производительный, весьма простой и надёжный (рис. 30).
Широкая его применяемость объясняется следующим. При обтачивании, как и при других сборочных работах, концы строчек принято закреплять обратной строчкой длиною 7÷10 мм или специальной закрепкой. Для выполнения строчки в обратном направлении на полуавтомате его необходимо оснастить следующими техническими средствами: механизмом останова шьющей головки при заданном положении игловодителя, механизмом переключения направления подачи, механизмом обрезки ниток. Всё это несколько усложняет и удорожает конструкцию.
Закрепки по назначению можно разделить на два типа: технологические и конструктивные. Конструктивные закрепки предохраняют шов от распускания в период эксплуатации изделия. Закрепки технологические, составляющие около 70 % от общего числа закрепок, необходимы лишь для обеспечения чёткого процесса сборки узла или изделия. На последующих операциях такие строчки обычно закрепляются повторно. Например, закрепление строчки при обтачивании клапана только предохраняет строчку от распускания в процессе выворачивания на лицевую сторону.
Однако есть более простые способы временного закрепления строчки. К ним относятся: выполнение цепочки из ниток, продолжающей обтачную строчку, учащение стежков на некотором участке строчки и закрепление посредством перехода строчки с нескольких слоёв пакета на один.
Исследованиями, проведёнными в ЦНИИШП, установлено, что, выполнив в конце обтачной строчки вне ткани цепочку из ниток в 10÷16 стежков, удаётся предотвратить шов от распускания при последующих операциях.
Рис. 30. Отечественный полуавтомат для обтачивания
Основываясь на этом, создатели полуавтомата 570 класса максимально упростили конструкцию, не включив в неё несколько сложных механизмов. Полуавтомат приобрёл те положительные качества, о которых упоминалось, и получил заслуженное признание у производственников.
Процесс обтачивания с одновременной подрезкой края заготовок в этом полуавтомате идёт почти непрерывно: кассета здесь двухпозиционная. Оператор только укладывает заготовки в кассету, а при определённом навыке делает это на ходу. Съём обработанных изделий идёт автоматически, цепочкой.
Переход на другой размер или другую форму обтачной детали осуществляется сменой кассет. Операция очень проста и выполняется самим оператором. Подналадки машины не нужно.
Оператор осваивает работу на таком оборудовании очень быстро, высокой квалификации не требуется.
После обтачивания заготовки вывёртываются, расправляются на металлических шаблонах и приутюживаются. Получившиеся детали (клапаны, манжеты, воротники) имеют очень малые отклонения в размерах друг от друга, что очень важно при проведении последующих сборочных операций, например, притачивание клапана к карману в рамку. Клапан всегда будет чётко соответствовать прорези кармана и вход в карман всегда будет с обеих сторон перекрыт клапаном.
Очень удобно поэтому описанное оборудование использовать в комплекте с другими полуавтоматами, например, AРW-195 N (см. разд. 5).
При обтачивании деталей под последующее выворачивание их на лицевую сторону нет необходимости строго выполнять строчку в уголках детали. Резкий перелом строчки можно заменить скруглением, так как после выворачивания на детали за счёт толщины материала все равно в этом месте контур пойдёт по некоторой дуге.
Иное дело, если на детали прокладывается отделочная строчка. Так, например, на воротнике сорочки перелом строчки должен точно попасть в угол воротника.
Фирма Pfaff предлагает машину класса 2481 с системой SENSEWMAT, позволяющей распознавать край детали и автоматически изменять длину последних стежков для точного попадания в угловую точку. Машина применяется для прокладывания отделочных строчек по воротникам, клапанам, карманам.
Обтачивание мелких деталей: клапанов, пат, погончиков идёт в кассетах, причём кассета является подвижным элементом относительно стационарно установленной шьющей головки. Но при обтачивании воротников, бортов кассета становится слишком громоздкой. В этом случае схему лучше поменять: кассета с закреплёнными в ней деталями становится неподвижной, а вокруг неё «бегает» швейная головка. На рисунке 31 показан полуавтомат для обтачивания воротников плащей, где реализована эта идея.
Рис. 31. Полуавтомат с подвижной головкой
Конструкторская мысль не стоит на месте, идут поиски возможностей соединения заготовок без жёстких устройств, удерживающих полуфабрикат при подаче его под шьющие механизмы.
Новая серия фирмы «Juki» АЕС-200 – это машины с автоматическим контролем положения края ткани. Они позволяют стачивать две детали по контуру со срезом любой конфигурации без подправления заготовок руками, без уравнивания краёв, без перехватов. Важной особенностью является то, что кривизна контуров стачиваемых деталей может быть разной, также как и плотность заготовок в паре, например деталь верха изделия и подкладка.
У машины (рис. 32) имеются два чувствительных сенсорных датчика для верхнего слоя и для нижнего слоя пакета. Датчики управляют двумя шаговыми двигателями, которые приводят в движение транспортирующие зубчатые ролики, контактирующие с обрабатываемым полуфабрикатом и автоматически обеспечивающие равномерную подачу и прокладывание строчки на заданном расстоянии от края. Роль оператора сводится только к тому, чтобы сложить соединяемую пару заготовок и подложить краешек пакета под лапку. Включается машина автоматически: ещё один датчик реагирует на наличие материала под лапкой.
Рис. 32. Машина для стачивания деталей
Обработанные заготовки можно снять руками, а может это сделать механический съёмник-укладчик.
На базе описанной машины есть вариант АЕС-200/S200 – это автомат, выполняющий складки на изделии. В один приём закладывается и застрачивается складка заданной ширины по всей длине заготовки.
Для обмётывания краёв заготовок, имеющих достаточно сложный профиль, создан полуавтомат на базе оверлока МО-6900 серии (рис. 33).
Рис. 33. Полуавтомат для обмётки срезов
Эта машина также управляется двумя сенсорами и чётко контролирует край заготовки, например, половинки брюк. На столе машины расположен ряд отверстий для подачи воздуха и при включении машины в работу заготовка приподнимается над столом на воздушной подушке, что облегчает, и очень значительно, её транспортировку.
8. Машины для выполнения операций, где полуфабрикат не раскладывается на плоскость
Как указывалось ранее, большинство швейных сборочных операций выполняется с деталями, которые можно удобно расположить на платформе швейной машины и рабочем столе, так как они являются плоскими или близкими к таковым. Но порядка 20 % операций, как правило, у почти готового изделия приходится проводить, действуя в пространстве. Втачивание рукавов в закрытую пройму (пиджаки, блузки, пальто), подшивка низков брюк, стачивание шаговых срезов в джинсах. Такие операции очень специфичны. И поэтому оборудование для их выполнения разрабатывается специализированное, конкретное, узкого назначения.
Приведём несколько примеров.
Машина фирмы «Juki» DLN-6390 (рис. 34) предназначена для подшивки низков брюк рабочей одежды или для той же операции на джинсах.
Рис. 34. Машина для подшивки низков брюк
Это одноигольная машина двухниточного челночного стежка с цилиндрической платформой, диаметр которой не превышает 180 мм. Головка установлена на столе так, что цилиндрическая часть платформы образует консоль. На платформе крепится приспособление для подгибки среза перед попаданием его под нажимную лапку. Челнок увеличенный вращающегося типа. Длина стежка в стандартном варианте 3,2 мм. При установке сменных деталей – 2,3, 2,8, 3,6 мм. Подъём нажимной лапки 14 мм. Для надёжной транспортировки заготовок машина снабжена тянущими роликами.
Машина выпускается в двух вариантах исполнения: без обрезки ниток и с автоматической обрезкой ниток (DLN-6390-7).
Механизмы машины прошли компьютерную проработку, чтобы найти оптимальные возможности в плане переналадки на различные виды материалов со стабильным качеством строчки. Максимальная скорость вращения главного вала 5000 оборотов в минуту.
Кажется, в этой операции («подшивка низков брюк») простая строчка, одного направления, без изломов и поворотов, даже закрепка не требуется, так как строчка в конце возвращается на своё начало и короткий двукратный проход по одному месту предохраняет её от распускания.
Однако всё несколько сложнее. Дело в том, что строчка выполняется на почти готовом изделии, на его трубчатой части сравнительно небольшого диаметра. Разложить на плоскости платформы машины для обработки возможно лишь небольшой участок, прошив который, нужно изделие расправить, зафиксировать руками следующий участок обработки и продолжить строчку. Ясно, что без частых остановок работа невозможна. И таких остановок должно быть пять-шесть. Отсюда низкая производительность. Кроме того, приходится при этом поворачивать готовое изделие, что весьма неудобно. Нельзя забывать и о том, что перед выполнением строчки срезы нужно подогнуть. Несмотря на то, что для подгибки выпускают специальные приспособления, всё равно, как говорится, «рук не хватает».
В этих условиях машина DLN-6390 просто незаменима. Надев на цилиндрическую платформу трубчатую часть брюк и заправив срез в направитель перед лапкой, оператор после включения в работу машины просто поворачивает изделие, немного помогая двигателю ткани швейной машины. Консольное расположение на столе шьющей головки освобождает слева от работающего большую зону, где может быть установлен кронштейн – зажим, в котором можно закрепить сразу несколько изделий и вести обработку в пачке.
Машиностроители практикуют создание машин с цилиндрической платформой и на других базах, например, на базе зигзаг-машины. Назначение машины такое же, только строчку она выполняет челночную зигзагообразную (рис. 35). Стандартный зигзаг до 8 мм и трёхшаговый зигзаг с шириной до 10 мм. Скоростной режим 4500÷5000 оборотов в минуту в зависимости от материала и условий технологической операции. Челнок вращающегося типа с титановым покрытием внутренней поверхности.
Рис. 35. Машина зигзаг для прокладывания строчки
на деталях трубчатой формы
Подшивка низа швейных изделий, таких как юбки, платья, пальто, производится и цепными строчками. Машины для этой цели показаны на рисунке 3 При подшивке пакет состоит из двух слоёв. Верхняя часть материала прокалывается иглой насквозь, а нижняя часть захватывается иглой лишь частично, и на лицевой стороне изделия строчки не будет видно.
Осуществляется строчка изогнутой иглой, двухрожковым петлителем, зубчатой транспортирующей рейкой, прижимными подпружиненными лапками и выдавливателем соединяемых слоёв ткани.
Операция проводится на почти завершённом в изготовлении изделии. На плоскость его не развернуть, да и объёмность предмета труда (пальто, платье) простоты не добавляет. Автоматизация процесса затруднительна. Поэтому совершенствование этой техники ведётся только в плане повышения надёжности работы. В технологическом плане предел здесь, пожалуй, достигнут. Совершенствованием подобного оборудования, созданием различных вариантов и комбинаций стежков, занимаются фирмы «Strobell» «Maier» (обе Германия).
Рис. 3 Машины для подшивки низа швейных изделий
Ряд оригинальных рукавных машин появился для шитья одежды и некоторых технических изделий. Оригинальность здесь заключается в том, что соединённые срезы направляются не на рукав машины, не поперёк рукава, а «сходят» с него. Это позволяет обрабатывать детали цилиндрической формы достаточно большой длины – рукава сорочек, брюки, джинсы.
Машина имеет П-образную платформу (рис. 37). Подача материала осуществляется зубчатой рейкой в направлении от оператора. Готовая часть изделия, сошедшая с рукава платформы, не мешает подвести под нажимную лапку новые участки срезов заготовки. В последнее время машина находит применение не только в швейной промышленности. Например, в коммунальном хозяйстве, где изготавливают рукава из специальных материалов для перекачки жидкостей или в химической промышленности при производстве рукавов из стеклоткани для фильтров сажевых производств. Длина таких изделий достигает нескольких метров, а то и десятков.
Машины этого типа имеют две иглы или три иглы, взаимодействующие с двумя или тремя петлителями, образуя при этом строчки, состоящие из стежков двухниточного цепного переплетения. Расстояние между иглами можно поменять, установив на машину детали из дополнительного комплекта: иглодержатель, рейку, лапку, игольную пластинку.
Как правило, на машину устанавливается приспособление, обеспечивающее подгибку срезов для выполнения шва «в замок». Нужно иметь в виду, что, изготавливая такой шов на узлах одежды, имеющих поперечные швы, в местах перехода создаются зоны, где число слоёв материала, подлежащих проколу иглами, сильно увеличивается и может достигать 1 Так, стачивая боковые и рукавные срезы сорочки или шаговые швы на джинсах, с этим моментом придётся столкнуться обязательно. С целью надёжного продвижения полуфабриката под иглами независимо от местных утолщений на машине устанавливается дополнительный тянущий ролик, позволяющий более надёжно переходить через швы. Вращение ролика синхронизировано с движением рейки.
Рис. 37. Машины с П-образной платформой
Некоторые технические данные. Скоростной режим 3000÷4000 оборотов в минуту в зависимости от материалов. Длина стежка регулируется в диапазоне 1,2÷4,2 мм. Подъём нажимной лапки – 10 мм. Минимальный диаметр рукава 171 мм (на изделии).
Дальнейшее развитие рассматриваемая техника получила в совместной разработке фирм «Juki» и «UnionSpecial» – класс 35 800. Особенностью машины является дифференциальный двигатель ткани, что позволяет получать длинные швы без искривлений и волн или соединять друг с другом различные по плотности материалы, также обеспечивая ровноту строчки. Машина выпускается в двух модификациях: тяжёлой (для джинс) и лёгкой (стачивание срезов трикотажных изделий).
Применение машин с рукавной платформой, когда готовая часть швейного изделия «сходит с рукава», позволяет в ряде случаев существенно сократить затраты времени на выполнение ручных вспомогательных приёмов. Пример – изготовление джинс. Так, если боковые срезы джинс соединены на стачивающе-обмёточной машине, то, выполняя затем шаговые швы на машине с П-образной рукавной платформой, удаётся снять такую трудоёмкую операцию, как «выворачивание изделия», так как шов сразу проходит по лицевой стороне.
В технологическом процессе изготовления многих видов изделий есть операция, от чёткости исполнения которой зависит общее качество изделия, и если не всё, то очень многое. Это – втачивание рукавов в пройму. Рукава с проймами соединяют стачным швом шириною 10 мм с направлением припусков на швы в сторону рукава.
Перед соединением проверяют точность линий срезов рукавов и пройм. В рукавах проверяют их симметричность, длину, ширину и наличие контрольных рассечек. Контрольные рассечки проверяются по проймам полочек и спинки.
Длина оката рукава должна быть больше длины линии проймы. Разница зависит от модели и вида проймы и составляет 0,4 мм на 10 мм длины проймы для полушерстяных тканей с содержанием синтетики до 30 %; до 1,5 мм на 10 мм длины для чисто шерстяных материалов. В связи с этим втачивание сопровождается обязательной посадкой ткани по срезу головки рукава. Величина посадки по периметру проймы не остаётся постоянной. Для создания необходимого внешнего вида, для обеспечения свободы движения руки посадку оката рукава распределяют по длине линии проймы различно в зависимости от требований, предъявляемых к тому или другому участку. Таких участков по длине проймы обычно от трёх до шести в зависимости от назначения изделия.
На рисунке 38 в качестве примера приведена схема, где окат рукава разделён на пять участков; изделие – жакет женский из гладкокрашеной ткани. Участок 1 – от контрольной надсечки на линии переднего переката до переднего шва и далее на такое же расстояние по нижней части рукава. Рукав здесь соединяют с проймой без посадки, что обеспечивает фиксацию положения линий переднего переката. Участок 2 – от контрольной надсечки на линии переднего переката до плечевого шва, не доходя до него 25÷30 мм. Посадка рукава на этом участке создаёт красивую обтекаемую форму на внешнем участке оката и обеспечивает необходимую свободу движения руки. Посадка здесь значительная и, ориентировочно, составляет 30÷33 % всей посадки. И распределение её по участку не одинаково: в центре, на наиболее косом срезе оката, она больше, а к концам участка её уменьшают. Участок 3 – область плечевого шва на 25÷30 мм, в одну и другую сторону от него. Посадка необходима для оформления верхней части оката. Величина посадки должна обеспечивать свободное огибание внутренних швов втачивания на данном участке и составляет 10÷12 % всей посадки. Участок 4 – часть оката рукава, расположенная со стороны спинки от конца участка 3 до контрольной надсечки на линии локтевого переката. С учётом необходимости оформления оката рукава на данном участке и обеспечения свободы движения посадка оката должна быть здесь до 30÷33 % всей посадки, примерно так же, как на участке 2. Участок 5 – часть оката рукава между концом участка 4 и началом участка 1. Посадка составляет 20÷24 % всей посадки.
Рис. 38. Схема деления оката рукава на участки
Как видим, операция достаточно сложная, трудоёмкость её весьма велика. Кроме того, велико и разнообразие вариантов посадки, которое устанавливается для различных конкретных случаев.
Применение для этой операции универсальных машин нецелесообразно, так как оно возможно только после предварительного вмётывания рукава в пройму, осуществляемого вручную по рассечкам для обеспечения необходимого качества посадки.
В последние годы созданы специальные машины, которые существенно повышают производительность. Назовём «Juki» DP-2100; «Durkopp/Adller» 550-16-26; «Pfaff» 3834-14/21 (рис. 39).
Операция по втачиванию рукавов производится с объёмным объектом и не на плоскости, а в пространстве. В связи с этим машина изготовлена в варианте с колонкой, на которой будет размещаться изделие.
Сухая головка, прямой привод – эти достижения вошли составной частью в конструкцию машины. Но главной особенностью является исполнение её транспортирующего узла. Он выполнен в виде пары роликов и прижимной лапки (у машины фирмы «Juki» пара транспортирующих ремешков). Движение этих роликов раздельное и управляемое. Разность в скоростях движения роликов определяет разницу в перемещении контактирующих с ними слоёв пакета, за счёт чего производится посадка. Процесс посадки контролируется программной системой и отображается на экране жидкокристаллического дисплея. Система может содержать в памяти 99 различных программ посадки по участкам. Таких участков может быть до 30.
Процесс программирования максимально упрощён: просто на пульте, сенсорно. Кроме того, система даёт подробную визуальную информацию о конкретной ситуации в проведении операции в данный момент и о том, что будет выполняться в следующий этап.
Длина челночного стежка регулируется от 1,5 до 6,0 мм. Скорость работы – 3500 оборотов в минуту. Толщина пакета под транспортирующими органами – до 3,5 мм.
Рис. 39. Машина для втачивания рукава в пройму
Важным моментом, который обязательно нужно отметить, является стабильность воспроизведения программы. Отсюда качество: и правый, и левый рукав будут вписаны в пройму одинаково.
В машине предусмотрено выполнение и ряда вспомогательных функций: автоматический останов в конце операции, подъём верхнего транспортирующего ролика, обрезка ниток.
9. Столы для швейных машин
В предыдущих разделах, когда речь шла о назначении и технических данных швейных машин, имелась в виду, прежде всего, рабочая головка, с помощью которой осуществляется задуманный технологический процесс. Однако только наличие высокопроизводительной и надёжной шьющей головки мало. Необходимо создать оператору комфортные условия для его нелёгкой работы, необходимо оснастить рабочее место так, чтобы заготовки и вспомогательные инструменты были под рукой, чтобы было удобно направлять полуфабрикат в рабочую зону, чтобы был обеспечен лёгкий доступ к определённым узлам в случае небольшого ремонта без удаления головки из технологического процесса.
Важной составляющей рабочего места швеи-мотористки (оператора) является стол.
Рабочий стол состоит из станины и крышки. По конструкции оба эти элемента различны для различных машин. Наиболее употребим стол на основе простой прямой станины (рис. 40) и крышки с вырезом под платформу шьющей головки (рис. 41).
Рис. 40. Станина для универсальных швейных машин
Такой стол применяется для многих швейных процессов, когда используются универсальные головки челночного и цепного стежков. В этом случае плоскость платформы машины совпадает с плоскостью крышки стола и полуфабрикат удобно расправить на столе и точно направить под иглу.
Крышка изготавливается из многослойной фанеры и покрывается пластиком.
Шьющая головка в вырезе крышки устанавливается на поворотных петлях. На крышке монтируется стойка для бобин ниток и ящик для хранения сменных лапок, приспособлений, шпулек, иголок. Там же находятся ножницы, пинцет, отвёртки, кисточка для чистки рабочих органов машины.
К станине или крышке крепится электропривод, управление которым осуществляется педалью, размещённой на нижней продольной стяжке станины. Высота стола обязательно регулируется в зависимости от физиологических данных оператора.
Станина устанавливается на резиновые башмаки или резиновые ролики, которые уменьшают вибрацию и шум, возникающие при работе установки. При использовании станины с роликами её, естественно, легче перемешать на площади цеха и устанавливать на необходимом рабочем участке.
Для рабочих головок закрепочных, пуговичных, петельных в крышке стола вырез не делается, сверлится только несколько отверстий под крепёж головки и изготавливается паз под приводной ремень (когда это необходимо).
Рис. 41. Крышка стола для установки рабочей головки в вырезе
Оверлоки и стачивающе-обмёточные машины ставятся на крышку стола по двум схемам: первая – когда игольная пластинка, платформа машины и крышка стола составляют единую плоскость и вторая – когда рабочая головка поднята над поверхностью крышки стола. Варианты выбираются исходя из конкретных технологических условий. Первая схема удобна в случае необходимости разместить и расправить заготовку перед шитьём, например, при обработке планки на полочке сорочки. В случае, когда нужно только слегка поддержать полуфабрикат в процессе обмётывания его срезов, удобен второй вариант размещения.
В случае «утопленного» варианта установки шьющей головки в крышке стола передняя её часть делается откидной (рис. 42), чтобы обеспечить лёгкий доступ к петлителям и нижнему ножу.
Рис. 42. Крышка стола для «утопленного» варианта размещения
шьющей головки
При осуществлении некоторых технологических операций, как правило, с уже почти готовым изделием очень удобно иметь слева от работающего свободную зону, куда можно поставить передвижной зажим, в котором закрепить пачку изделий. С этой целью шьющие головки устанавливаются на одноопорные столы, обеспечивающие их консольное размещение (рис. 43).
Рис. 43. Станина одноопорного стола
Для машин с П-образной платформой применяются столы на шести опорах, обеспечивающие свободную зону спереди и слева (рис. 44).
Рис. 44. Шестиопорная станина
Для швейных полуавтоматов, как правило, проектируются индивидуальные станины.
Рабочее место оснащается также стулом, корзинками для полуфабриката и мусора, кронштейнами.
Швейное оборудование в «чистом» виде, то есть в таком, в котором оно выпущено машиностроительным заводом, на швейном предприятии может использоваться в несколько ограниченной области. Особенно это касается машин, которые принято называть «универсальными» по признаку специализации. Они не оснащены какими бы то ни было дополнительными средствами для пошива и могут применяться для выполнения довольно широкого круга операций, и здесь квалификация оператора, его умение выходят на первый план при обеспечении высокого качества выпускаемых изделий.
С другой стороны, в технологическом плане швы швейного изделия весьма разнообразны. Простые соединительные применяются в незначительном объёме. Очень много других, более сложных (см. табл. 5.2).
Некоторые виды швов можно выполнить вручную за счёт профессионального мастерства и числа проходов, а некоторые – просто невозможно. В связи с чем создано большое количество приспособлений, которые устанавливаются на швейную головку и обеспечивают необходимое формообразование текстильного материала. Качество теперь в меньшей степени зависит от работающего, а производительность, естественно, возрастает.
Для уменьшения трудоёмкости, повышения качества, а следовательно, и производительности выполнения технологических операций применяется группа технических средств, называемых технологической оснасткой (или приспособлениями малой механизации).
Всё многообразие этих приспособлений в зависимости от типа выполняемого с их применением шва по классификации, предложенной ЦНИИШП, разбито на шесть групп.
В первую группу объединены приспособления для выполнения соединительных и отделочных швов (без подгибания материала). Во вторую, третью и четвёртую группы входят приспособления для выполнения таких швов, где требуется подгибать один или несколько слоёв материала. При этом во вторую группу входят приспособления, где подгибание не связано с соединением деталей (например, подшивание низа брюк), а в третью группу – приспособления для выполнения швов, где одновременно с подгибанием соединяют две или более деталей (за исключением окантовывания срезов). Приспособления для выполнения окантовочных швов объединены в четвёртую группу. В пятую группу входят приспособления для обмётывания петель, пришивания пуговиц, крючков и другой фурнитуры; в шестую – прочие приспособления к швейным машинам.
Подробнейшим образом этот материал изложен в книге «Справочник по швейному оборудованию» (М.: Лёгкая индустрия, 1981). Примеры приспособлений приведены на рисунке 45.
Работа по рационализации рабочих мест и методов труда носит комплексный характер и включает в себя применение методов микроэлементного анализа трудовых процессов и методов проектирования рабочих мест по агрегатному принципу на основе использования типовых устройств для механизации ручных приёмов труда. Важную роль при этом играет организационная оснастка рабочих мест (оргтехоснастка ), которая представляет собой набор элементов, обеспечивающий рациональное построение трудового процесса, размещение и хранение деталей и инструмента, улучшение условий труда. Организационная оснастка способствует сокращению времени на выполнение вспомогательных приёмов и позволяет без существенных капитальных затрат обеспечить на рабочем месте рост производительности труда на 5–15 %.
Сопоставим затраты времени на выполнение конкретной операции при двух вариантах оснащения рабочего места. Вариант 1 (базовый): на рабочем месте установлен стандартный промышленный стол со швейной головкой, обращённый левым торцом к междустолью. Вариант 2: промышленный стол оснащён оргоснасткой.
Рис. 45. Приспособления малой механизации
Выполняемая операция – «стачать боковые детали с деталями полочек подкладки мужского пальто». Схемы рабочих мест представлены на рисунке 46, затраты времени на выполнение приёмов работы по обработке правой и левой полочек – в таблице 7.
Рис. 4 Схемы рабочих мест
Таблица 7
Затраты времени на выполнение приёмов работы
по обработке правой и левой полочек
№ приёма работы | Приём работы | Затраты времени, с | |
вариант 1 | вариант 2 | ||
1 | Взять левой рукой с междустолья перед и, подхватывая его рукой за срез обработки, переместить к рабочей зоне | 1,8 2 | – |
2 | Взять из пачки двумя руками боковую деталь переда, лежащую слева на крышке стола, за срез обработки и совместить с передом | 2,1 2 | – |
3 | Взять из пачки, лежащей на правой дополнительной плоскости, одновременно двумя руками боковую деталь переда и перед, лежащий на левой дополнительной плоскости или наклонной полке | – | 2,1 2 |
4 | Остальные приёмы | 18,5 2 | 18,5 2 |
Итого для одного изделия | 44,8 | 41,2 |
В первом варианте работница, выполняющая операцию сидя (стул 8), берёт левой рукой с междустолья 3 полочку 2 и размещает её на промышленном столе 4 в рабочей зоне швейной головки 5. Затем она обеими руками берёт из пачки боковую деталь полочки 1, совмещает детали, стачивает их и размещает обработанные детали 7 на тележке-стеллаже
Во втором варианте выполняющая операцию сидя (стул 8) работница одновременно обеими руками берёт из пачки, лежащей на правой дополнительной плоскости 6 к промышленному столу 4, боковую деталь полочки 7, а из пачки, лежащей на левой дополнительной плоскости или наклонной полке 9, деталь полочки 1. Далее работница совмещает детали, стачивает их на машине 5 и размещает обработанные детали 3 на тележке-стеллаже 2.
Как видно из приведённого сопоставления, последовательное выполнение приёмов «взять деталь» может быть заменено на параллельное, если на рабочем месте детали расположены в удобной для работы зоне, а это даёт рост производительноститруда на 8,8 %. Кроме того, обеспечение порядка на рабочем месте, сокращение траекторий трудовых движений, уменьшение затрат времени на перехваты способствуют меньшей утомляемости работницы.
Разработан комплект элементов оргоснастки,который получил название УСО-1(унифицированная сборная оргоснастка). Из набора элементов, входящих в УСО-1, можно компоновать различные по назначению рабочие места. Индекс 1 обозначает, что комплект предназначен для оснащения рабочих мест со стандартным промышленным столом и швейной машинойс плоской платформой. Комплектом можно оснащать машины 97-А класса, 1597 класса, 1022 класса завода «Промшвеймаш» и т.д.
Основное назначение комплекта УСО-1 – изменение геометрии крышки стола, применение полочек и кронштейнов для размещения пачек деталей. В УСО-1 входят функциональные элементы, монтажные элементы и крепёжные детали.
Функциональные элементы выполнены в виде плоскостей различных размеров, которые служат для изменения формы и размера крышки стола и для установки вспомогательных полочек нарабочем месте. Типы функциональных элементов приведены в таблице 8.
Таблица 8
Типы функциональных элементов
Номер элемента | Наименование элемента | Марки-ровка | Эскиз | |
1 | 2 | 3 | 4 | |
1 | Плоскость дополнительная | ![]() |
||
2 | Плоскость передняя | ![]() |
||
3 | Подлокотник | ![]() |
||
4 | Плоскость боковая правая | ![]() |
||
1 | 2 | 3 | 4 | |
5 | Полка | П50-п | ![]() |
|
6 | Наклонная полочка | ![]() |
||
Примечание. *Обозначения П10, П11 и т.д. предполагают различные размеры А и Б. |
Размеры этих элементов рассчитаны на присоединение к крышке стандартного размера (1060575 мм). Плоскостные элементы изготовляют из фанерных плит толщиной от 15 до 20 мм и покрывают их пластиком.
Все функциональные элементы (плоскости) монтируются на столе с помощью группы монтажных элементов– рам, кронштейнов, стоек.
Монтажные элементы подразделяютсяна две группы: базовые исоединительные. Как говорит само название, базовые элементы (элементы 1–5 в таблице 9 служат основой для сборки рабочих мест инесут на себе основную нагрузку, а с помощью соединительных элементов (элементы 6–10) осуществляется необходимая компоновка (соединение плоскостей на рабочих местах).
Базовые, соединительные и функциональные элементы связываются друг с другом с помощью крепежных деталей – болтов, винтов, шурупов, гаек ишайб.
Рама Р1 является основным монтажным элементом. Она предназначена для установки на рабочем столе дополнительных плоскостей с левой стороны, спереди и сзади крышки стола. Рама закрепляется с нижней стороны крышки на левой стороне стола.
Таблица 9
Типы монтажных элементов
Номер элемента | Элемент | Марки-ровка | Эскиз | |
1 | 2 | 3 | 4 | |
1 | Рама | Р1 | ![]() |
|
2 | Кронштейн | Р2 | ![]() |
|
3 | Кронштейн угловой | Р3 | ![]() |
|
4 | Кронштейн инструментального ящика | Р4 | ![]() |
|
5 | Уголок соединительный | Р5 | ![]() |
|
6 | Стойка | С1 | ![]() |
|
7 | Кронштейн | ![]() |
||
1 | 2 | 3 | 4 | |
8 | Кронштейн | К20 | ![]() |
|
9 | Кронштейн | К30 | ![]() |
|
10 | Кронштейн | К40 | ![]() |
Подобную же роль, но с меньшей несущей нагрузкой, выполняют кронштейны Р2 и Р3. Первый устанавливают под крышкой по переднему её срезу, а второй – в углах крышки по её правому торцу. Схема установки базовых монтажных элементов на крышку стола показана на рисунке 47.
Рис. 47. Схема установки базовых монтажных элементов
на крышку промышленного стола
Рама Р1 и кронштейны Р2 и Р3 имеют направляющие в виде трубок. В эти трубки могут входить соединительные элементы К10, К11, К12 и К30, так как они выполнены из стержней круглого поперечного сечения диаметром, несколько меньшим диаметра отверстия трубок рамы Р1 и кронштейнов Р2 и Р3.
К соединительным элементам К10,КП, К12 и К20 прикрепляются функциональные элементы (плоскости). Прикрепление производится с помощью гаек и винтов.
За счёт имеющейся резьбовой регулировки добиваются, чтобы присоединяемые плоскости находились на одном уровне с крышкой стола, и с помощью соединительных уголков Р5 окончательно фиксируют найденное положение.
Кронштейны типа К20, К30 и К40, а также стойки типа С1 используют для размещения плоскостных элементов вне плоскости крышки стола. Так, на кронштейне К30 полка размещается параллельно крышке стола. Кронштейн К20 имеет возможность поворота опорной площадки относительно установочного стержня. Поэтому установленная на этот кронштейн плоскость может быть размещена наклонно к крышке стола.
Общий вид варианта рабочего места, собранного из типовых элементов оргоснасткиУСО-1,показан на рисунке 48.
Рационализация трудовых процессов, связанная с уменьшением траекторий движения работницы и обеспечением порядка на рабочем месте, потребовала применения крышек столов уменьшенной площади и станин, имеющих только одну стойку. Такие однотумбовые столы всё чаще используются в технологических процессах изготовления одежды.
Завершающим элементом организации рабочего места оператора швейной машины являются транспортные средства , позволяющие передавать полуфабрикат по технологической цепочке от одного рабочего места к другому. Таким элементом являются бесприводные напольные транспортные средства – тележки.
Примеры транспортных средств представлены на рисунке 49.
В технологических процессах заготовки и монтажа используют тележки четырёх типов, каждый из которых имеет несколько модификаций.
Тележки разных модификаций отличаются друг от друга размерами и числом поверхностей для укладки деталей и полуфабрикатов.
Тележка-стеллаж – это металлический остов на четырёх колёсах, на котором смонтировано от одной до семи плоскостей.
Тележки-контейнеры представляют собою одну или несколько ёмкостей (корзин), применяемых для хранения и транспортирования пачек деталей.
Третий тип – тележки-кронштейны. Они предназначены для транспортирования полуфабрикатов больших размеров при укладке их наперевес.
Рис. 48. Общий вид рабочего стола
Четвёртый тип – тележки-зажимы, где пачка деталей, как правило, достаточно длинных закрепляется за один конец, при свободном втором. Это позволяет использовать тележку-зажим как организационную оснастку, ведя обработку деталей, не разбивая пачки.
Новинка в области организации производства – конвейерная система, обеспечивающая передачу изделия по сборочному процессу от одного рабочего места к другому в подвешенном состоянии. Управление полностью компьютеризировано.
Что это даёт? Когда изделие передаётся в пачке, её завязывают, чтобы сохранить порядок, и, естественно, заготовки мнутся. В подвешенном состоянии в этом плане режим щадящий, а это меньше затрат на влажно-тепловую обработку в конце.
Конечно, система достаточно сложная и, естественно, дорогая. Но никаких тележек, никаких вспомогательных рабочих для передачи. Отсутствуют междустолья, и нет жёсткой привязки к одному месту технологического оборудования.
Преуспели здесь фирмы «Eton» (Франция), «TwinStarGroup» (Сингапур) (рис. 48).
Понятно, что такая система хороша для изготовления стабильных изделий в больших партиях.
Рис. 49. Виды транспортных средств, применяемых
на заготовительных и монтажных участках
Рис. 50. Конвейер для передачи изделий по процессу
и обработке их в подвешенном состоянии
В мелкосерийном производстве перспективный подход – организация гибких модулей в пошивочных цехах. Под модулем понимается рабочее место, оснащённое набором оборудования, позволяющего выполнять группу различных технологических операций, базирующихся на различных типах строчек, например, двухниточных челночных с помощью универсальной швейной машины и цепных на оверлоке или на подшивочной машине. Возможны различные комбинации.
Библиографический список
1. Зак И.С., Полухин В.П., Лейбман С.Я. Комплексно-механизи-рованные линии в швейной промышленности. – М.: Легпромбытиздат, 2008. – 320 с.
2. Кокеткин П.П. Пооперационная машинноавтоматизированная технология одежды. – М.: Легпромбытиздат, 2008. – 232 с.
3. Франц В.Я. Охрана труда на швейных предприятиях. – М.: Легпромбытиздат, 2007. – 256 с.
4. Доможиров Ю.А., Полухин В.П. Внутрипроцессный транспорт швейных предприятий. – М.: Легпромбытиздат, 2007. – 200 с.
5. Пристинский В. 100 знаменитых изобретений. – Ростов н/Д.: Феникс, 2009. – 510 с.
6. Беляева С.А., Парыгина М.М., Боброва Е.В., Петрова Е.М. Швейная промышленность в России // История науки и техники. 2010. – № 10. – С. 2–8.
7. Бабаджанов С.Г., Доможиров Ю.А. Экономика предприятий швейной промышленности.– М.: Академия, 2008. – 320 с.
8. Жуков Ю.В. Итоги работы лёгкой промышленности в 2006 г. // Швейная промышленность. – 2007. – № 2. – С. 2–12.
9. Зак И.С. Автоматизация процессов сборки швейных изделий. – М.: Лёгкая индустрия, 2009. – 208 с.
10. Эскин И.Ю. Выставка IMB-2006 (г. Кёльн, Германия) // Швейная промышленность. – 2006. – № 4. – С. 31–34.
11. Эскин И.Ю., Калмыкова Н.А. Оборудование полуавтоматического действия на IMB-2006 // Швейная промышленность. – 2007. – № 5. – С. 25–26.
12. Эскин И.Ю. Вспомогательная техника для заготовительных и монтажных участков швейного производства // Швейная промышленность. – 2008. – № 2. – С. 22–23.
13. Эскин И.Ю. Германия – Кёльн, IMB-2009 // Швейная промышленность. – 2009. – № 4. – С. 7–11.
22. Жуков Ю.В. Итоги работы лёгкой промышленности в 2008 г. // Швейная промышленность. – 2009. – № 2. – С. 3–6.
Швейное оборудование в зависимости от способа образования стежка подразделяется на машины челночного стежка и машины цепного стежка.
При челночном стежке механизм иглы сообщает игле, в ушко которой заправлена нитка, возвратно-поступательное и колебательное движение. Игла прокалывает ткань, проводя через нее верхнюю нитку. При обратном ходе иглы за счет трения нитки о ткань создается петля у ушка иглы. Механизм челнока обеспечивает захват петли, её обвод вокруг шпуледержателя. Механизм нитепритягивателя сматывает нитку с катушки, сдёргивает её с челнока и затягивает стежок. Для выполнения следующего стежка механизм двигателя ткани передвигает ткань на длину стежка. В электромеханических машинах все механизмы получают движение от главного вала, приводимого во вращение электрическим или механическим приводом. В компьютеризированных машинах продвижение иглы и ткани осуществляется отдельными электромагнитами, управляемыми с помощью процессора.
Цепной стежок образуется с помощью петлителя. В строчках цепного стежка переплетение нитей происходит на одной стороне сшиваемых материалов. Вид строчки на лицевой и нижней стороне различен. Цепной стежок бывает одно-, двух- и многониточным и допускает значительное удлинение вдоль строчки и поэтому обычно используется при сшивании эластичных (например, трикотажных) материалов. Главные недостатки цепного стежка - распускаемость и больший расход ниток, чем при использовании строчек из челночных стежков.
3.1. Бытовая швейная техника
Бытовая швейная техника предназначена для выполнения нерегулярных домашних швейных работ (подгонка готовых изделий, мелкий ремонт и т.п.), а также для регулярного домашнего пошива одежды на уровне хобби и любительского тканевого дизайна (пэчворк, квилтинг и т.п.). Такая техника имеет ограниченный эксплуатационный ресурс. При интенсивной эксплуатации бытовые машины быстро изнашиваются и очень часто не подлежат ремонту.
Многофункциональная и дорогая бытовая швейная техника относится к разряду «ремесленных» машин. Она широко используется для профессионального индивидуального пошива одежды на дому или в малых ателье (легкой, верхней одежды, женской, мужской одежды).
3.1.1. Механические швейные машины челночного стежка
Перемещение иглы и ткани выполняют механические детали (шестерни, рычаги и
пр.). Все управление (выбор типа строчки, длины и ширины стежка, регулировка
натяжения нити и т.п.) осуществляется при помощи механических переключателей и
регуляторов, находящихся на корпусе машины. Механические машины снабжаются
приводом от электромотора. В настоящее время выпускаются усовершенствованные
механические машины, которые могут выполнять в среднем от 7 до 25 операций, в
том числе:
- прямую строчку,
- краеобметочный шов для обработки среза ткани (в том числе швы зигзаг и
оверлочные швы),
- трикотажный (эластичный) шов,
- потайной шов, который применяется для обработки низа изделий,
- штопку тканей.
Некоторые механические машины могут выметывать простую бельевую петлю в автоматическом или полуавтоматическом режиме. Машины данного типа не могут выполнять строчки сложной формы.
3.1.2. Электромеханические (электронные) швейные машины челночного стежка
Основное устройство машин данного типа такое же, как и у механических машин,
но управление некоторыми функциями электронное, в том числе:
- электронное управление подъемом/опусканием иглы,
- электронный ограничитель скорости на корпусе машины,
- пуск и остановка машины без педали,
- отображение режимов работы машины на экране.
Количество выполняемых операций соответствует механическим машинам.
3.1.3. Процессорные (компьютерные) швейные машины челночного стежка
Движение иглы и транспортера подачи ткани осуществляют два электромагнита (шаговых двигателя), которыми управляет встроенный микропроцессор. Такой принцип управления не накладывает механических ограничений по сложности и количеству выполняемых операций. Шаговые двигатели по командам процессора выдают дозированный объем механического движения с оптимальным усилием непосредственно на рабочие устройства машины, что позволяет создать конструкцию с минимальным количеством движущихся механических частей.
Управление машиной производится в основном с помощью кнопок на передней панели, встречается и сенсорное управление. Информация о выбранной строчке и ее параметрах выводится на дисплей. Также на дисплей выводятся подсказки, такой режим работы называется «швейный советник».
Количество строчек в современных процессорных машинах может достигать
нескольких сотен. Все виды строчек заложены в память машины. На таких
устройствах можно выполнять следующие виды работ:
- различные виды петель по заданным размерам в автоматическом режиме;
- разнообразные строчки по трикотажу;
- большое количество декоративных швов;
- отделочные строчки с элементами вышивки, в том числе алфавит.
3.1.4. Компьютерные швейно-вышивальные машины челночного стежка
Для вышивки ткань закрепляется в пяльцах и передвигается в горизонтальной плоскости в любых направлениях. За вертикальное движение иглы и пялец в двух горизонтальных направлениях отвечает микропроцессор, поэтому можно запрограммировать движения для выполнения вышивки гладью, крестом, ришелье, обработку фестонов и мережки.
На таких машинах можно выполнять большое количество разнообразных вышивок, заложенных в память на заводе. Такие машины имеют возможность загружать вышивки извне, можно через специальное устройство подключить такую машинку к компьютеру. Имеются специальные программы для создания собственных рисунков. На таких машинах можно выполнить различные виды петель.
3.1.5. Бытовые оверлоки – машины цепного стежка
Оверлок это машина, предназначенная для обработки края (среза) ткани. Оверлок одновременно обрезает и сшивает ткань прочным эластичным швом. Оверлоки бывают 2-х, 3-х, 4-х и 5-и ниточные. До широкого распространений оверлоков обработка среза ткани выполнялась с помощью строчки «зигзаг», но такой шов получался неэластичным и непрочным. Оверлок позволит обработать ткани любой сложности: шелк, трикотаж, плотные ткани и пр. Такой вид строчки получается не за счет челнока, а с помощью петлителей, которые образуют сложную строчку. Особо стоит отметить такую функцию оверлока, как дифференциальную подачу ткани. Можно настроить оверлок так, чтобы ткань в ходе строчки растягивалась или припосаживалась. Благодаря этой функции упрощается работа с эластичными тканями. Оверлок не заменит швейную машину, а является дополнением к ней.
3.2. Термины швейной техники
Автостоп намотки шпульки – намотка ниток автоматически останавливается при полном заполнении шпульки.
Баланс петли – регулировка плотности левого и правого столбиков петли относительно друг друга.
Верхний и нижний транспортер подачи ткани
.
Верхний
транспортер расположен на механизме прижима ткани и передвигает ткань, зацепляя
ее сверху. Бывает встроенным (Фото 3-2-1 а) или докупается отдельно.
Используется для шитья тонких, ворсистых, эластичных, плотных тканей. Благодаря
верхнему транспортеру обеспечивается более равномерное продвижение слоев ткани
под лапкой.
Нижний транспортер расположен в рукаве машины и передвигвет ткань под лапкой,
зацепляя ее снизу (Фото 3-2-1 б). Нижний транспортер выполнен в виде зубчатых
реек, чем больше реек – тем более надежно выполняется продвижение. Во многих
машинах есть возможность отключения нижнего транспортера для выполнения штопки
или вышивки.
Дисплей – экран на корпусе машины. На дисплей выводится информация о выбранной строчке, ее параметрах, выводятся подсказки (швейный советник). Дисплеи бывают монохромные, цветные, сенсорные.
Дополнительный подъем лапки – позволяет приподнять лапку выше стандартной высоты. Применяется для шитья изделий из толстых тканей.
Игольная пластина – металлическая пластина, под которой находится челночное устройство. Для удобства шитья игольные пластины имеют разметку. На некоторых машинах игольная пластина может быть сменной. Стандартно для выполнения всех видов строчек применяется пластина с широким прямоугольным отверстием для прохода иглы в любом положении относительно центра строчки. Для выполнения прямой строчки применяется игольная пластина с маленьким круглым отверстием. За счет малого отверстия обеспечивается точное продвижение тонких и мягких тканей, без замятий и забивания ткани под лапку на рейки нижнего транспортера.
Коленный рычаг подъема лапки – подъем лапки осуществляется движением колена, руки освобождаются.
Машинные иглы.
Для выполнения машинных швов рекомендуется
применять качественные наборы игл известных производителей. В большинстве
моделей бытовых и ремесленных швейных машин применяются стандартные (universal -
универсальные) иглы. Фирменные иглы производятся из высококачественной
инструментальной стали. Фирма Мадейра впускает универсальную швейную иглу из
титанового сплава (номер 80/12, артикул № 9455T). Эта игла подходит для всех
видов ткани, она долговечна (Фото 3-2-2).
В некоторых моделях швейных машин, например в современных машинах фирмы Singer, используются только собственные иглы.
Европейская нумерация машинных игл от 65 до 130. Чем больше номер иглы, тем более толстые нитки можно использовать с этой иглой. Номер иглы означает максимальную ширину в миллиметрах нижнего участка иглы, где находится отверстие для нитки – «ушко», умноженную на 100. Например, игла номер 90 имеет ширину «ушка» 0,9 мм. Часто через дробь на иглах указывается американская система нумерации, например 100/16, 90/14, 80/12, 70/10.
Машинная игла подвергается интенсивному износу, поэтому рекомендуется периодически с помощью сильной лупы (8 крат и более) проверять качество кончика иглы. Затупленные иглы, иглы с зазубренным кончиком, а также иглы, имеющие загнутый кончик в форме миниатюрного крючка, необходимо заменить.
Нельзя пользоваться гнутыми иглами. Чтобы проверить машинную иглу, положите ее плоской стороной на ровную и гладкую плоскую поверхность (стекло). Зазор между иглой и плоской поверхностью должен быть везде одинаковым (Рис. 3-2).
Нитевдеватель – устройство для быстрой заправки нитки в игольное ушко. Бывают автоматические и ручные.
Нитеобрезатель – устройство для быстрой обрезки нитей. Располагается на корпусе машины или на задней поверхности игольного штока.
Освещение – встроенная лампа, освещающая рабочую область. Освещение есть во всех современных машинах.
Память – флэш-память, встроенная в машину. Применяется в процессорных, вышивальных и швейно-вышивальных машинах. В основную память машины загружаются строчки, мотивы вышивок и подсказки. Также бывает память доступная для пользователя, в которую загружаются собственные образцы вышивки или строчки.
Педаль – электронно-механическое устройство для регулировки скорости работы двигателя машины. Обороты двигателя зависят от степени нажатия ноги на педаль.
Петля – автоматические и полуавтоматические выполнение петель. При автоматическом выполнении машина выметывает петлю в один прием, размер петли определяется по пуговице или задается через меню. При полуавтоматическом выполнении машина выметывает петлю в четыре приема.
Позиционирование иглы – функция, которая позволяет опускать/поднимать иглу нажатием специальной кнопки на панели машины. При выполнении этой функции машина запоминает, в каком положение оставлять иглу после завершения строчки.
Положение катушки с нитками – вертикальное или горизонтальное. При вертикальном положении катушка надевается на выдвижной штырь. При горизонтальном положении катушка закрепляется в специальном отсеке машины в горизонтальном положении, считается, что горизонтальное положение обеспечивает лучшее сматывание нити.
Реверс – обратный ход продвижения ткани. Применяется для того, чтобы сделать закрепку (закрепить нити не завязывая узлов вручную). Обратный ход не означает, что мотор и маховик машины вращаются в обратном направлении.
Регулировка давления лапки на ткань – функция полезна при шитье толстых тканей, на которых ее можно ослабить, и тонких, на которых ее можно усилить.
Регулировка натяжения верхней и нижней нитей – позволяет оптимально подобрать натяжение нитей в зависимости от толщины нити и ткани для получения красивой и прочной строчки.
Регулировка скорости – ограничение скорости работы в процессорных, вышивальных и швейно-вышивальных машинах. Полезное свойство машины для начинающих.
Рукавная консоль – или «свободный рукав». Образуется путем снятия с машины детали, расширяющей поверхность рабочей плоскости, благодаря чему станина машины в области иглы-челнока становится узкой. Полезное приспособление при шитье узких цилиндрических деталей (рукава, манжеты и пр.). Присутствует практически во всех современных машинах.
Челнок вертикальный качающийся – применяется в простых и дешевых машинах. Отличительными особенностями таких челноков являются надежность, возможность регулировать натяжение нижней нити, невысокая стоимость. Недостатки – высокий уровень вибраций и невысокая скорость работы (Фото 3-2-3).
Челнок вертикальный двойного обегания (ротационный) – используется в конструкциях дорогостоящих швейных. Современные профессиональные швейные машины оснащены челноками именно такого типа. Челноки данного типа отличаются надежностью, высокой скоростью работы, удобством настройки и они практически не подвержены вибрации.
Челнок горизонтальный двойного обегания – широко применяется в процессорных швейных машинах, ориентированных на выполнение простых швейных операций в лоскутной технике (Фото 3-2-4). Челнок расположен горизонтально, обладает рядом достоинств: удобен и прост в заправке, не вибрирует (так как не качается, а вращается), не требует смазки, скорость работы выше, чем у вертикального челнока. Количество ниток в челноке видно через прозрачную пластину. Такой челнок требует применения высококачественных фирменных ниток. К недостаткам горизонтального челнока можно отнести неудобную регулировку натяжения нижней нити - для того, чтобы добраться до регулировочного винта, нужно снять игольную пластину.
Швейный советник – применяется в процессорных машинах. Все операции на машине сопровождается подсказками, которые выводятся на экран. Функция может быть полезна только при освоении машины.
Электронный стабилизатор силы прокола ткани – применяется в дорогих процессорных машинах, независимо от оборотов двигателя автоматически выбирается пробивное усилие иглы, что позволяет работать с плотными тканями.
Электропривод – электродвигатель, приводящий в движение механизм машины. Включение двигателя и изменение скорости его работы производится путем нажатия на педаль.
3.3. Общие правила безопасной работы на швейной машине
Прежде чем приступить к работе на швейной машине, необходимо внимательно изучить руководство к ней. Необходимо изучить заправку и регулировку натяжение нитей, чистку и смазку машины.
3.3.1. Санитарно-гигиенические правила и правила техники безопасности
При работе на швейной машине:
- свет должен падать на рабочую поверхность с левой стороны или спереди,
- сидеть за машиной надо прямо, на всей поверхности стула, слегка наклонив
корпус и голову вперед,
- стул должен стоять против иглы, расстояние между работающим и столом машины
должно быть 10÷15 см,
- изделие должно находиться на расстоянии 30÷40 см от глаз работающего,
- на машине не должны лежать посторонние предметы,
- не следует наклоняться близко к движущимся и вращающимся частям машины,
- заправляя нитку в машинную иглу, не держать ноги на педали,
- перед работой проверить, не остались ли в стачиваемых деталях булавки и иглы.
3.3.2. Правила начала и окончания строчки на швейной машине
а) подготовка машины к строчке:
- поставить машину на рабочий ход,
- поднять иглу в верхнее положение,
- вынуть из-под лапки кусочек ткани,
- заправить верхнюю и нижнюю нитки.
б) начало строчки:
- подложить подготовленную для работы ткань под лапку и проколоть ее иглой,
придерживая концы ниток,
- затем опустить лапку и приступить к работе.
в) окончание строчки:
- поднять иглу и лапку,
- затем отвести ткань от себя левой рукой,
- обрезать нитки, оставляя концы длиной 10÷15 см,
- подложить кусочек ткани под лапку, опустить лапку,
- опустить иглу.
Если намечается длительный перерыв в работе, то поставить машину на холостой
ход, а на машине с ножным приводом снять приводной ремень, чтобы он не
растягивался.
Прокладка из ткани между подающей рейкой и лапкой предохраняет острые грани
рейки подающего механизма от затупления при контакте с металлом лапки. А также
предохраняет подошву лапки от деформации при длительном контакте с металлом
подающей рейки.
Опускание лапки предохраняет прижимную пружину лапки от излишнего напряжения
(сжатия) в нерабочем состоянии машины.
Опускание иглы предохраняет ее от поломки, а швею от травм.
Перевод на холостой ход предохраняет машину от поломки, а швею от травм при
случайном включении мотора или повороте махового колеса машины.
3.3.3. Общие правила работы за машиной
Маховик машины должен вращаться только в одном направлении – «на себя». Нельзя вращать маховик в противоположном направлении (от себя), так как неправильное вращение может вызвать запутывание ниток в челночном устройстве и обрыв нити. На некоторых машинах имеется реверс движения ткани для закрепления шва, но при этом маховик всегда вращается «на себя».
Не пускать машину в ход без подложенной под лапку ткани, чтобы не притупились зубцы подающего механизма, и не портилась нижняя опорная поверхность нажимной лапки.
Нельзя тянуть или подтягивать ткань руками во время шитья, может сломаться игла. Необходимая подача ткани производиться самой машиной.
При намотке ниток на шпульку механизм машины должен быть отключен.
3.3.4. Уход за машиной
После окончания рабочего дня машину необходимо почистить.
После окончания пошива одного изделия машину почистить, затем смазать. В инструкциях к машине указаны все точки смазки. Если инструкции нет, то необходимо смазывать все места, где есть движение металла по металлу. После смазки машину оставить в рабочем положении (не складывать) на 8÷10 часов, чтобы излишнее количество масла стекло вниз. Излишки масла убрать мягкой бумажной салфеткой.
Для смазки необходимо использовать масло отечественное индустриальное (машинное) марок И8-А, И20-А или импортное масло от известных производителей швейных машин. Для бытовых швейных машин нельзя применять автомобильные масла, а также масло для промышленного оборудования (например, веретенное масло). Следует учитывать, что машинное масло имеет ограниченный срок годности (6÷12 месяцев). Масло со временем окисляется и густеет, при этом теряет свои эксплуатационные свойства.
3.4. Неполадки в работе машины, причины их возникновения
Способы устранения мелких неполадок изложены на примере машины с вертикальным челночным устройством.
Получение хорошей строчки зависит:
- от правильного выбора толщины ниток и иглы (см. Таблицу 1),
- от правильного натяжения ниток в машине,
- от правильного выбора длины стежка.
Очень важно отрегулировать натяжение верхней и нижней нитей. Верхняя нить идет с катушки, а нижняя из челночного устройства. Верхняя и нижняя нитки должны быть либо с одной катушки, либо с разных, но при этом нижняя нитка должна быть тоньше верхней. Когда натяжение нитей отрегулировано правильно, они переплетаются внутри сшиваемых тканей, на верхней поверхности ткани не видно нижней нитки, а на обратной поверхности ткани не видно верхней нитки (Рис.3-4 а).
3.4.1. Нить петляет
Машина делает петли с нижней стороны сшиваемых тканей, если нижняя нить сильно натянута или верхняя сильно ослаблена по отношению к нижней (Рис.3-4 б).
Машина делает петли с верхней стороны сшиваемых тканей, если верхняя нить сильно натянута по отношению к нижней нити или нижняя нить натянута слишком слабо (Рис.3-4 в).
Прежде всего, проверить натяжение нити в челноке: шпульный колпачок вместе со шпулькой подвесить за нить и подергивать. Если колпачок при легком подергивании соскользнет и остановится, то натяжение нормальное, если скользит без остановки - слабое, если не скользит совсем - сильное.
Регулировка натяжения нижней нити производится посредством винта на шпульном колпачке.
Изменение натяжения верхней нити производится посредством регулятора натяжения верхней нити.
3.4.2. Слабая строчка
Видны нитки между сшитыми полотнищами ткани при оттягивании одного полотнища от другого. В этом случае усиливается натяжение обеих нитей (верхней и нижней) и доводится до нормального. Сначала усиливают натяжение нижней нити, а затем постепенно увеличивают натяжение верхней нити.
3.4.3. Тугая строчка
Тонкая мягкая ткань стягивается, сосбаривается, а на толстой плотной ткани строчка получается непрочной, т.е. при небольшом растягивании ткани вдоль строчки нитки рвутся.
Сначала ослабить нижнюю нить, затем подрегулировать натяжение верхней нити.
3.4.4. Пропуск стежков
Основные причины:
- кривая или тупая игла,
- игла, не соответствующая нитке по толщине,
- неправильная установка иглы по высоте,
- неправильная установка иглы по расположению ее желобков,
- плохое качество ниток, то есть в машину заправлены старые залежалые
хлопчатобумажные нитки, нитки с узелками, армированные нитки с отстающей
оплеткой, а также нитки, не соответствующие виду машинных работ (нитки для
наметки, нитки для ручной вышивки).
Пропуск стежков может быть вызван нарушением взаимодействия двигателя ткани и иглы, повышенным износом деталей механизма и другими причинами, которые может устранить механик по швейным машинам.
3.4.5. Обрыв верхней нити
Обрыв верхней нити может произойти по разным причинам. Искать причину надо с начала заправки, т.е. с катушки. Проверяется качество деталей и узлов, через которые проходит нить. Заусенцы, шероховатости, острые края деталей могут вызвать обрыв нити.
В регуляторе натяжения верхней нити обрыв может быть из-за накопившихся волокон и грязи между зажимными шайбами. Регулятор можно почистить без разборки, при поднятой лапке вставить между прижимными шайбами кусочек ткани и двумя руками продвигать ее между шайбами влево-вправо.
Игла может вызвать обрыв нити, если она неправильно вставлена (не в ту сторону желобком), а также, если ее желобок или ушко имеют острые края (заусенцы).
Обрыв нити может произойти и от поворота махового колеса в обратную сторону во время работы машины.
Причинами обрыва нити также могут быть:
- застрявшая нить в челноке,
- нарушение взаимодействия рабочих органов машины при несвоевременном
продвижении ткани,
- неправильная сборка челночного комплекта,
- большое загрязнение челночного комплекта,
- сильный износ челночного комплекта,
- плохое качество ниток или применение ниток, не соответствующих виду машинных
работ (нитки для наметки, нитки для ручной вышивки).
3.4.6. Обрыв нижней нити
Нижняя нить от шпульки проходит по шпульному колпачку (между колпачком и пружиной натяжения) и через игольный глазок игольной пластины.
Причины обрыва ищут с момента намотки нитки на шпульку. Проверяют качество намотки, качество самой шпульки и правильность ее вставки в шпульный колпачок. Если нитка на шпульку намотана с петлями или неравномерно, то петли мешают нормальному сматыванию нитки со шпульки, они скручиваются и дают обрыв нижней нити.
Если ниток на шпульке намотано много, то она с нажимом вставляется в шпульный колпачок и там не вращается. Чтобы предотвратить обрыв нижней нитки, излишние нитки надо смотать.
Более частой причиной обрыва нижней нити является ее чрезмерное натяжение и неправильная заправка нити.
Обрыв нижней нити может произойти и из-за плохого качества деталей, через которые она проходит, но, проверяя детали, одновременно следует проверить качество ниток (узелки могут застрять в прорези), а также проверить, не сечется ли нитка об острые края шпульки.
3.4.7. Поломка иглы
Причинами поломки иглу могут быть:
- игла неправильно вставлена по высоте или направлению желобков игле,
- игла кривая,
- игла не соответствует толщине ниток и ткани,
- игла слабо закреплена в иглодержателе,
- удар иглы по неправильно установленной или слабо закрепленной лапке,
- удар иглы по игольной пластине в случае плохого закрепления пластины или при
выполнении швов с отклонением иглы с игольной пластиной для прямой строчки,
- неправильно вставлен шпульный колпачок,
- слишком толстая ткань,
- сильное натягивание ткани руками во время ее продвижения под лапкой.
3.5. Регулировка натяжения нитей
на примере машины с вертикальным челночным устройством)
Прежде всего, проверить натяжение нити в челноке (Фото 3-5): шпульный колпачок вместе со шпулькой подвесить за нить и подергивать вверх. Если колпачок при легком подергивании не скользит совсем (1), то натяжение сильное, если скользит без остановки (2) – слабое, если скользнет и остановится, то натяжение нормальное (3).
3.5.1. Регулировка натяжения нижней нити
Регулировка производится посредством винта на шпульном колпачке (Фото 3-5-1).
Следует использовать отвертку с узким и тонким лезвием. Вращение по часовой стрелке усиливает натяжение нити, против часовой стрелки – ослабляет. Будьте осторожны, винт маленький и короткий, при отворачивании его до конца упругая пластинка, которую он прижимает, с силой вытолкнет его, винт выскочит и может потеряться. Для поиска винта применяйте магнит.
3.5.2. Регулировка натяжение верхней нити
Регулировка производится с помощью регулятора натяжения верхней нити. Поворот ручки регулятора по часовой стрелке усиливает натяжение нити, против часовой стрелки – ослабляет.
Устройство регулятора одинаково практически на всех машинах. Верхняя нить проходит между двумя зажимными шайбами, степень натяжения верхней нити зависит от силы сдавливания шайб, а также от толщины, вида волокна и структуры (крутки) нити. При поднятой лапке зажимные шайбы разводятся, и нить не задерживается.
Перед регулировкой необходимо почистить регулятор натяжения верхней нити, так как в нем остаются волокна нитей, они спрессовываются и не дают зажимным шайбам плотно сойтись для удержания нити. При поднятой лапке полоской мягкой ткани прочистить регулятор натяжения верхней нити между двумя зажимными шайбами.
3.6. Как научиться ровно строчить
Начинающим не всегда удается получить ровную строчку на швейной машине.
1. Для начала нужно проверить качество работы подающего механизма машины:
- заправить нитки, установить режим прямой строчки и минимальную скорость хода
машины,
- положить под лапку кусочек ткани длиной 15,0 х 15,0 см,
- выполнить строчку до конца кусочка ткани, не дотрагиваясь до ткани руками и не
изменяя скорость хода машины,
- уложить вдоль строчки линейку и проверить прямолинейность строчки.
Хорошо налаженная машина должна на таком кусочке ткани по всей длине шва выполнить прямую строчку без помощи рук. Отклонение от прямой линии не должно превышать 0,1 см. Такое отклонение при работе можно скомпенсировать, направляя руками ткань под иглу.
Если отклонение больше, то возможны следующие неисправности механизма подачи
ткани:
- заводской дефект подающей зубчатой рейки (называемой также гребенкой),
- дефект монтажа подающей рейки (заводской или в ходе ремонта),
- затупление зубьев подающей рейки,
- заводской дефект держателя лапки,
- заводской дефект лапки в месте ее крепления к держателю лапки,
- заводской дефект подошвы лапки.
Машину следует отремонтировать.
Возможна неправильная установка лапки при замене (прекос, недостаточное закрепление).
2. Руки швеи нужны только для направления ткани по линии шва и подачи
длинного участка ткани на платформу машины. Правильно действовать так:
- точно установить иглу в начале строчки, выполнить закрепку шва,
- пальцы правой руки положить на ткань справа от лапки, пальцы левой руки
положить на ткань слева перед лапкой,
- пальцами на ткань не нажимать, не тормозить и не тянуть ткань, а только слегка
придерживать с равным усилием правой и левой руки (Фото 3-6-1).
3. Как начать строчку:
- опустить иглу в ткань на расстоянии 1,0÷1,5 см от среза ткани (начала шва),
- опустить лапку,
- установить режим закрепления строчки, прострочить назад почти до среза ткани
(начала шва),
- отключить режим закрепления строчки, строчить вперед.
Как обеспечить ровность строчки:
- направлять руками ткань так, чтобы игла шла по меловой линии шва или рядом со
стежками ручной наметки (по стежкам не строчить, иначе наметку будет трудно
удалить),
- если нет меловой линии или наметки на ткани, то направлять ткань по
контрольным линиям, выгравированным на игольной пластине, или использовать
направитель ткани (Фото 3-6-2).
Фото 3-6-1 Фото 3-6-2
5. Как закончить строчку:
- не доводить строчку до среза ткани (конца шва) на 0,2 см,
- установить режим закрепления строчки, прострочить назад 0,5 см,
- поднять иглу из ткани, поднять лапку,
- отодвинуть ткань назад и влево от иглы,
- обрезать концы ниток.
6. Тренировка для закрепления навыков:
- для тренировки возьмите ненужную ткань,
- начертите на ней с помощью линейки тонко отточенным карандашом параллельные
линии,
- строчите несколько метров, пока строчки не будут ровными.
2. В чем отличие буквенно-цифровой классификации от буквенноцифрового кодирования характеристик швейных машин?
3. Какие основные части швейной машины вы знаете?
4. Перечислите основные причины и неполадки в работе машины
11. Швейные машины челночного стежка
Машины челночного стежка наиболее широко используются в производстве швейных изделий и предназначены для пошива изделий однолинейной строчкой двухниточного челночного стежка. Это наиболее распространенный тип швейных машин не только в промышленности, на малых предприятиях, но и в быту.
Для обеспечения отдельных операций и сокращения ручных операций (сметывание, обрезка края, разутюживание шва и т.д.) разработаны машины челночного стежка специального назначения, которые имеют дополнительные механизмы и некоторые изменения конструкции механизмов и корпусных деталей машины.
Во всех машинах челночного стежка сохранены общие принципы и последовательность образования стежка, что упрощает их изучение. Различия в работе и конструкции машин касаются функционирования дополнительных механизмов и их конструкции.
Процессы петлеобразования (таблица 3).
Нитевая строчка складывается из множества отдельных стежков. Для образования челночного стежка используют две нитки - верхнюю и нижнюю. Игла с верхней ниткой перемещается вниз-вверх, а челнок с намотанной на шпульку нижней колеблется или вращается под игольной пластиной, на которой лежит ткань. При движении вниз игла прокалывает ткань и протягивает через нее верхнюю нитку, создавая с изнаночной стороны петлю. Челнок захватывает эту петлю и обводит вокруг шпуледержателя и шпульки, переплетая обе нитки. Затем нитепритягиватель сматывает верхнюю нитку с катушки, сдергивает петлю со шпульки и затягивает стежок, после чего транспортер перемещает ткань на длину стежка. Работа всех механизмов согласуется с помощью главного вращающегося вала.
Швейная машина класса 97-А с горизонтальной осью челнока
Швейная машина класса 97-А предназначена для стачивания двухниточной челночной строчкой легких и средних тканей. Основными отличительными признаками машины являются: наличие вращающегося (фасонного) нитепритягивателя, высокая производительность и автоматическая система смазывания. Машина предназначена для изготовления комплектов постельного белья, белья, сорочек, костюмов и женского платья.
Таблица 3
Окончание таблицы 3
Максимальная толщина обрабатываемого
Рис. 21 Схема заправки игольной нитки.
Заправка ниток. Бобина 1 (рисунок 21,а) с игольной ниткой надевается на стержень 2 стойки 5 и устанавливается вертикально на подставку 6. Далее нить продевается через втулку 3 планки 4 стойки 5. Втулка 3 должна располагаться строго на вертикали, проведенной через центр оси стержня 2. При этом расстояние Я от подставки б до втулки 3 должно быть таковым, чтобы по возможности уменьшить боковое касание нити при ее сходе с бобины. Ограничением в установке расстояния является недопустимость касания головкой машины подставки 6 при ее опрокидывании. Далее заправку игольной нитки выпол-
няют последовательно, проводя ее через отверстия нитенаправителей 7 (рисунок 21, б) и 8 на рукаве машины. Нитку пропускают через щель 9 на фронтальной доске машины. Выводят нитку из щели 9 через отверстие 16 фронтальной доски, обводят между шайбами 75 регулятора натя жения, заводят за крючок компенсационной пружины и обводят снизу вверх нитенаправительный уголок 14. Затем игольную нитку вводят в щель между фронтальной доской и кольцом 10 и набрасывают на кулачковую поверхность нитепритягивателя 11, выводят из-под кольца 10 и заправляют в нитенаправитель 12, закрепленный на фронтальной доске, и в проволочный нитенаправитель на игловодители, вводят в
ушко иглы 13. При заправке нитки оставляют свободный конец нитки длиной 70 ...80 мм, который используют для вытягивания челночной нитки из-под игольной пластины.
Заправка челночной нитки (рисунок 22).
Рис. 22. Схема последовательной перезаправки челночной нитки.
При заправке челночной нитки, намотанной на шпульку, берут шпульку 1 пальцами правой руки и надевают на осевой стержень 2 шпульного колпачка 3, который удерживают в левой руке. Конец нитки проводят по прорези 4 шпульного колпачка, подводят под пластинчатую пружину 5 и заводят за ее язычок 6. Задвижную пластину 8 на платформе машины выдвигают влево и, поворачивая шкив машины, поднимают иглу в крайнее верхнее положение. Поднимают прижимную лапку над игольной пластиной. Пальцами левой руки удерживают за пластину 7 защелки шпульный колпачок с челночной ниткой и вставляют в осевой стержень 9 шпуледержателя 10 пустотелый осевой стер-
жень 2 шпульного колпачка 3. При этом вырез на шпульном кол пачке должен быть обращен вверх. После установки шпульного колпачка 3 в шпуледержатель 10 проверяют попадание выступа 11 на пластине 7 защелки в боковой вырез на фронтальной части шпуледержателя 10 и срабатывание, т. е. фиксацию шпульного колпачка 3 пластиной 7 на стержне 9. Поворотом шкива, удерживая игольную нитку и натягивая ее при выходе иглы из-под игольной пластины, вытягивают обе нитки и направляют их под лапку от оператора.
Натяжение челночной нитки регулируют поворотом винта прижатия пластинчатой пружины 5, игольной нитки - поворотом гайки в регуляторе натяжения.
Устройство и работа моталки. Для намотки нитки на шпульку в машине используют моталку, устанавливаемую на поверхности стола справа от головки машины.
Рис.23. Моталка челночной нитки на шпульку к швейной машине
Моталка имеет пластину 6 (рисунок 23), на конце которой винтом крепится скоба 8. В вертикальной части пластины запрессован регулятор натяжения нитки 9, а в верхней части скобы имеется нитенаправительное отверстие 10. В передней части пластины 6 в двух ее стойках 13 удерживается рычаг 14, снизу в его отверстие вставлена пружина, которая, надавливая на упор, стремится повернуть рычаг 14 против часовой стрелки. В верхней части рычага 14 имеется отверстие, в котором располагается вал 4, имеющий правый конец с разрезом для более плотной установки на нем шпульки 5. На левом конце вала 4 закреплен шкив 3. С рычагом 14 соединено звено 2, к его приливу винтом 16 прикрепляется пластинчатая пружина 12, служащая для отключения моталки при наматывании требуемого количества нитки на шпульку 5. Вторая часть звена 2 соединена с рычагом 17 включения автоматического устройства для наматывания ниток, при этом нижний конец рычага 17 соединен со стойкой пластины 6 шарнирной заклепкой. Для бесшумного отключения моталки и ее Торможения на пластине 6 закреплен держатель 1 с резиновой прокладкой 18.
Моталка закрепляется на столе через продольные отверстия в пластине 6 двумя шурупами 11.
Для намотки нитки на шпульку нитку от бобины на стойке проводят через отверстие 10 между шайбами регулятора натяжения 9 и совершают 3...4 витка на шпульке 5, предварительно установленной на валу 4. Моталку включают, повернув рычаг 17 по часовой стрелке, что соответствует выходу рычага 17 и звена 2 на одну прямую линию. При этом шкив 3 смещается к ремню привода швейной машины. При изменении положения звена 2 его пластинчатая пружина 12 входит между стенками шпульки 5. Когда же на шпульку 5 наматывается заданное количество нитки, наполненная шпулька давит на пластинчатую пружину 12, и под действием пружины в рычаге 14 звено 2 и рычаг 17 выводятся из выпрямленного состояния. Рычаг 14 поворачивается против часовой стрелки, шкив 3 отходит от ремня и соприкасается с тормозной резинкой 18, которая останавливает его инерционное вращение. Шпулька 5 снимается с вала 4, нитка отрезается. Недопустимо попадание оставшегося свободного конца нитки на ремень привода машины, поскольку она может намотаться на шкив машины.
Степень наполнения нитками шпульки регулируется винтом 15, что изменяет положение пластинчатой пружины 12 относительно оси шпульки 5. При закручивании винта 15 выступающая часть пружины 12 опускается и на шпульку 5 наматывается больше ниток.
Для равномерного наматывания нитки на шпульку 5 необходимо отрегулировать положение нитенаправителя 10 относительно шпульки 5. Для этого освобождают винт 7 и смещают скобу 8 поперек пластины d таким образом, чтобы нитка равномерно наматывалась по всей ширине шпульки 5.
Равномерное вращение шкива 3 можно отрегулировать перемещением пластины 6 с моталкой после ослабления крепления шкива шурупами 11 к ремню привода машины. Между шкивом 3 и ремнем должен быть плотный контакт, исключающий свободное проскальзывание ремня относительно шкива 3 при намотке нитки на шпульку 5.
Отключение моталки и ее останов можно отрегулировать, смещая моталку от ремня после ослабления ее крепления шурупами 11, а также регулированием положения резиновая прокладка 18 после ослабления крепления державки 1. Резиновая прокладка 18 должна контактировать со шкивом 3 при его отключении, что предотвращает переполнение нитками шпульки 5 в результате инерционного вращения шкива 3.
Механизм нитепритягивателя.
В машине 97-А применяется фасонный вращающийся тип механизма нитепритягивателя (рисунок 24).
Нитепритягиватель 1 по отверстию 2 надевается на ось 3 пальца 5 кривошипа 4 и через сектор 6 винтами 7 прикрепляется к приливу пальца 5. К фронтальной доске рукава машины винтом и гайкой закрепляется нож для обрезки нитки в случае ее обрыва и устранения ее наматывания на профиль 8 нитепритягивателя 1.
Рис. 24. Нитепритягиватель ротационного типа
В механизме регулируется своевременность затягивания нитки в стежке поворотом нитепритягивателя 1 после ослабления винтов 7. При повороте нитепритягивателя 1 против часовой стрелки стежок затягивается раньше. Запаздывание затягивания стежка может привести к повторному захвату сброшенного с пальца накладного полукольца-скобы челночного устройства игольной петли.
Центрально-шпульный равномерно вращающийся тип механизма челнока (рисунок 25).
Рис.25. Челнок к швейной машине класса 97-А
На главном валу б двумя винтами крепится зубчатый барабан 7 (рисунок 25, а). На нижнем распределительном валу 9 закрепляется нижний зубчатый барабан 8. На оба барабана надевается зубчатый ремень 5. Для устранения осевого смещения ремня на барабаны надеты также пружинные кольца. Распределительный вал 9 вращается в шарикоподшипнике и двух втулках. На его левом конце двумя винтами закреплена шестерня 10 с внутренним расположением зубьев. Шестерня 10 входит в зацепление с малой шестерней 4 и образует зубчатую передачу с передаточным отношением 1:2. Шестерня 4 имеет единое исполнение с челночным валом 3. Челночный вал 3 вращается в двух втулках, запрессованных во втулку 11 (рисунок 25, б), закрепленную винтом в платформе машины. На левый конец вала 3 устанавливается челночное устройство 1 и закрепляется двумя винтами 2.
Челнок 1 через зубчато-ременную и зубчатую передачи получает вращение в том же направлении, что и шкив машины, но за один оборот главного вала он совершает два оборота.
Своевременность подхода носика челнока / к игле регулируется его поворотом после ослабления винтов 2. При подъеме иглы из крайнего нижнего положения на расстояние S = 1,9...2,1 мм носик челнока должен выйти на траекторию движения иглы.
Зазор Д между носиком челнока 1 и иглой регулируется после ослабления винта крепления втулки 11 и осевым смещением втулки 11 совместно с челночным устройством 1. Зазор Д = 0,05... 0,1 мм.
Количество масла, поступающего к челночному устройству, регулируется винтом 12. При вывертывании винта 12 подача масла к челноку возрастает. Проверку подачи смазочного материала челноку следует проводить при максимальном числе оборотов главного вала, для чего необходимо подставить под челнок лист бумаги и подержать его неподвижно 15 с. Если на бумаге останутся две рассеянные масляные полоски шириной приблизительно 1 мм, то подача масла к челноку нормальная.
Конструкция челночного устройства рассмотрена в п. 3.2.
В машине используется реечного типа механизм двигателя ткани, состоящий из узлов подъема прижимной лапки, продвижения, регулирования и обратного хода зубчатой рейки.
Узел подъема рейки (см. рисунок 26). На нижнем распределительном валу 26 закрепляется двумя винтами эксцентрик подъема 34, и на него надевается головка шатуна 33. Между шатуном 33 и эксцентриком вставлен игольчатый подшипник. Вторая головка шатуна 33 через шарнирный винт 30 с помощью гайки 32 соединена с коромыслом 31, закрепленным на валу подъема 43 стягивающим винтом 29. Вал 4? центрируется шпильками 27 и 45, закрепленными винтами 28"и 44в корпусе машины. На переднем конце вала 43 имеется рычаг 42 подъема. Палец, закрепленный в рычаге 42, входит в осевое отверстие ползуна 41, который находится в направляющих рычага-вилки 47. На рычаге-вилке закреплена рейка 46.
Вращение эксцентрика 34 вызывает колебательные движения шатуна 33 и с помощью коромысла 31, вала 43 и рычага 42 с ползуном 41 перемещает рейку 46 в вертикальной плоскости.
Рис.26. Кинематическая схема механизма перемещения рейки
Узел продвижения рейки по горизонтали. На распределительном валу 26 эксцентрик продвижения 36 выполнен единой деталью с эксцентриком подъема 34. На эксцентрик продвижения 36 надета головка шатуна-вилки 37. Между шатуном 37 и эксцентриком 36 вложен игольчатый подшипник. В заднюю головку, выполненную в виде вилки, вставлена ось 16, которая образует также шарнирное соединение с раздвоенной головкой соединительного звена 13 и жестко, с помощью винта 15, соединена с коромыслом 38. Нижняя головка коромысла 38 продета через ось 39, передняя часть которой надета на нижнюю головку коромысла 40, а удаленный конец ее жестко, с помощью винта, соединен с рычагом 35. Верхняя головка коромысла 40 шарнирно соединена через шпильку 48 с корпусом машины. Шпилька 48 закрепляется винтом в платформе машины. Верхняя головка рычага 35 винтом 7 7 закрепляется на промежуточном валу 18 узла регулировки длины стежка.
Соединительное звено 13 дальней головкой шарнирно, через винт 11, связано с коромыслом 10, которое стягивающим винтом 9 закреплено на валу продвижения 8. Вал продвижения 8 удерживается с помощью двух шпилек 72 и 2 в корпусе машины. Шпильки 12 и 2 закреплены соответственно винтами 14 и 1 в платформе машины. На переднем конце вала 8 имеется вертикальная рамка 7, в
которой с помощью шпилек 6 и 3 центрируется рычаг-вилка 47. Шпильки 6 и 3 в рамке 7 закрепляются винтами 5 и 4.
Вращение эксцентрика 36 вызывает колебательные движения шатунавилки 37, которые преобразуются с помощью коромысла 38 в возвратноповоротные движения оси 16. При выполнении строчки со стабильной длиной стежка ось 39 качания коромысла 38 неподвижна. От оси 16 колебательные движения сообщаются коромыслу 10 через соединительное звено-вилку 13. Коромысло 10, закрепленное на валу продвижения 8, и рамка 7 совершают воз- вратно-поворотные движения, которые перемещают рейку 46 в горизонтальном направлении.
Узел регулирования длины стежка и выполнения закрепки (обратного хода рейки). Для регулирования длины стежка и выполнения обратного хода рейки (это позволяет выполнять закрепку на строчке) в машине 97-А промежуточный вал 18 через рычаг 25 и тягу 21 соединен с двуплечим рычагом 22. На выходящем из корпуса его конце закреплена рукоятка 24. Для возврата рукоятки 24 в крайнее верхнее положение после выполнения закрепки в строчке на промежуточном валу 18 закреплено с помощью винтов установочное кольцо 20. В отверстие установочного кольца 20 вставлен один конец пружины 19, а другой конец упирается в платформу машины.
Изменения расстояния транспортирования материала (регулировка длины стежка) выполняются сменой положения оси 39. Чем больше ось отходит от плоскости, проведенной через ось 16 и шарнирный винт 11 в среднем положении рейки 46, тем больше длина стежка. При выходе оси 39 на эту плоскость длина стежка равна нулю, а при дальнейшем движении против часовой стрелки движение рейки преобразуется в обратное. Положение рычага 22 фиксируется гайкой 23.
Узел прижимной лапки. Шарнирная лапка 1 (см. рисунок 27) винтом 2 прикрепляется к стержню 22, перемещающемуся во втулке 21, которая запрессована в рукаве машины. На верхнем конце втулки 21 располагается кронштейн 20, его плоский выступ входит в вертикальную прорезь 4 рукава. На стержне 22 винтом 18 закреплена муфта 77, к которой прикреплен толкатель для освобождения нитки при поднятии лапки. Плоский выступ на муфте 77также вставлен в вертикальную прорезь 4 рукава. Выступ на муфте 17 не позволяет прижимной лапке 1 разворачиваться вокруг оси стержня 22. Сверху в стержень 22 вложен шарик 16, на который давит пластинчатая пружина 75, надетая правым концом на винт 14. На пружину 75 сверху действует регулировочный винт 9. Снизу на выступ кронштейна 20 может воздействовать кулачок 3, жестко запрессованный на горизонтальной оси 19. На правом конце оси 19 закрепляется рычаг 23 для ручного подъема прижимной лапки 7. При повороте кулачка 3 он через толкатель (на рисунок 27 не показан) и стержень отжимает пластину регулятора натяжения и освобождает игольную нитку.
Для коленного подъема лапки к кронштейну 20 присоединена шарнирным винтом нижняя головка звена 5. Верхняя головка звена 5 надета на стержень 6, который приварен к рычагам 7 (11) и 11. Рычаг 7(77) удерживается на
шарнирных винтах 8 и 10. В правый выступ рычага 77 вставлен верхний конец тяги 13 и зафиксирован разводным штифтом 12. Нижний конец тяги 13 проходит через отверстие в платформе машин, снизу на тягу надеты пружина 24 и шайба 25. Шайба 25 также зафиксирована разводным штифтом.
Рис.27. Кинематическая схема узла подъема прижимной лапки.
При нажатии на рычаг для коленного подъема лапки тяга 13, поднимаясь, поворачивает рычаг 77 против часовой стрелки и через звено 5, кронштейн 20 и муфту 77 поднимает стержень 22, а вместе с ним и прижимную лапку 7.
Длина стежка в машине 97-А регулируется поворотом рифленой гайки 23 (см. рисунок 26), расположенной в рукоятке 24регулятора. При закручивании гайки 23 рукоятка смещается вниз и длина стежка уменьшается.
Высота подъема рейки 46 над, игольной пластиной регулируется поворотом рычага 42 после ослабления винта 29 крепления коромысла 31 к валу подъема 43.
Усилие прижатия лапкой 7 (см. рисунок 27) материала регулируется регулировочным винтом 9. При завинчивании винта 9 усилие прижатия материала лапкой 7 возрастает.
Своевременность подъема и продвижения рейки 46 (см. рисунок 26) регулируется поворотом эксцентриков подъема 34 и продвижения 36 после ослабления винтов их крепления на нижнем распределительном валу 26.
Положение рейки 46 вдоль прорези в игольной пластине регулируется после ослабления винтов 29 и 9 крепления коромысел 31 и 10 соответственно на валах подъема 43 и продвижения 8.
Положение рейки 46 в прорези игольной пластины в поперечном направлении устанавливается ослаблением винтов 5и Укрепления шпилек 6 и 3 на рамке 7 вала продвижения 8 и при дальнейшем смещении рычага-вилки 47 с рейкой 46.
Соответствие длины стежка указателю на рукаве достигается установлением положения «О» рукояткой 24 и после ослабления винта 77 поворотом рычага 40 с осью 39 и выводом ее на плоскость расположения оси 16 и винта 11. Рейка 46 не должна горизонтально перемещаться над игольной пластиной.
Положение прижимной лапки 1 (см. рисунок 27) по отношению к игле устанавливается после ослабления винта 18 на муфте 17 и поворотом стержня 22 совместно с прижимной лапкой 1.
Максимальный подъем прижимной лапки 1 регулируется при поднятой лапке поворотом рычага 23 после ослабления винта 18 крепления муфты 17 к стержню 22 благодаря вертикальному смещению стержня 22. Максимальный подъем лапки 1 должен соответствовать технической характеристике машины, приведенной выше.
Системы смазывания швейной машины. В швейной машине 97-А
реализована автоматическая подача масла к трущимся деталям в рукаве машины (рисунок 28). В машине для этого установлен шиберный насос 6. Корпус насоса прикреплен к платформе машины. Лопасти насоса вращаются через червячную передачу 10 от нижнего распределительного вала 5. Масло подается по распределительным пластмассовым маслопроводам к трущимся поверхностям деталей. Масло поступает по трубопроводу через фильтр 7, опущенный в картер с маслом.
При нормальной работе насоса и при наличии масла в картере машины масло должно струей ударяться в прозрачный колпачок /, расположенный на рукаве машины. Это позволяет наблюдать за работой системы смазывания.
Поданное от насоса по маслопроводу 2 в рукав машины масло заполняет пространство между втулкой и главным валом, а также смазывает шарикоподшипники и игольчатый подшипник в механизме иглы. Излишки масла через фитиль поступают в правый шарикоподшипник на главном валу машины. Масло по отводящим маслопроводам 3 и 4 поступает обратно в картер машины.
Рис.28. Схема централизованной системы смазывания механизмов
По маслопроводу 9 в платформе машины от насоса 6 масло поступает во втулку механизма челнока, где оно распределяется для смазывания шестерен, челночного вала-шестерни и челночного устройства.
По маслопроводу 8 масло подается для смазывания игольчатых подшипников механизма двигателя ткани.
При эксплуатации машины необходимо следить через прозрачный колпачок 1 за работой системы смазывания и при уменьшении количества масла в картере своевременно его дополнять. Для смазывания используется масло индустриальное И-12А и И-20А.
Швейная машина класса 1022 М АО «Орша» (Беларусь) является базовой машиной конструктивно-унифицированного ряда машин, предназначенных для обработки материалов строчкой двухниточного челночного переплетения. Характеристика машин данного ряда представлена в таблице 4.
Таблица. 4.
Параметры машин конструктивно-унифицированного ряда, построенных на базе машин класса 1022М АО «Орша» (Беларусь)
Параметр | |||||||
Максимальная часто- | |||||||
та вращения главного | |||||||
вала машины, мин -1 |
|||||||
Окончание таблицы 4
Параметр | |||||||
Длина стежка, мм | |||||||
Максимальная высота | |||||||
подъема прижимной | |||||||
лапки, мм | |||||||
Максимальная тол- | |||||||
щина обрабатывае- | |||||||
мых материалов, мм | |||||||
Мощность двигателя, | |||||||
Напряжение питания, | |||||||
Примечание. Для машин классов 1022М и 1022Н применяют иглы 0092- 02-90, 0092-02-100, 0092-02-110, 0092-02-120, 0092-02-130, 0092-02-150; для машин классов 1022МПК и 1022НА - 0319-02-90, 0319-02-100, 0319-02-110, 0319-02-120, 0319-02-130, 0319-02- 150; для машин класса 1022М-3 - 0319-02-90, 0319-02-100, 0319-02- 110; для машин класса 1022М-4 - 0319-02-120, 0319-02-130, 0319- 02-150.
Машины классов 1022М, 1022Н, 0-1022МС, 1022НА рассчитаны на обработку средних и среднетяжелых тканей, машины класса 1022МПК - также и легких тканей, машины класса 1022М-3 предназначены для пошива легкого платья, класса 1022М-4 - для работы с пальтовыми тканями.
Машина класса 1022Н имеет систему автоматического смазывания от встроенного насоса. Машины классов 1022М-3 и 1022М-4 оснащены окантовывателями. Машина класса 1022М-3 предназначена для окантовывания деталей легкого платья полоской ткани, выкроенной под углом 45° к основе, а машина класса 1022М-4 - для окантовывания деталей пальто полоской ткани или трикотажной лентой. Подача бейки с бобины и стабилизация натяжения ее перед входом в формователь осуществляется автоматически. Машина класса 0-1022МС оснащается средствами автоматизации по останову машины, обрезке ниток и подъему прижимной лапки. Машина класса 1022МПК предназначается для индивидуальных производителей, малых предприятий. Машина класса 1022НА обеспечивает высокую производительность благодаря автоматизации обрезки ниток и выполнению закрепки в строчке.
Машина класса 1022М имеет вылет рукава 245 мм. Длина стола не превышает 1060 мм, ширина - 575 мм. Высота регулируется от 745 до 825 мм. Высота машины со столом регулируется в пределах 1470... 1550 мм. Масса машины со столом и электроприводом - не более 108 кг.
Заправка ниток и регулировка их натяжения. Заправка игольной нитки (см. рисунок 29) осуществляется от бобины с игольной ниткой, установленной
на стойке. Нитка 5, проведенная через глазок в стойке, поступает к нитенаправителю. Заправленная в глазки нитенаправителя и проведенная между тарелочками устройства предварительного натяжения 4 нитка поступает к нитенаправителю 3, а от него - к регулятору натяжения 75. Проведенная между шайбами 14 регулятора и заброшенная за крючок компенсационной пружины и под крю- чок-нитенаправитель 13 и нитенаправитель 16 нитка заправляется в глазок нитепритягивателя 2. Далее от нитепритягивателя 2 нитка проводится через нитенаправитель 1 на рукаве машины и проволочный нитенаправитель 18, установленный на игловодителе, и заправляется в ушко иглы 17.
Рис. 29. Схема заправки игольной нитки
Челночная нитка со шпулькой имеет заправку, аналогичную машине класса 97-А.
Для намотки челночной нитки на шпульку в машине класса 1022М установлена в рукаве моталка 11. Нитка 7от стойки заправляется в нитенаправитель с регулятором натяжения б и обводится 3...4 раза вокруг шпульки 8, которая устанавливается на вал моталки. Для включения моталки нажимают на шпульку 8, и она смещается с валом в корпус моталки. Для фиксации наполнения шпульки 8 используется рычаг 12, закрепленный стягивающим винтом 10 на оси моталки. При наполнении шпульки 8 рычаг 12 поворачивается против часовой стрелки и отключает вращение вала моталки со шпулькой 8. Рычаг 12 выходит из контакта с нитками в шпульке. Шпулька 8 смещается от корпуса моталки.
В машине возможно регулирование натяжения игольной нитки поворотом гайки в регуляторе натяжения 75. Вращая гайку по часовой стрелке, увеличивают натяжение игольной нитки. Предварительное натяжение игольной нит-
ки в регуляторе 4 не должно превышать натяжение, создаваемое основным регулятором 15 натяжения.
Регулировка натяжения челночной нитки выполняется регулировочным винтом прижатия пластинчатой пружины на шпульном колпачке челночного устройства.
Конструкция моталки для намотки нитки на шпульку. В машине моталка установлена в рукаве немного выше уровня главного вала. Корпус моталки 11 закреплен в рукаве двумя винтами 9 (см. рисунок 30).
Рис.30. Схема устройства для намотки челночной нитки
На главном валу 1 для привода вала 2 моталки установлен червяк 19, который взаимодействует с червячным колесом 3. Червячное колесо 3 закрепляется на валу 2 винтом 4. На вал 2 надета втулка 18. В прорезь вала 2 с переднего его конца вставлена пружина 9 и закреплена на нем заглушкой 10. Втулка 18 проходит в корпусе 8 моталки. Втулка 18 и профильный вал 2 сжаты пружиной 6, расположенной на валу 2 и закрепленной в корпусе 8 внутренним кольцом 5. В корпусе 8 имеется поперечный вырез 14, в котором проходит кулачок 77. Кулачок 7 7 закреплен на оси 13. На переднем конце оси 13, выходящей из корпуса 8, закреплен стягивающим винтом 77 рычаг-защелка72 На кулачок 7 7 воздействует пружина 16, один конец которой прикреплен к кулачку 77, а другой
К шпильке, установленной на корпусе 8моталки. Кулачок 77 имеет вырез, в котором располагается шарик 15. Шарик 75 в рабочем положении втулки 18 попадает в конусную ее расточку 7.
При намотке нитки шпульку устанавливают на валу 2 с прорезью, надавливают, и она совместно с втулкой 18 и валом 2 смещается к главному валу 7. Червячное колесо 3 смещается к червяку 4 и взаимодействует с ним. При этом
коническая расточка 7на втулке 18 подходит к вырезу 14 корпуса 8. Шарик 75 под действием кулачка 77 входит в вырез. Давление кулачка 77 на шарик 75 обеспечивается пружиной 16. Рычаг-защелка 12 входит между боковыми стенками шпульки и контактирует с витками нитки на шпульке. При наполнении шпульки рычаг-защелка, повернувшись против часовой стрелки, освобождает кулачком 17 шарик 15 из расточки 7 втулки 18. Втулка 18 под действием пружины 5 смещается вдоль своей оси. Конусная расточка /позволяет окончательно вытолкнуть шарик 75 из расточки 7, что приводит к выводу рычага-защелки 12 из шпульки и далее к выводу из зацепления червячного колеса 3 с червяком 4. Шпулька с намотанной челночной ниткой смещается от корпуса 8 моталки. Швея снимает шпульку с вала 2 и отрезает нитку.
Степень наполнения шпульки ниткой регулируется изменением угловой ориентации рычага-защелки 12 после ослабления стягивающего винта 11 на оси 13. Поворачивая рычаг-защелку 12 против часовой стрелки, увеличивается количество ниток на шпульке, а по часовой стрелке - уменьшается.
Плотность намотки нитки на шпульке регулируется гайкой на регуляторе натяжения б (см. рисунок 29).
Равномерность намотки на шпульку обеспечивают смещением регулятора 6 от корпуса машины или к нему после ослабления винта крепления стержня регулятора в корпусе машины.
В машине класса 1022М применяется кривошипно-ползунный механизм иглы 4 (см. рисунок 31).
В машине класса 1022М используется центрально-шпульный равномерно вращающийся тип механизма челнока 1. Челночное устройство 1 приходит во вращение от главного вала 10 машины через зубчато-ременную передачу 11, нижний распределительный вал 12, зубчатую передачу 13 и челночный вал 14. Механизм имеет регулировку своевременности захвата игольной петли и выполнения гарантированного зазора А между иглой и носиком челнока.
Рис.31. Схема машины класса 1022М
В машине используется кривошипно-коромысловый (кривошипнорычажный) механизм нитепритягивателя 8 (рисунок 31). Рычаг нитепритягивателя 8приходит в движение от пальца 5 кривошипа 9, установленного на главном валу 10. Между пальцем 5 и нижней головкой нитепритягивателя 8 вложен игольчатый подшипник. На средней части нитепритягивателя 8ь его отверстие вставлена ось от звена 7. Во второе отверстие звена /вставлена шпилька 6, которая закреплена в корпусе винтом.
В машине используется двигатель ткани реечного типа, состоящий из следующих узлов: подъема, продвижения рейки 2, регулировки длины стежка и обратного хода (выполнения закрепки) и прижимной лапки 3.
Эксцентрик подъема 31 (см. рисунок 32) выполнен в едином исполнении
с эксцентриком 32 продвижения и закреплен двумя винтами на нижнем распределительном валу 24. На головках эксцентриков 31 и 32 имеются игольчатые подшипники. На подшипниках эксцентрика 31 расположена головка шатуна 25. Через второе, меньшее, отверстие в шатуне 25 так же, как и через отверстия рычага-вилки 27, проведена ось 28 и закреплена винтом 29. Рычаг-вилка 27 закрепляется стягивающим винтом 26 на валу продвижения 40, который в двух втулках проходит в платформе машины. На левой стороне вала устанавливается передний рычаг 39 и закрепляется стягивающим винтом 38. Для устранения осевого смещения на валу 40 закрепляется вплотную к втулке, запрессованной
в платформе машины, установочное кольцо 30. Рычаг 39 через ось соединен со звеном 43, в нижние отверстия которого также вставлена ось 42, соединяющая звено 43 с балкой 45. Ось 42 закрепляется в балке 45 стягивающим винтом 41.
К балке 45 двумя винтами крепится рейка 44.
Рис.32. Кинематическая схема механизма перемещения зубчатой рейки.
В узел продвижения рейки 44 входит эксцентрик продвижения 32, на игольчатом подшипнике которого расположена большая головка шатуна 33. В меньшее отверстие шатуна 33 вставлена ось 11, которая проходит через звено 36 и закрепляется в звене двумя винтами 12 и 10. В нижнее отверстие звена 36 вставлена ось 34, которая проходит также через звено-рамку 35. В левое верхнее отверстие звена-рамки 35 вставлена шпилька 9, которая закрепляется в платформе винтом 37. А в правое верхнее отверстие звена-рамки 35 вставлен вал 14 узла обратного хода. Звено-рамка 35 закреплено стягивающим винтом 13 на валу 14 обратного хода.
Ось 11 проходит через соединительное звено 8, в дальнее отверстие которого проведена ось, соединяющая его с рычагом-вилкой 6. Рычаг-вилка 6 закрепляется стягивающим винтом 7 на валу продвижения 4. Вал продвижения 4 проходит в двух втулках в платформе машины. На левой стороне вала закрепляют с помощью винта 46 вертикально рычаг-рамку 7. Рычаг-рамка 7 через ось 3 шарнирно соединена с балкой 45. Ось 3 крепится стягивающим винтом 2 в балке 45. Для устранения осевого смещения на валу 4 закрепляется вплотную к втулке, запрессованной в платформе машины, установочное кольцо 5.
Рейка 44, взаимодействуя с узлами продвижения и подъема, получает эллипсообразную траекторию движения. Единое исполнение эксцентриков двух узлов позволяет получать наиболее рациональное согласование движений по вертикали и горизонтали.
Горизонтальное перемещение рейки 44 определяется положением оси 34. Чем больше отклонения оси от плоскости расположения оси 77 и оси соединения рычага-вилки 6 и звена 8, тем больше горизонтальное перемещение рейки 44. Для изменения положения оси 34 служит узел регулятора длины стежка. Вал 14 проходит в платформе машины и на правом конце имеет запрессованный рычаг 23, который через шарнирный винт соединен с тягой 17. В отверстие верхнего конца тяги вставлен шарнирный винт, подвижно соединяющий тягу 77 с двуплечим рычагом 18, на переднем конце которого расположена втулкауказатель 20. В ее винтовую часть вставляются рукоятка 19 и гайка 21. Рукоятка 19 штифтом закрепляется на рычаге 18.
Для предотвращения самопроизвольного изменения длины стежка в рукоятке 19 установлен ролик 22, поджатый к наружной поверхности гайки 21 пружиной, которая вставлена во внутреннее отверстие рукоятки 19. Для этих же целей на валу 14 двумя винтами закрепляется установочное кольцо 15, имеющее боковое отверстие, в которое входит левый конец пружины 16, а ее правый конец упирается в платформу машины. Чем больше закручена пружина 16, тем устойчивее рычаг 18 с рукояткой 19 занимают крайнее верхнее положение.
Узел прижимной лапки 1 располагается в левой части рукава машины(см. рисунок 33). Прижимная лапка 7 крепится винтом 2 к стержню 20, который проходит во втулке, закрепленной в рукаве и в полом стержне-винте 7. Верхняя часть винта 7 выступает над рукавом и служит для регулировки давления прижимной лапки 7 на материал. Винт 7 давит на пружину 24, которая находится
Рис.33. Кинематическая схема узла прижимной лапки.
на более тонкой его нижней части. Пружина 24 воздействует на кронштейн 23, который стягивающим винтом 5 закреплен на стержне 20. Плоский выступ на кронштейне 23 входит в вертикальный паз в рукаве машины. На кронштейне 23 закрепляется рычаг-нитенаправитель 77, который освобождает нитку при подъеме лапки. К кронштейну 23 крепится угловой нитенаправитель 77. Для разжатия шайб (тарелочек) в регуляторе натяжения на кронштейне 23 в передней части выполнен выступ 22, который может контактировать с двуплечим рычагом 18, установленным на оси 19 в рукаве машины. Двуплечий рычаг 18 прижимается к выступу 22 под действием пружины сжатия 16. Ниже кронштейна 23 на стержне 20 расположен рычаг 21. Его плоский выступ так же, как у кронштейна 23, входит в вертикальную прорезь в корпусе машины. На рычаг 21 снизу может действовать рычаг подъема 3 лапки, который закреплен на оси 4 в рукаве машины.
Для коленного подъема лапки к рычагу 21 через шарнирный винт присоединена нижняя головка звена 6. Верхняя головка звена 6 надета на стержень 9, который приварен к рычагу 10 (13). Рычаг 10(13) удерживается на шарнир-
ном винте 8 и шпильке 11, вставленной во вставку 12. В правый выступ рычага 13 вставлен верхний конец тяги 15 и зафиксирован разводным штифтом 14.
Нижний конец тяги 75 проходит через отверстие в платформе машины, снизу на тяге 75 имеются пружина 25 и шайба 26. Шайба 26 также зафиксирована разводным штифтом.
При нажатии на рычаг для коленного подъема лапки тяга 75, поднимаясь, поворачивает рычаг 13 против часовой стрелки и через звено 6, рычаг 21 и кронштейн 23 поднимает стержень 20, а вместе с ним - и прижимную лапку 7.
Длина стежка в машине 1022М регулируется поворотом рифленой гайки на рукоятке регулятора. При закручивании гайки 21 рукоятка 19 смещается вниз и длина стежка уменьшается.
Подъем рейки 44 над игольной пластиной регулируется поворотом рычага 39 после ослабления винтом 38 его крепления к валу подъема 40.
Усилие прижатия лапки 7 к материалу регулируется регулировочным винтом 7. При завинчивании винта 7 усилие прижатия материала лапкой 7 увеличивается.
Своевременность подъема и продвижения рейки регулируется поворотом эксцентриков подъема и продвижения соответственно после ослабления винтов их крепления на нижнем распределительном валу.
Положение рейки 44 вдоль прорези в игольной пластине регулируется после ослабления винтов 38 и 46 крепления рычагов 39 и 7 соответственно на валах подъема 40и продвижения 4.
Положение рейки 44 в прорези игольной пластины в поперечном ее направлении устанавливается после ослабления винтов 38 и 46 крепления рычагов 39 и 1 соответственно на валах подъема 40 и продвижения 4 и при дальнейшем смещении этих рычагов совместно с балкой 45 и рейкой 44.
Соответствие длины стежка указателю на рукаве достигается установкой рукоятки 19 в положение «О» и после ослабления винта 13 поворотом рычага 35 с осью 34 в плоскость расположения оси 77 и оси соединения рычага 6 со звеном 8. Рейка 44 при этом положении рукоятки 19 не должна горизонтально перемещаться над игольной пластиной.
Положение прижимной лапки 7 по отношению к игле устанавливается после ослабления винта 5 на кронштейне 23 поворотом стержня 20 совместно с прижимной лапкой 7.
Максимальный подъем прижимной лапки регулируется после ослабления винта 5 крепления кронштейна 23 к стержню 20 при поднятой лапке от поворота рукоятки 3 благодаря вертикальному смещению стержня 20. Максимальный подъем должен соответствовать технической характеристике машины.
Системы смазывания швейной машины. В швейной машине 1022М применяется смешанная система смазывания: челнок смазывается в результате разбрызгивания масла и подачи его по специальным направителям к челночному устройству; отдельные детали смазывают капельным способом (трущиеся поверхности деталей).
Рис.34. Схема системы смазывания деталей в механизме челнока.
Челночное устройство 1 (см. рисунок 34) смазывают так же, как и в машине класса 97-А. Масло из картера по фитилю 6, закрепленному на втулке 4, поступает на челночный вал 3 и по наружному винтообразному каналу 5 поступает через вертикальный канал 8 во втулке 4 во внутренний канал 10 челночного вала 3. Масло поступает по каналу 10 на выход из челночного вала 3, который в отличие от механизма челнока машины класса 97-А не перекрыт винтом. Далее масло попадает в канал 2 в челночном устройстве 1 и по нему - на соединение корпуса челночного устройства 1 со шпуле-держателем 11. Количество поступающего масла в челночное устройство 1 зависит от степени перекрытия винтом 9 вертикального канала 8. Чем больше ввинчен винт Рв корпус втулки 4, тем меньше смазывается челночное устройство 1. Излишки масла по горизонтальному каналу 7 во втулке 4 возвращаются на правый конец челночного вала 3 в месте его контакта с фитилем 6.
Базовая швейная машина челночного стежка конструктивноунифицированного ряда 31.
Для уменьшения затрат на производство машин различного технологического назначения, но имеющих единое функциональное назначение основных механизмов, в СКБ АО «Орша» (Беларусь) под руководством Л. К. Милосердного был разработан конструктивно-унифицированный ряд (КУР) машин по модульно-блочному принципу.
Все машины в соответствии с толщиной обрабатываемого материала разделены на три группы: легкие - для обработки пакета толщиной до 3 мм, средние - до 5 мм и среднетяжелые - до 7 мм. Толщина материала определяет конструктивные размеры механизмов иглы и двигателя ткани, а также тип механизма нитепритягивателя (для легких тканей используется фасонный нитепрйтягиватель).
В основу разработки КУР положен блочно-модульный принцип построения: машина создается из конструктивных модулей, каждый из которых имеет свое функциональное назначение. На создание 43 швейных машин различного назначения КУР 31 предусматривает примерно 25 модулей.
Базовой машиной КУР 31 является швейная машина класса 31-12+3, которая состоит из 11 модулей. Швейная головка машины включает в себя сле-
дующие модули: корпус, унифицированный для всех машин ряда; зубчатоременная передачу от главного вала к нижнему распределительному валу; насос для подачи масла из картера в рукав машины и к местам смазывания; механизм игловодителя с общим расстоянием перемещения иглы 32 мм; кривошип- но-шатунный нитепритягиватель; механизм перемещения нижней рейки (узлы подъема и перемещения рейки); узел прижимной лапки; узел регулировки длины стежка; механизм отводчика шпуледержателя. Промышленный стол к швейной машине состоит из следующих модулей: станина с крышкой и педаль или коленоподъемник для подъема прижимной лапки. Для неавтоматизированных швейных машин используется электрофрикционный привод, выполненный в виде самостоятельного модуля.
Таблица 5
Техническая характеристика швейных машин общего назначения КУР 31 АО «Орша»
Параметр | Классмашины | |||
Обрабатываемые материалы | Сорочечные, | Костюмные | Шинельные, |
|
платьевые, | пальтовые |
|||
бельевые | ||||
Максимальная толщина об- | ||||
рабатываемых материалов, мм | ||||
Частота вращения главного вала, мин1 | ||||
Длина стежка, мм | ||||
Максимальная высота подъема лапки, | ||||
не менее, мм | ||||
Номер применяемых игл | ||||
Применяемые нитки: хлопчатобу- | ||||
мажные шелковые | №33а №ЗЗЛ | |||
Потребляемая мощность электро- | ||||
двигателя, кВт | ||||
Масса, не более, га- | ||||
Размеры машины, не более, мм: дли- | ||||
на ширина высота (регулируется) |
На швейных машинах, предназначенных для пошива более тяжелых материалов (класс 31-13+3), в механизме игловодителя меняется кривошип, что позволяет увеличить ход иглы до 35 мм, а также снимается механизм отводчика. При пошиве материалов толщиной менее 3 мм (машина класса 31-11+3) используется ротационный фасонный нитепритягиватель. Техническая харак-
теристика швейных машин КУР 31с продвижением материала рейкой представлена в таблице 5.
Заправка ниток в машине. Заправка игольной нитки в швейной машине класса 31-12+3 начинается с установки бобины на стойке также, как и в машинах классов 97-А и 1022М. От нитенаправителя на стойке нитка 1 (рисунок 35, а) заправляется в нитенаправитель 2 на рукаве машины, проходя между шайбами регулятора 3 предварительного натяжения нитки, далее - в нитенаправитель 10 и регулятор натяжения 9. Нитка набрасывается на крючок компенсационной пружины и под крючок нитенаправителя. От него нитка вдевается в глазок нитепритягивателя 4 и далее - в нитенаправитель 5 на фронтальной крышке машины, за нитенаправитель 6, установленный на игловодителе, и в ушко иглы 7.
Заправка челночной нитки и установка шпульки аналогичны машинам классов 97-А и 1022М.
Рис.35. Общий вид швейной машины класса 31-12+3, схема заправки игольной нитки при образовании строчки (а) и челночной нитки
при ее наматывании на шпульку (б)
Общие принципы наладки механизмов швейной машины. Наладку машины начинают с основный механизмов, переходя к дополнительным и элементам автоматизации. Центральным в машине челночного стежка является механизм иглы. После него налаживают механизмы челнока, двигателя ткани и нитепритягивателя.
Сначала проверяют соответствие использования машины и органов технологической характеристике машины. Для всех механизмов на первом этапе проверяется правильность сборки и отсутствие заклинивания, соударений и заеданий в шарнирах механизма и других очевидных дефектов.
На втором этапе проверяют выполнение траекторий движения основных рабочих органов и рабочих органов устройств. При необходимости осуществляют регулировку траектории движения рабочих органов.
На третьем этапе осуществляется согласование движений рабочих органов. На этом этапе можно использовать циклограммы и диаграммы согласования нитки.
На четвертом этапе уточняют взаимные положения рабочих органов. После пробной обкатки машины на холостом ходу в случае отсутствия
дефектов (шум, вибрация и др.) проверяют качество и безотказность выполнения технологической операции. Если параметры отказов превышают паспортные данные, то выполняют необходимую регулировку.
В машинах челночного стежка общего назначения при выпуске с заводаизготовителя допускаются следующие параметры дефектов и отказов: не более одного обрыва ниток на строчке длиной 45 м; не более 2 % посадки т. е. смещения равной длины слоев ткани друг относительно друга; не более 2 % стягивания, т.е. укорачивания длины образца по сравнению с длиной до стачивания; не более 10 мм отклонения от прямой линии строчки длиной 300 мм.
Из-за износа деталей при длительной эксплуатации швейных машин данные параметры могут быть не достигнуты без замены деталей новыми. Поэтому допустимые параметры дефектов и отказов принимают, руководствуясь экономической целесообразностью. Затраты по замене деталей должны оправдываться получаемой эффективностью по надежности и качеству ее работы, что особенно актуально при эксплуатации машин в процессах с длительными простоями оборудования, при высокой стоимости деталей и др.
Наладка механизмов швейной машины по калибрам. Наиболее удобной является наладка механизмов, модулей машины по калибрам. Однако этот способ требует наличия в механизмах специальных установочных положений и калибров к машине. В машинах КУР 31 предусмотрено выполнение наладки по калибрам.
Рис.36. Схема установки рамки в рукаве по калибрам для швейных машин конструктивно-
Рассмотрим наладку механизма иглы . Установка рамки в рукаве машины предусмотрена по калибрам. Для этого на местигольной пластины устанавливается калибр 1 (рисунок 36, а), а вместо иглы - калибр-стержень 2. Ослабив винты 5и Укрепления рамки в рукаве, устанавливают рамку 3 так, чтобы стер- жень-калибр 2 проходил в отверстии калибра 1. При выполнении этого условия винты 5 и 4 следует закрепить.
В машинах серий 31 и 131 с отклоняющейся иглой перед установкой рамки 3 необходимо дополнительно" прошить калибром 6 (рисунок 36, б) шатун 7 узла отклонения иглы.
Для установки высоты иглы в игловодитель на место иглы устанавливают калибр-стержень 7 (см. рисунок 37). Крепление игловодителя 2 в поводке 5 освобождают стягивающим винтом 4. Вращая шкив машины, выводят челнок на захват игольной петли. Игловодитель 2 располагают по высоте так, чтобы калибр 1 упирался в носик 11 челнока. Далее в отверстие 6 в кривошипе 7 вставляют калибр 8, который должен пройти не только через отверстие 6 кривошипа 7, но и через верхнее отверстие 9 в рукаве машины. Винт 4 на поводке закрепляют.
Рис.37. Схема установки высоты иглы по калибрам для швейных машин конструктивно-унифицированных рядов 31 и 131
При наладке механизма двигателя ткани учитывают, что расположение рейки в пазах игольной пластины зависит от расположения балки 10(см. рисунок 36), на которой устанавливается рейка. Для точной установки балки 10 к нижней поверхности калибра 1 (единый калибр для установки рамки механизмов иглы и рейки) запрессован палец 9. Для корректировки положения рейки необходимо ослабить винты 12 крепления рычага-рамки 13 узла продвижения на валу 11 и изменить его положение так, чтобы палец 9 вошел в дальнее от
оператора отверстие, предназначенное для крепления рейки на балке 10. После регулировки винты 12 затянуть.
унифицированных рядов 31 и 131
При наладке механизма нитепритягивателя двухколенчатый палец 2 (рисунок 38) в кривошипе 1 устанавливают, выполняя следующие операции: подбирают диаметр А калибра - согласно таблице 6; на оси звена механизма нитепритягивателя располагают калибр 4 диаметром А; колено пальца 2 прижимают к калибру 4; винтом 3 палец 2 закрепляют в кривошипе 1.
Таблица 6.
Параметры калибра для установки | ||||
двухколенчатого пальца механизма нитепритягивателя | ||||
Классмашины | Ходглазка, мм | Параметрыкалибра |
||
Маркировка | А, мм |
|||
Наладка механизма челнока включает в себя следующие операции. Для установки своевременности подхода носика челнока 11 (см. рисунок 37) к игле 1 используют отверстия 6 и 5 в кривошипе 7 и в рукаве 9 (так же, как при установке иглы по высоте). Оба отверстия «прошивают» калибром 8. Освободив винты 12 крепления челнока на челночном валу, устанавливают челночное устройство так, чтобы его носик 11 подходил к игле 1 (калибр заменен иглой). Винты 12 закрепляют.
В процессе наладки механизма двигателя ткани определяют значение подъема зубьев рейки над игольной пластиной.
Для установки своевременности продвижения рейки по отношению к игле ослабить винты 1 крепления эксцентриков 2 механизма двигателя ткани. Оси рамки 3, вала 10 и втулки 11 выводят на одну линию и в них проводят ка-
либр-стержень 9. Вращая шкив машины, выводят кривошип 7 так, чтобы его отверстие 6 совпало с нижним отверстием 10 в рукаве, и в эти отверстия вставляют калибр-стержень 8. В этом положении механизмов закрепляют один из винтов 1 крепления эксцентриков 2 двигателя ткани. Затем вынимают калибр 9, проходящий через вал 10 обратного хода и завертывают второй винт 1 крепления эксцентриков 2.
Для установки соответствия показаний длины стежка на шкале пластины действительному значению рычаг б регулятора длины стежка устанавливают в положение «О». Ослабляют винт крепления рычага 7 и поворачивают рамку 3 с противовесом так, чтобы оси соединительного звена 5 и оси прокачивания зве- на-рамки 4ъ рамке 3 с противовесом были на одной линии. Через них проводят калибр-стержень 8. Завинчивают винт крепления рычага 7 на оси рамки 3 с противовесом.
Рис.39. Схема установки рукоятки регулятора длины стежка по калибрам для швейных машин конструктивно-
унифицированных рядов 31 и 131
После каждой регулировки калибры удаляют.
Для обработки тканей с различными механическими свойствами в швейной машине предусмотрены: смена ниток по номеру или цвету, их натяжения, частоты строчки, номера и формы острия иглы; применение лапок со специальным покрытием; выполнение технологических регулировок в машине и др. Для особых материалов (труднотранспортируемых, легкорастяжимых и др.) и выполнения специальных операций (стачивание с одновременной обрезкой края материала, стачивание с посадкой и др.) существуют специализированные швейные машины челночного стежка.
Швейные машины с дифференциальной подачей материала
Швейные машины челночного стежка с дифференциальной подачей материала предназначены для устранения стягивания или посадки материала и
получения нормально затянутой строчки при пошиве легкодеформируемых материалов.
Особенности рабочего процесса. При образовании стежка материал испытывает со стороны ниток сжатие, что может привести к формированию стежка с утянутой структурой. Это влечет стягивание материала по линии строчки. Формирование стежка на материале, который растянут, может привести к тому, что после выхода его из-под лапки стежок будет не затянут. Регулирование натяжения ниток при растяжении стежка может вызвать их обрыв. При пошиве легких или рыхлых материалов происходит припосаживание нижнего слоя материала из-за растяжения верхнего слоя подошвой прижимной лапки. Поэтому в швейных машинах для формирования нормальной структуры стежка для стачивания легкодеформируемых материалов качественной строчкой челночного стежка применен дифференциальный тип двигателя ткани.
Швейные машины с обрезкой края материала
Для формирования строчки на определенном расстоянии В от края материала при одновременном его выравнивании в машинах челночного стежка устанавливается модуль обрезки материала. Процесс резания материала на швейной машине. В швейных машинах реализовано в основном резание способом ножниц, т.е. когда имеются два лезвия (верхнее и нижнее), периодически взаимодействующие друг с другом и обрезающие край материала. При отсутствии плотного контакта между лезвиями ножей материал разрезается способом прорубания, что требует более острой заточки верхнего ножа.
Швейные машины с отклоняющейся иглой
К швейным машинам с отклоняющимися иглами относятся специализированные машины челночного стежка с горизонтальной осью вращения челночного устройства, а также специальные швейные машины с вертикальной осью вращения челночного устройства для выполнения соединения деталей одной или двумя параллельными строчками челночного переплетения. Игла в этих машинах имеет отклонение по направлению транспортирования материала.
Вопросы для самопроверки
1. Каковы основные отличия между базовыми машинами классов 97- А, 1022М и 31-12+3 по техническому назначению?
2. Как заправляют игольную и челночную нитку в машинах 97-А, 1022М и 31-12+3 класов?
3. Какие регулировки можно выполнить в моталке?
4. Как регулируются механизм иглы, челнока и двигателя ткани?
5. Какие характеристики работы машины можно использовать ри её наладке?
Каждая швейная машина имеет свою отличную от других марок машин инструкцию, но большинство машин эконом класса, с качающимся челноком (как у швейной машинки Чайка): Brother, Jaguar, Singer, Veritas, Janome, Husqvarna и других марок имеют практически одинаковое устройство.
Правила по эксплуатации, заправка нитки, переключение операций, установка шпульного колпачка, смазка и уход и т.д. в инструкции таких швейных машин практически одинаковые.
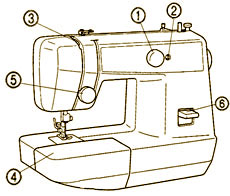
Основные части швейной машины:
1. Ручка выбора вида строчки. С помощью этой ручки вы устанавливаете необходимый вид строчки: прямая, штопка, зигзаг или смещение иглы для пришивания молнии, выполнение петли и др.
2. Винт точной настройки выметывания петель. Не у каждой машинки бывает такая регулировка. Она предназначена для выравнивания частоты (густоты) строчки зигзаг при выполнении петли. То есть, в одном из направлений зигзаг будет реже, поэтому прежде чем выполнять петлю, проверьте ее на обрезке такой же ткани. И если необходимо выполните регулировку.
3. Рычаг нитепритягивателя.
4. Съемный столик с отделением для хранения принадлежностей.
5. Дисковый регулятор натяжения верхней нитки .
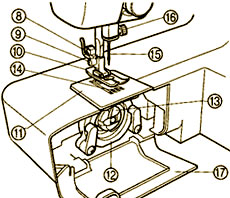
6. Клавиша движения ткани в обратном направлении.
7. Приспособление для обрезки нити. Очень удобное приспособление, но требующее определенной привычки. Обычно им редко пользуются, просто забывая про него, обрезая нитку ножницами.
8. Узел адаптера прижимной лапки.
9. Винт крепления адаптера прижимной лапки.
10. Прижимная лапка.
11. Игольная пластина.
12. Челночный узел.
13. Шпульный колпачок.
14. Гребенки (рейка) транспортера ткани.
15. Швейная игла .
16. Винт иглодержателя.
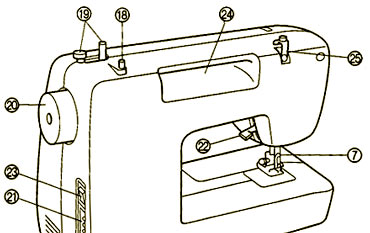
17. Крышка челночного устройства.
18. Стержень для установки катушки.
19. Устройство намотки шпулек.
20. Маховое колесо.
21. Гнездо подключения педали.
22. Рычаг прижимной лапки.
23. Выключатель питания и лампочки подсветки.
24. Встроенная ручка для переноски.
25. Направляющая нити, регулятор натяжения нити при намотке на шпульку.
Принадлежности и аксессуары швейной машины
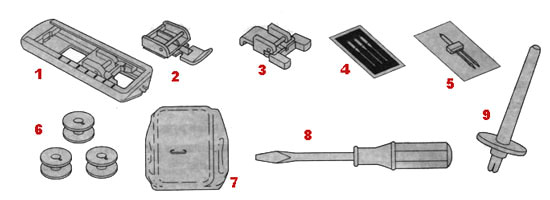
1. Лапка для выметывания петель. Специальная лапка, с помощью которой удобно выполнять изготовление петель. Размер петли зависит от размера пуговицы, вложенной в нее. В недорогих моделях швейных машин, выметывание петли производится в 4 приема.
2. Лапка для вшивания застежки "молния".
3. Лапка для пришивания пуговиц.
4. Набор игл.
5. Двойная игла.
6. Шпульки.
7. Штопальная пластина. Эта пластина заменяет рычаг опускающий гренку. Пластина просто одевается поверх рейки, скрывая зубчики, чтобы ткань не продвигалась при работе машины.
8. Отвертка
9. Дополнительный стержень для катушки. Этот стержень необходим, когда используется двойная игла, его предназначение - устанавливать вторую катушку ниток.
Перечисленные выше принадлежности хранятся в специально предназначенном для них футляре внутри столика-приставки. Эти принадлежности предназначены для облегчения выполнения большинства швейных задач.
Инструкция по установке иглы
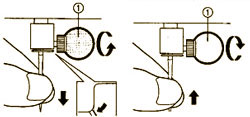
Перед установкой иглы необходимо обязательно выключить швейную машину от сети. Это необходимо выполнить особенно для неопытных, только начинающих швей.
1. Выньте вилку сетевого шнура из электрической розетки.
2. Поднимите игловодитель в крайнее верхнее положение.
3. Опустите прижимную лапку.
4. Если игла уже установлена, выньте o ее, ослабив винт иглодержателя рукой или отверткой, и потянув иглу вниз.
5. Вставьте новую иглу, плоской стороной обращенную к задней части машины, задвигая её как можно выше до упора в стопор.
6. Затяните винт иглодержателя.
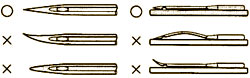
1. Для качественного шитья швейная игла обязательно должна быть прямой и острой.
2. Для проверки прямизны иглы расположите её плоской стороной вниз на ровной поверхности, как показано на рисунке.
3. Если игла погнута или затупилась, замените ее. Никогда не пытайтесь ее выпрямить или заточить. Металл, из которого сделана игла не предназначен для этого.
См. Ремонт швейных машин своими руками .
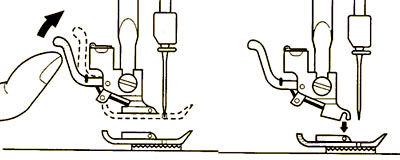
В зависимости от вида вашей работы, бывает нужно заменить прижимную лапку. Переведите сетевой выключатель в положение "О".
2. Отсоедините прижимную лапку, подняв рычажок на задней стороне узла адаптера лапки.
3. Разместите лапку на игольной пластине, чтобы поперечный стерженёк прижимной лапки находился под пазом, в нижней части адаптера лапки.
4. Опустите рычаг прижимной лапки, и зафиксируйте лапку в адаптере. Если прижимная лапка находится в правильном положении, ее стерженек защелкнется в адаптере.
Обратный ход швейной машины. Закрепка
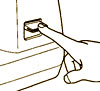
Для шитья в обратном направлении нажмите до упора клавиша шитья в обратном направлении и удерживайте ее в данном положении, слегка нажимая в это время на педаль. Для шитья в прямом направлении отпустите клавишу. Шитье в обратном направлении используется для закрепления и усиления швов. Возможно использование обратного продвижения ткани для выполнения декоративных строчек, а также выполнения штопки одежды.
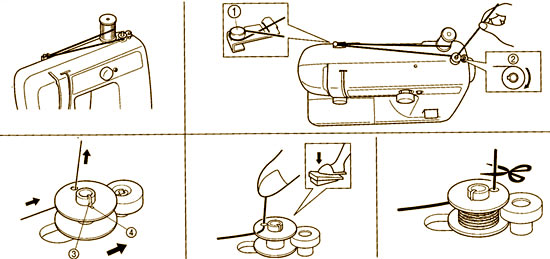
1. Установите катушку с нитками на предназначенный для нее стержень и проведите нить вокруг регулятора натяжения нити при намотке на шпульку.
2. Пропустите конец нити сквозь отверстие в шпульке с внутренней ее стороны.
3. Установите шпульку на вал устройства намотки и сдвиньте вал вправо. Вручную вращайте шпульку по часовой стрелке до тех пор, пока пружина на валу не попадет в предназначенный для нее паз на шпульке.
4. Удерживая конец нити, плавно нажмите на педаль, чтобы несколько оборотов нити намотались на шпульку. Затем остановите машину.
5. Обрежьте излишек нити над шпулькой и, нажимая на педаль, продолжите намотку нити на шпульку. Примечание: Когда шпулька заполняется нитью, машина автоматически останавливается.
6. После остановки машины разрежьте нить между шпулькой и катушкой, сдвиньте вал влево и снимите намотанную шпульку с вала. Примечание: Когда вал устройства намотки шпульки сдвинут в сторону прижимного ролика, игловодитель неподвижен, но маховик продолжает вращаться. Поэтому не прикасайтесь к маховику во время намотки шпульки.
Заправка нижней нитки в шпульный колпачок
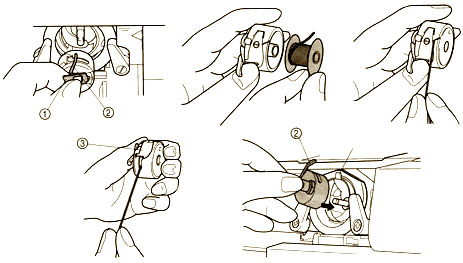
Переведите сетевой выключатель в положение "О".
1. Поднимите иглу в крайнее верхнее положение, повернув маховик на себя (против часовой стрелки), затем поднимите рычаг прижимной лапки.
2. Откройте крышку челночного устройства за столиком-приставкой с передней стороны машины, извлеките шпульный колпачок , потянув его защелку на себя и извлекая его из челнока.
3. Отмотайте приблизительно 10 см нити с полностью намотанной шпульки и вставьте шпульку в шпульный колпачок. Проденьте отмотанный конец нити в щель, затем вниз и влево, до тех пор, пока нить не попадет в отверстие под пружиной регулировки натяжения.
4. Удерживая шпульный колпачок за защелку, вставьте его до упора в челнок, после чего отпустите защелку. Следите за тем, чтобы палец шпульного колпачка вошел в предназначенный для него паз в верхней части челнока. Примечание:
Если неправильно вставить шпульный колпачок в машину, то сразу после начала шитья он выпадет из челнока.
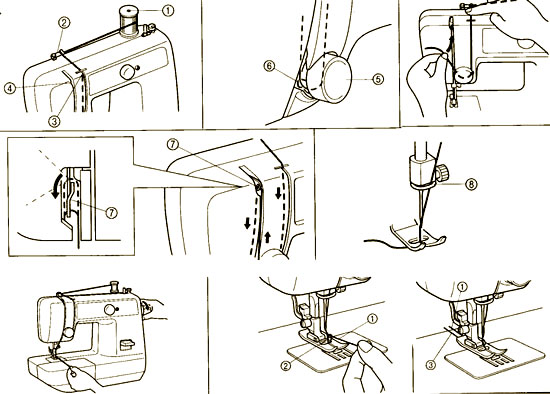
1. Поднимите рычаг прижимной лапки, пользуясь соответствующим рычагом, и поверните маховик на себя (против часовой стрелки), чтобы поднять рычаг нитепритягивателя в крайнее верхнее положение.
2. Вытяните вверх стержень для катушки и наденьте на него катушку с нитью.
3. Пропустите нить через оба нитенаправителя: сначала через задний, а потом через передний.
4. Протяните нить вниз и вокруг регулятора натяжения верхней нити справа налево так, чтобы нить зацепила ограничительную пружину. Придерживая нить, протяните ее между натяжными дисками.
5. Направьте нить к задней части рычага нитепритягивателя и далее вокруг него справа налево. Проведите нить через прорезь, вытянув ее на себя, до попадания ее в ушко нитепритягивателя.
6. Опустите нить вниз и проведите ее за нитенаправителем.
7. Заправьте нить в ушко иглы спереди назад и вытяните около 5 см ниткки. Примечание: Если нить заправлена неправильно, она может оборваться, а также могут пропускаться стежки или морщиться ткань.
Если у вашей швейной машины нет инструкции, и вы не знаете как ей пользоваться, то можете воспользоваться данным упрощенным и универсальным руководством. Данная инструкция подойдет для любой швейной машины эконом-класса с качающимся челноком, выполняющей минимальный набор операций.